Contact Details
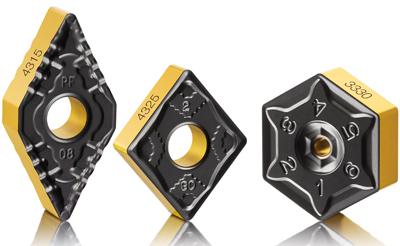
On March 3, Sandvik Coromant will introduce new insert grades for steel turning and cast iron milling with Inveio. In today's manufacturing, predictability is becoming increasingly important. Production that runs smoothly, without unexpected interruptions, allows for secure lights out production and high machine utilization; a cornerstone for profitable production processes.
Following the successful introduction of insert grade GC4325 in October 2013, Sandvik Coromant now extends that assortment and introduces new grades GC4315 and GC3330. All three grades feature Inveio which brings endurance, predictability and long tool life to the machining process.
The performance of these grades is made possible by Inveio's uni-directional crystal orientation. Normally, the crystal orientation of the CVD alumina coating is random. Sandvik Coromant found a way to control the growth of the crystals, lining them up in the same direction to create a stronger, uniform structure of the coating. These tightly-packed crystals create a strong barrier towards the cutting zone and chip.
The result is grades that offer incredible wear resistance and cutting edges that stay in shape and last longer in the cut. The long, predictable tool life of GC4325, GC4315 and GC3330 enables secure unmanned production with a high metal removal rate.
GC4325 is reportedly the first-choice grade for steel turning. When GC4325 reaches a limit in metal-removal rate due to high speed and long time in cut, GC4315 withstands the high cutting temperatures that occur. GC3330 is reportedly the first-choice grade for milling in cast iron materials.
Related Glossary Terms
- chemical vapor deposition ( CVD)
chemical vapor deposition ( CVD)
High-temperature (1,000° C or higher), atmosphere-controlled process in which a chemical reaction is induced for the purpose of depositing a coating 2µm to 12µm thick on a tool’s surface. See coated tools; PVD, physical vapor deposition.
- gang cutting ( milling)
gang cutting ( milling)
Machining with several cutters mounted on a single arbor, generally for simultaneous cutting.
- metal-removal rate
metal-removal rate
Rate at which metal is removed from an unfinished part, measured in cubic inches or cubic centimeters per minute.
- milling
milling
Machining operation in which metal or other material is removed by applying power to a rotating cutter. In vertical milling, the cutting tool is mounted vertically on the spindle. In horizontal milling, the cutting tool is mounted horizontally, either directly on the spindle or on an arbor. Horizontal milling is further broken down into conventional milling, where the cutter rotates opposite the direction of feed, or “up” into the workpiece; and climb milling, where the cutter rotates in the direction of feed, or “down” into the workpiece. Milling operations include plane or surface milling, endmilling, facemilling, angle milling, form milling and profiling.
- turning
turning
Workpiece is held in a chuck, mounted on a face plate or secured between centers and rotated while a cutting tool, normally a single-point tool, is fed into it along its periphery or across its end or face. Takes the form of straight turning (cutting along the periphery of the workpiece); taper turning (creating a taper); step turning (turning different-size diameters on the same work); chamfering (beveling an edge or shoulder); facing (cutting on an end); turning threads (usually external but can be internal); roughing (high-volume metal removal); and finishing (final light cuts). Performed on lathes, turning centers, chucking machines, automatic screw machines and similar machines.
- wear resistance
wear resistance
Ability of the tool to withstand stresses that cause it to wear during cutting; an attribute linked to alloy composition, base material, thermal conditions, type of tooling and operation and other variables.