Contact Details
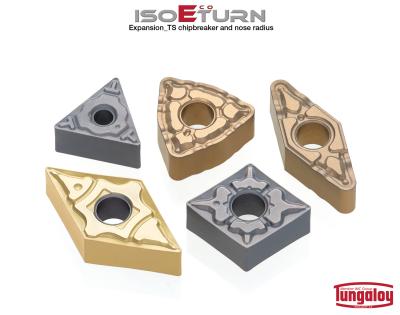
Tungaloy has expanded its ISO-EcoTurn cost efficient turning insert line by adding 63 inserts in new geometries.
ISO-EcoTurn inserts, while downsized for tool economy, incorporate the identical chipbreaker geometry and thickness of regular sized inserts to maintain the same cutting performance at a depth of cut up to 3.0 mm (0.12"). This expansion provides more cost efficient solutions in steel turning applications.
Major expansions have been made to existing NS9530 uncoated cermet insert, GT9530 and AT9530 coated cermet insert, and T9215 and T9225 CVD-coated carbide insert lines by increasing nose radii and chipbreaker style options.
TS style chipbreaker, which is a chipbreaker for finishing process proven for superior chip control at light cutting depths, is now available on cermet inserts, providing extended tool life and wear predictability for finish turning of steel parts.
Existing ZF and ZM style chipbreaker lines have also been expanded, increasing geometric options that provide better chip control in challenging finish profiling of intricate 3D surfaces. Along with new nose radii options, an expanded insert family of ISO-EcoTurn will further deliver cost efficient, high-performing turning solutions to customers.
Related Glossary Terms
- chipbreaker
chipbreaker
Groove or other tool geometry that breaks chips into small fragments as they come off the workpiece. Designed to prevent chips from becoming so long that they are difficult to control, catch in turning parts and cause safety problems.
- depth of cut
depth of cut
Distance between the bottom of the cut and the uncut surface of the workpiece, measured in a direction at right angles to the machined surface of the workpiece.
- profiling
profiling
Machining vertical edges of workpieces having irregular contours; normally performed with an endmill in a vertical spindle on a milling machine or with a profiler, following a pattern. See mill, milling machine.
- turning
turning
Workpiece is held in a chuck, mounted on a face plate or secured between centers and rotated while a cutting tool, normally a single-point tool, is fed into it along its periphery or across its end or face. Takes the form of straight turning (cutting along the periphery of the workpiece); taper turning (creating a taper); step turning (turning different-size diameters on the same work); chamfering (beveling an edge or shoulder); facing (cutting on an end); turning threads (usually external but can be internal); roughing (high-volume metal removal); and finishing (final light cuts). Performed on lathes, turning centers, chucking machines, automatic screw machines and similar machines.