Contact Details
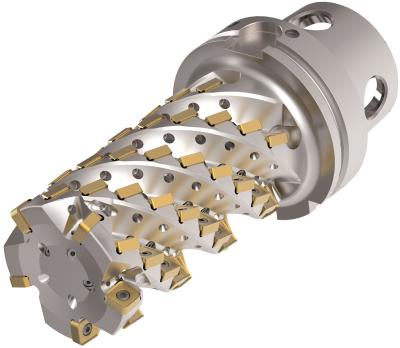
Customers have been asking for a new carbide grade to machine titanium 6Al4V at higher cutting speeds compared to increasing feed rates or increasing depth of cuts in that result in increased cutting forces imposed on the workpiece, fixtures and machine spindles. The KCSM40 grade has an advance cobalt binder that provides thermal fatigue resistance without sacrificing the toughness customers have experienced with KC725M or X500. In addition to the new material substrate, Kennametal’s proprietary AlTiN/TiN coating enhances the wear resistance at the cutting edge.
“We took the toughness of our most popular milling grades KC725M and X500 and increased the thermal crack resistance and wear resistance that will enable our customers to machine at higher cutting speeds without sacrificing toughness,” says Scott Etling, director of global product management for indexable milling at Kennametal.
The target cutting speed for KCSM40 in Ti6Al4V was 175 SFM (53 m/min) while achieving a greater than 20 cubic inches per minute (327 cm3/min) metal-removal rate for 60 minutes. Not only has KCSM40 achieved this but has results milling titanium at speeds up to 270 SFM (85 m/min) at a lower radial depth of cut.
Etling says the radial engagement of the milling cutter to the workpiece is one key component when optimizing the cutting speed. “At higher radial engagements, the insert is cutting the material for longer time which creates more heat at the cutting zone. The heat will not go into the titanium chips like when milling steels so controlling the heat is critical. Lower cutter speeds at higher radial engagements is a good practice. At lower radial engagements, higher cutting speeds can be achieved.”
Recent internal testing with the new HARVI Ultra helical milling platform achieved over 100 minutes of tool life running at 155 SFM (47 m/min) with a .0067 ipt (.12 mm/t) chip load. The radial depth of cut was 1.0” (25 mm) and the axial depth of cut was 3” (76 mm). Etling stated: “The edge condition on the KCSM40 grade still looked great. And we are getting many other fantastic results. In one facemilling operation on a hardened steel wear plate the number of passes was reduced from 234 to just 22. Needless to say, I am very excited for Kennametal and the value KCSM40 will bring to our customers”.
The development of KCSM40 was targeting Ti6Al4V but it will be a top performer in other high temperature/heat resistant materials. The KCSM40 is a grade that aligns well with Kennametal’s market segments like aerospace (aero structure and engine components), energy (turbine blades and parts made from duplex stainless steels) and ransportation (turbo chargers). Etling concluded, “We continue to get test results in daily on a wide array of workpiece materials and different components delivering some very nice cost savings for our customer.”
Related Glossary Terms
- cutting speed
cutting speed
Tangential velocity on the surface of the tool or workpiece at the cutting interface. The formula for cutting speed (sfm) is tool diameter 5 0.26 5 spindle speed (rpm). The formula for feed per tooth (fpt) is table feed (ipm)/number of flutes/spindle speed (rpm). The formula for spindle speed (rpm) is cutting speed (sfm) 5 3.82/tool diameter. The formula for table feed (ipm) is feed per tooth (ftp) 5 number of tool flutes 5 spindle speed (rpm).
- depth of cut
depth of cut
Distance between the bottom of the cut and the uncut surface of the workpiece, measured in a direction at right angles to the machined surface of the workpiece.
- facemilling
facemilling
Form of milling that produces a flat surface generally at right angles to the rotating axis of a cutter having teeth or inserts both on its periphery and on its end face.
- fatigue
fatigue
Phenomenon leading to fracture under repeated or fluctuating stresses having a maximum value less than the tensile strength of the material. Fatigue fractures are progressive, beginning as minute cracks that grow under the action of the fluctuating stress.
- fatigue resistance
fatigue resistance
Ability of a tool or component to be flexed repeatedly without cracking. Important for bandsaw-blade backing.
- feed
feed
Rate of change of position of the tool as a whole, relative to the workpiece while cutting.
- gang cutting ( milling)
gang cutting ( milling)
Machining with several cutters mounted on a single arbor, generally for simultaneous cutting.
- inches per minute ( ipm)
inches per minute ( ipm)
Value that refers to how far the workpiece or cutter advances linearly in 1 minute, defined as: ipm = ipt 5 number of effective teeth 5 rpm. Also known as the table feed or machine feed.
- inches per tooth ( ipt)
inches per tooth ( ipt)
Linear distance traveled by the cutter during the engagement of one tooth. Although the milling cutter is a multi-edge tool, it is the capacity of each individual cutting edge that sets the limit of the tool, defined as: ipt = ipm/number of effective teeth 5 rpm or ipt = ipr/number of effective teeth. Sometimes referred to as the chip load.
- metal-removal rate
metal-removal rate
Rate at which metal is removed from an unfinished part, measured in cubic inches or cubic centimeters per minute.
- milling
milling
Machining operation in which metal or other material is removed by applying power to a rotating cutter. In vertical milling, the cutting tool is mounted vertically on the spindle. In horizontal milling, the cutting tool is mounted horizontally, either directly on the spindle or on an arbor. Horizontal milling is further broken down into conventional milling, where the cutter rotates opposite the direction of feed, or “up” into the workpiece; and climb milling, where the cutter rotates in the direction of feed, or “down” into the workpiece. Milling operations include plane or surface milling, endmilling, facemilling, angle milling, form milling and profiling.
- milling cutter
milling cutter
Loosely, any milling tool. Horizontal cutters take the form of plain milling cutters, plain spiral-tooth cutters, helical cutters, side-milling cutters, staggered-tooth side-milling cutters, facemilling cutters, angular cutters, double-angle cutters, convex and concave form-milling cutters, straddle-sprocket cutters, spur-gear cutters, corner-rounding cutters and slitting saws. Vertical cutters use shank-mounted cutting tools, including endmills, T-slot cutters, Woodruff keyseat cutters and dovetail cutters; these may also be used on horizontal mills. See milling.
- wear resistance
wear resistance
Ability of the tool to withstand stresses that cause it to wear during cutting; an attribute linked to alloy composition, base material, thermal conditions, type of tooling and operation and other variables.