Contact Details
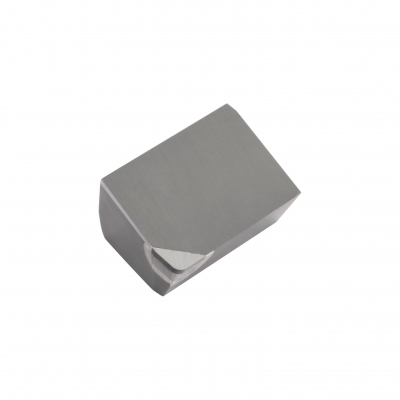
Anyone who’s replaced a head gasket on an internal combustion engine knows a smooth, flat surface on both cylinder head and block is needed for proper operation. No one understands this better than automakers, who strive for predictable, controlled surface finishes and high production output, together with maximum tool life and the lowest tooling cost per machined component.
Many machinists might think, “What’s the big deal? Aluminum is one of the easiest materials around.” And while that is certainly true of the ubiquitous 6061-T6, nothing could be further from the truth when it comes to the aluminum alloys used in automotive applications. Grades 319 and 390, for example, are readily cast into the complex shapes
needed for engine blocks, pistons, heads, pulleys, and similar parts, but due to their high silicon content—easily 20 to 30 times that of 6061—they’re like cutting sand. Fortunately for those charged with machining these abrasive metals, there’s a better alternative than carbide cutting tools, one that produces mirror finishes and produces tens
of thousands of parts per edge.
“Finishes of 2 to 3 μm Ra are easily obtainable, as is tool life between indexing of 40,000 engine blocks, cylinder heads and other automotive components,” says Tim Marshall, senior global product manager for indexable milling at Kennametal. “This new facemilling platform uses a fine-pitch aluminum body with wedge-style clamps and adjustable
pockets. A variety of polycrystalline diamond (PCD) inserts are available, from mini-tips for light finishing cuts to full face wipers, standard cartridge inserts, and 1/2 in. (12.7 mm) axial cutters for heavy roughing and shoulder cutting.”
He’s talking about the KBDM PCD facemilling system from Kennametal. Designed for high-volume machining, the KBDM is stocked in standard sizes of 2.5 - 8.0 in. (63 - 200 mm), although Marshall is quick to point out the company’s custom solution capabilities. “We can offer cutters up to 21.5 in. (550 mm) in diameter. This allows customers to machine very large components in a single pass. We also have options for integral shank bodies, HSK mounting, left hand cutter rotation, as well as special edge preps and nose radii.”
There’s more to the KBDM than a robust body design, however. Because automakers often create their own proprietary aluminum alloys, Kennametal has developed two PCD grades to complement it: KD1400 uses small diamond grains and offers excellent chipping resistance and good wear attributes, while KD1425 uses large diamond grains, giving it excellent abrasion resistance and thermal stability but only slightly lower performance where chipping is a concern. Both are capable of very high cutting parameters—depending on the alloy and setup rigidity, Kennametal recommends an initial cutting speed of 3,280 sfm (1000 m/min.) and feed rates of 0.004 in. per tooth (0.01 mm), although substantially higher values are possible.
“A major machine builder conducted cutting tests for us against several competitive solutions,” Marshall says. “Using a 24-tooth, 6.0 in. (150 mm) diameter face mill at 80 percent radial engagement and 0.04 in. axial DOC (1 mm), we ran at a feed rate of 0.006 ipt (0.15 mm) and 9,600 sfm (2926 m/min.). This comes out to 6,112 rpm, with a table feed of 880 ipm (22,350 mm). It was really moving. Even so, the KBDM produced a 14.7 Ra surface finish, several points better than the other cutting tools.”
Marshall recommends presetting the KBDM offline using an optical or video style presetter. A small amount of lubricant should be applied to the adjustment and locking screws, and also the wedge side of the pocket. Turn the axial adjustment screw until the insert is 0.0004 - 0.0006 in. (0.010 - 0.015 mm) below the final set height, tighten the
locking screws to 31 in/lb. (3.5 Nm)—don’t overtighten—then adjust each insert to its final height position. If using a wiper insert, set it 0.0006 - 0.0008 in. (0.015 - 0.020 mm) higher than the rest.
“It’s simple to set up,” Marshall says. “You can easily get everything within a couple microns. That's one of the keys to successful face milling, not only for proper balance at high spindle speeds but also for achieving the desired surface finish—when you're finishing a deck face on a block or head, both are critical.”
Adjusting the KBDM is a straightforward process—use an optical presetting device whenever possible, and don't overtighten.
Related Glossary Terms
- abrasive
abrasive
Substance used for grinding, honing, lapping, superfinishing and polishing. Examples include garnet, emery, corundum, silicon carbide, cubic boron nitride and diamond in various grit sizes.
- alloys
alloys
Substances having metallic properties and being composed of two or more chemical elements of which at least one is a metal.
- aluminum alloys
aluminum alloys
Aluminum containing specified quantities of alloying elements added to obtain the necessary mechanical and physical properties. Aluminum alloys are divided into two categories: wrought compositions and casting compositions. Some compositions may contain up to 10 alloying elements, but only one or two are the main alloying elements, such as copper, manganese, silicon, magnesium, zinc or tin.
- cutting speed
cutting speed
Tangential velocity on the surface of the tool or workpiece at the cutting interface. The formula for cutting speed (sfm) is tool diameter 5 0.26 5 spindle speed (rpm). The formula for feed per tooth (fpt) is table feed (ipm)/number of flutes/spindle speed (rpm). The formula for spindle speed (rpm) is cutting speed (sfm) 5 3.82/tool diameter. The formula for table feed (ipm) is feed per tooth (ftp) 5 number of tool flutes 5 spindle speed (rpm).
- facemilling
facemilling
Form of milling that produces a flat surface generally at right angles to the rotating axis of a cutter having teeth or inserts both on its periphery and on its end face.
- feed
feed
Rate of change of position of the tool as a whole, relative to the workpiece while cutting.
- flat ( screw flat)
flat ( screw flat)
Flat surface machined into the shank of a cutting tool for enhanced holding of the tool.
- gang cutting ( milling)
gang cutting ( milling)
Machining with several cutters mounted on a single arbor, generally for simultaneous cutting.
- inches per minute ( ipm)
inches per minute ( ipm)
Value that refers to how far the workpiece or cutter advances linearly in 1 minute, defined as: ipm = ipt 5 number of effective teeth 5 rpm. Also known as the table feed or machine feed.
- inches per tooth ( ipt)
inches per tooth ( ipt)
Linear distance traveled by the cutter during the engagement of one tooth. Although the milling cutter is a multi-edge tool, it is the capacity of each individual cutting edge that sets the limit of the tool, defined as: ipt = ipm/number of effective teeth 5 rpm or ipt = ipr/number of effective teeth. Sometimes referred to as the chip load.
- milling
milling
Machining operation in which metal or other material is removed by applying power to a rotating cutter. In vertical milling, the cutting tool is mounted vertically on the spindle. In horizontal milling, the cutting tool is mounted horizontally, either directly on the spindle or on an arbor. Horizontal milling is further broken down into conventional milling, where the cutter rotates opposite the direction of feed, or “up” into the workpiece; and climb milling, where the cutter rotates in the direction of feed, or “down” into the workpiece. Milling operations include plane or surface milling, endmilling, facemilling, angle milling, form milling and profiling.
- milling machine ( mill)
milling machine ( mill)
Runs endmills and arbor-mounted milling cutters. Features include a head with a spindle that drives the cutters; a column, knee and table that provide motion in the three Cartesian axes; and a base that supports the components and houses the cutting-fluid pump and reservoir. The work is mounted on the table and fed into the rotating cutter or endmill to accomplish the milling steps; vertical milling machines also feed endmills into the work by means of a spindle-mounted quill. Models range from small manual machines to big bed-type and duplex mills. All take one of three basic forms: vertical, horizontal or convertible horizontal/vertical. Vertical machines may be knee-type (the table is mounted on a knee that can be elevated) or bed-type (the table is securely supported and only moves horizontally). In general, horizontal machines are bigger and more powerful, while vertical machines are lighter but more versatile and easier to set up and operate.
- polycrystalline diamond ( PCD)
polycrystalline diamond ( PCD)
Cutting tool material consisting of natural or synthetic diamond crystals bonded together under high pressure at elevated temperatures. PCD is available as a tip brazed to a carbide insert carrier. Used for machining nonferrous alloys and nonmetallic materials at high cutting speeds.
- polycrystalline diamond ( PCD)2
polycrystalline diamond ( PCD)
Cutting tool material consisting of natural or synthetic diamond crystals bonded together under high pressure at elevated temperatures. PCD is available as a tip brazed to a carbide insert carrier. Used for machining nonferrous alloys and nonmetallic materials at high cutting speeds.
- shank
shank
Main body of a tool; the portion of a drill or similar end-held tool that fits into a collet, chuck or similar mounting device.
- wiper
wiper
Metal-removing edge on the face of a cutter that travels in a plane perpendicular to the axis. It is the edge that sweeps the machined surface. The flat should be as wide as the feed per revolution of the cutter. This allows any given insert to wipe the entire workpiece surface and impart a fine surface finish at a high feed rate.
Additional Products from Kennametal Inc.
Pagination
- First page
- Previous page
- 1
- 2
- 3
- 4
- 5
- 6
- 7
- 8
- 9