Contact Details
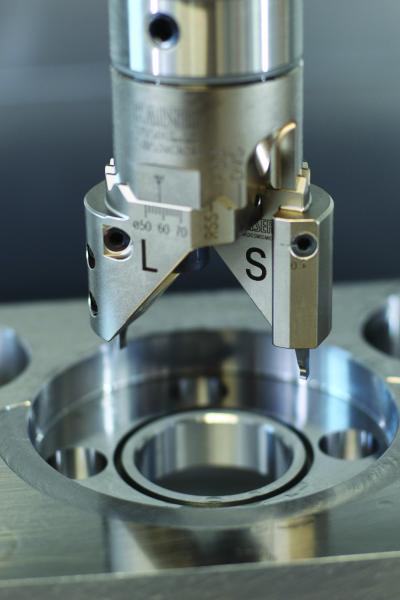
BIG KAISER announces the release of new insert holders for face grooving. The new accessories are specifically designed to fit the BIG KAISER large diameter series 318 and series 319 SW twin-cutter boring heads for ultimate system flexibility, according to the company.
The new face grooving system can be used as either a single or twin cutter grooving tool for diameter ranges from 2.087” to 118” in diameter. The design allows for a grooving depth up to 0.472”, with a minimum width of 0.079” and a maximum of 0.375”.
Face grooving with boring tools is generally more efficient than milling with circular interpolation, especially when manufacturing grooves of large diameters. Also, whenever a surface for a sealing application is required, there is no other acceptable or accurate option than to use a face grooving setup.
Using the boring tools as twin cutters, with a simultaneous adjustment in radius and length, allows the feed rate to be increased. Using the cutters in diameter offset operation enables a groove width of up to 0.472”, and both inside and outside diameters can be adjusted separately within the smallest tolerances. Both cutting edges can be adjusted easily to the same length, due to an eccentric bolt mechanism with clear direction indication.
“BIG KAISER products give our customers an unparalleled combination of quality, precision and ruggedness,” said Jack Burley, BIG KAISER vice president of sales and engineering. “These new face grooving holders uphold that tradition, while adding additional options to the applications possible with our SW twin cutter and large diameter series 318 system.”
Related Glossary Terms
- boring
boring
Enlarging a hole that already has been drilled or cored. Generally, it is an operation of truing the previously drilled hole with a single-point, lathe-type tool. Boring is essentially internal turning, in that usually a single-point cutting tool forms the internal shape. Some tools are available with two cutting edges to balance cutting forces.
- feed
feed
Rate of change of position of the tool as a whole, relative to the workpiece while cutting.
- gang cutting ( milling)
gang cutting ( milling)
Machining with several cutters mounted on a single arbor, generally for simultaneous cutting.
- grooving
grooving
Machining grooves and shallow channels. Example: grooving ball-bearing raceways. Typically performed by tools that are capable of light cuts at high feed rates. Imparts high-quality finish.
- interpolation
interpolation
Process of generating a sufficient number of positioning commands for the servomotors driving the machine tool so the path of the tool closely approximates the ideal path. See CNC, computer numerical control; NC, numerical control.
- milling
milling
Machining operation in which metal or other material is removed by applying power to a rotating cutter. In vertical milling, the cutting tool is mounted vertically on the spindle. In horizontal milling, the cutting tool is mounted horizontally, either directly on the spindle or on an arbor. Horizontal milling is further broken down into conventional milling, where the cutter rotates opposite the direction of feed, or “up” into the workpiece; and climb milling, where the cutter rotates in the direction of feed, or “down” into the workpiece. Milling operations include plane or surface milling, endmilling, facemilling, angle milling, form milling and profiling.