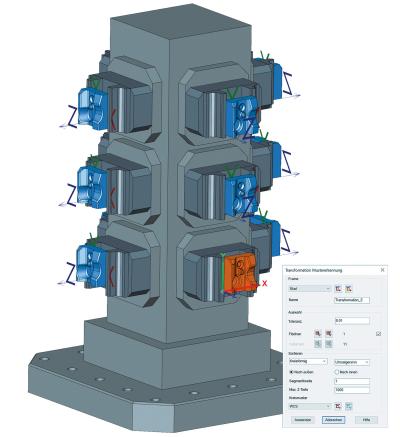
OPEN MIND Technologies, a leading developer of CAD/CAM software solutions worldwide, has introduced its latest hyperMILL® 2023 CAD/CAM software suite which offers users new and enhanced features for even more powerful and simplified NC programming in applications ranging from 2.5D machining to 5-axis milling. “We are pleased to introduce hyperMILL® 2023 to provide our customers with new, powerful CAD/CAM programming strategies, in addition to a wide range of enhancements – all designed to simplify and accelerate programming, improving the user experience,” said Mr. Alan Levine, Managing Director of OPEN MIND Technologies USA, Inc.
New and Enhanced CAM Capabilities
For easy programming of recurring shapes with a single click, hyperMILL® 2023 has a new General Transformation Pattern feature. The new feature uses a selected reference geometry and searches for the same reference in all other models regardless of its spatial orientation, creating a general transformation pattern including associated frames. This is highly useful when there are multiple components.
To ensure the highest level of safety while providing reliable programming when back boring, a new 2.5D Back Boring machining strategy enables back boring tasks to be programmed on machines with different kinematics conveniently and easily. Toolholders and inserts, as well as monobloc tools, are displayed one-to-one in the virtual machine and checked for collisions. Now programming the controller for countersinking, deburring and milling tools on the once inaccessible back side of a hole can be done with ease.
An enhanced milling surface extension is offered in hyperMILL® 2023 for “3D Z-Level Shape Finishing” and “3D Profile Finishing” strategies, ensuring high-quality and reliable surface extensions when required, even with complex geometries. Users can reliably and easily protect sharp edges and divide up machining areas, especially useful for creating high-quality surfaces in tool and moldmaking when combined with a “Smooth Overlap” feature.
New Mill-Turn Capabilities, Enhancements
New for hyperMILL® MILL-TURN capability, now “Smooth Overlap” is available for optimizing finishing paths in turning. This function enables flawless transitions when multiple tools or orientations are required for machining, and approach/ retract macros can be used normally.
Also, for more flexible, simplified programming of free-form tools, groove plunging with free tool geometry has been enhanced, as all tool geometries can now be used for any type of workpiece contour when roughing. These same tool setting options, approach and retract macros are also available for standard tools.
Enhancing Virtual Machining
With the introduction of hyperMILL® 2023, the NC Optimizer feature in the hyperMILL® VIRTUAL Machining strategy now optimizes fixed rotary and parallel axes by automatically locating a kinematically correct and collision-free solution. This saves time by eliminating the need to manually interact with the axes.
Contact Details
Related Glossary Terms
- boring
boring
Enlarging a hole that already has been drilled or cored. Generally, it is an operation of truing the previously drilled hole with a single-point, lathe-type tool. Boring is essentially internal turning, in that usually a single-point cutting tool forms the internal shape. Some tools are available with two cutting edges to balance cutting forces.
- computer-aided manufacturing ( CAM)
computer-aided manufacturing ( CAM)
Use of computers to control machining and manufacturing processes.
- countersinking
countersinking
Cutting a beveled edge at the entrance of a hole so a screw head sits flush with the workpiece surface.
- gang cutting ( milling)
gang cutting ( milling)
Machining with several cutters mounted on a single arbor, generally for simultaneous cutting.
- milling
milling
Machining operation in which metal or other material is removed by applying power to a rotating cutter. In vertical milling, the cutting tool is mounted vertically on the spindle. In horizontal milling, the cutting tool is mounted horizontally, either directly on the spindle or on an arbor. Horizontal milling is further broken down into conventional milling, where the cutter rotates opposite the direction of feed, or “up” into the workpiece; and climb milling, where the cutter rotates in the direction of feed, or “down” into the workpiece. Milling operations include plane or surface milling, endmilling, facemilling, angle milling, form milling and profiling.
- numerical control ( NC)
numerical control ( NC)
Any controlled equipment that allows an operator to program its movement by entering a series of coded numbers and symbols. See CNC, computer numerical control; DNC, direct numerical control.
- parallel
parallel
Strip or block of precision-ground stock used to elevate a workpiece, while keeping it parallel to the worktable, to prevent cutter/table contact.
- turning
turning
Workpiece is held in a chuck, mounted on a face plate or secured between centers and rotated while a cutting tool, normally a single-point tool, is fed into it along its periphery or across its end or face. Takes the form of straight turning (cutting along the periphery of the workpiece); taper turning (creating a taper); step turning (turning different-size diameters on the same work); chamfering (beveling an edge or shoulder); facing (cutting on an end); turning threads (usually external but can be internal); roughing (high-volume metal removal); and finishing (final light cuts). Performed on lathes, turning centers, chucking machines, automatic screw machines and similar machines.