Contact Details
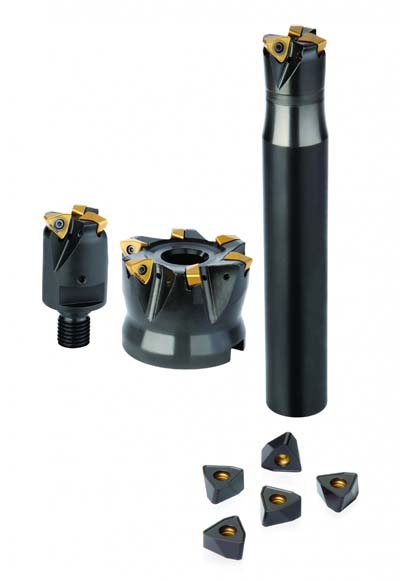
The new KenFeed 2X milling solution from Kennametal is the latest development in high-feed for light to heavy end milling operations. Developed from the original KenFeed platform, which has seen industry success for over six years, this new generation promises larger depths of cut using larger inserts.
While the previous generation of KenFeed tooling required three different insert sizes, the new KenFeed 2X requires only one. These new inserts are engineered to provide superior material removal rates and productivity at high feeds for roughing operations. Each double-sided trigon insert offers six cutting edges for better cost per edge position with full usage. The thick design of the inserts provides outstanding strength and reliability making them capable of withstanding high-feed operations. Additionally, it is the ideal solution for deep cavities or milling operations from 3 x D.
Two insert topographies can be easily selected to cover light, general purpose, and heavy machining. The HD insert geometry is the first choice for steels, high-strength steels, and cast iron, while the GD geometry provides lower cutting forces for softer materials. With the latest grades and geometries, the KenFeed 2X inserts provide 2 times the cutting power with multiple edges. K
enFeed 2X tool bodies are available in screw-on, end mill, and shell mill options with internal through coolant. The platform design makes KenFeed 2X ideal for pocketing, ramping, and helical interpolations with Z-plunge capabilities.
Kennametal plans to expand this new line to include additional metric and inch diameters.
Related Glossary Terms
- coolant
coolant
Fluid that reduces temperature buildup at the tool/workpiece interface during machining. Normally takes the form of a liquid such as soluble or chemical mixtures (semisynthetic, synthetic) but can be pressurized air or other gas. Because of water’s ability to absorb great quantities of heat, it is widely used as a coolant and vehicle for various cutting compounds, with the water-to-compound ratio varying with the machining task. See cutting fluid; semisynthetic cutting fluid; soluble-oil cutting fluid; synthetic cutting fluid.
- gang cutting ( milling)
gang cutting ( milling)
Machining with several cutters mounted on a single arbor, generally for simultaneous cutting.
- milling
milling
Machining operation in which metal or other material is removed by applying power to a rotating cutter. In vertical milling, the cutting tool is mounted vertically on the spindle. In horizontal milling, the cutting tool is mounted horizontally, either directly on the spindle or on an arbor. Horizontal milling is further broken down into conventional milling, where the cutter rotates opposite the direction of feed, or “up” into the workpiece; and climb milling, where the cutter rotates in the direction of feed, or “down” into the workpiece. Milling operations include plane or surface milling, endmilling, facemilling, angle milling, form milling and profiling.
- milling machine ( mill)
milling machine ( mill)
Runs endmills and arbor-mounted milling cutters. Features include a head with a spindle that drives the cutters; a column, knee and table that provide motion in the three Cartesian axes; and a base that supports the components and houses the cutting-fluid pump and reservoir. The work is mounted on the table and fed into the rotating cutter or endmill to accomplish the milling steps; vertical milling machines also feed endmills into the work by means of a spindle-mounted quill. Models range from small manual machines to big bed-type and duplex mills. All take one of three basic forms: vertical, horizontal or convertible horizontal/vertical. Vertical machines may be knee-type (the table is mounted on a knee that can be elevated) or bed-type (the table is securely supported and only moves horizontally). In general, horizontal machines are bigger and more powerful, while vertical machines are lighter but more versatile and easier to set up and operate.