Contact Details
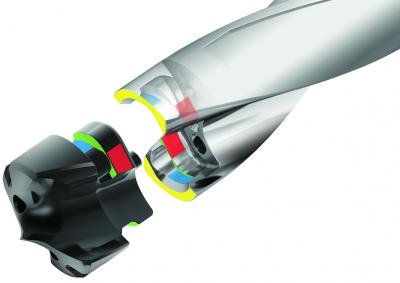
Some good ideas can be made even better. Much better. This was certainly the case when Kennametal engineers took the strength and versatility of their proven KSEM modular drill system and combined it with the ease of use and low feed forces of its smaller companion drill, KenTIP, the company reports. The resulting fusion of these advanced holemaking technologies is the KenTIP FS, a 6 mm to 26 mm, 1.5 to 12 x D modular drill that’s simple to use, produces good hole quality, and is tough enough to compete with solid-carbide drills across a wide range of materials.
Why KenTIP FS? Alexander Schmitt, senior global product manager for modular drilling at Kennametal, says FS denotes the tool’s “full solid” carbide tip. It just looks like the tip of a solid-carbide drill. That means the carbide tip fully covers and protects the steel holder from washing out, but he adds that the meaning goes a bit further. “The KenTIP FS not only looks like a solid-carbide drill; it also works like one. So you can think of it as a fusion of solid-carbide’s best characteristics together with the cost-effectiveness of indexable drilling tools.”
At first glance, the KenTIP FS appears to be like any other replaceable tip drill, with a disposable carbide insert, coolant through the tool, and a helical flute for efficient chip removal. The similarities end there, however. The KenTIP FS has a new design, one that incorporates a number of important features that separate it from the “me too” modular drilling crowd, according to the company.
For starters, the flutes are smooth and shiny. That’s because they’re highly polished after final machining, a process that Kennametal has found greatly improves chip evacuation and reduces wash out near the tip. And instead of the two coolant holes found in most modular drill designs, the KenTIP FS has four: two at the tip and two in the chip
gullet directly behind the head. This “multicoolant” approach provides greater coolant volume to prevent chip packing while simultaneously drawing heat away from the cutting zone, prolonging tool life and improving hole quality.
“Multicoolant allows us to tailor the cutting fluid needs to the application,” Schmitt explains. “For example, adhesion and flank wear are a big concern in stainless steels and cast irons. Inserts with HPL- and HPC-point styles have through-the-tool coolant channels to provide better lubrication in this area to overcome the issue. In steel though, it’s better to concentrate coolant to the rake and take the heat from the contact zone between chip and rake surface. So we eliminated the front coolant holes in our HPG geometry inserts to raise our insert tool life and improve chip breakage. In addition, this avoids built-up edge and makes the insert more rigid, which allows higher penetration rates in steel applications.”
There’s more to application tuning than the number of coolant holes an insert has. The HPG geometry is available in a new, highly wear resistant carbide grade, KCP15A, designed especially for steel. Its newly-designed point angle and self-piloting chisel edge offers better positioning accuracy and hole straightness than other drills in this class, even under high feed rates. The insert corners are protected with small chamfers to reduce chipping, and the margins are similarly reinforced, making the HPG geometry suitable for the cross holes and inclined exits encountered in hydraulics manifolds, for example, or the stacked plates used in heat exchanger production.
If the world drilled only steel, HPG geometry inserts might be sufficient, but the aerospace industry needs stainless steels and superalloys, while automotive manufacturers make extensive use of cast iron. For the former, Kennametal offers the HPL geometry, which has a split-point designed to reduce cutting forces and break up long-chipping aerospace and medical alloys. Like the HPG geometry, it too is available in a new grade, in this case KCMS15, a wear-resistant, fine-grain carbide with an anti-adhesive AlTiN coating that extends tool life. And for cast, ductile, and compacted graphite irons, the HPC geometry offers four margin lands and a radiused point that eliminates the exit chipping and cracking common with these materials, with a specially-designed chip gash that clears chips quickly in combination with the front coolant exits.
All three insert styles have 143-degree points, and specially prepared, polished or honed edges for
maximum tool life. “Between the HPG, HPC and HPL geometries, the KenTIP FS can handle most anything a solid-carbide drill can, but with far lower cost per part and equal or greater performance,” says Schmitt.
This is all cool stuff, but the KenTIP FS’ biggest differentiator isn’t its coolant delivery system, the new grades of carbide, its polished flutes or tip designs—it’s the mounting interface. KenTIP FS has the robust insert security of the larger KSEM and KSEM Plus drills, but uses a quick-release mechanism similar to the one KenTIP users are familiar with—just clean the pocket with an air blast, set the insert in place and give it a slight twist, then secure it with the supplied smart wrench. It’s not going anywhere. That’s because the KenTIP FS has a patented taper interface that provides maximum rigidity and accuracy. Its retention lock eliminates pullout, and its large bearing surface is able to withstand extreme torsional loads without pocket deformation. And since the full solid-carbide insert has no
mounting screw, there’s no risk of damage to the clamping mechanism from chip or workpiece contact.
Best of all, KenTIP FS is a sustainable solution. There’s no need for reconditioning as there is with solid-carbide and many modular drills. Use the insert to its fullest capability, replace it with a fresh tool, and get money back when you recycle the old one using the Kennametal recycling service. There’s none of the offset adjustments as there is with resharpened tools, or worry about how a used drill will perform compared to a new one. Tool life and production throughput are therefore more predictable, the company reports. And since the merry-go-round of drills out for grinding is now eliminated (never mind that inserts are much less expensive than solid-carbide drills), tooling costs are substantially reduced.
“The rigidity and stability of the KenTIP FS interface is crazy, and since the drill has a full solid-carbide front, the interface can withstand more heat and abuse than competing modular drill technologies. In addition to that the carbide tip fully covers and protects the steel holder from washing out. We simply put carbide where it matters," says Schmitt. “Granted, there will always be extremes where nothing but a solid-carbide drill will do, but for perhaps 90 percent of the applications we see, the new design works exceptionally well in a variety of materials. Kennametal
put a lot of time and effort into optimizing KenTIP FS, and we look forward to offering it to our customers.”
Related Glossary Terms
- alloys
alloys
Substances having metallic properties and being composed of two or more chemical elements of which at least one is a metal.
- built-up edge ( BUE)
built-up edge ( BUE)
1. Permanently damaging a metal by heating to cause either incipient melting or intergranular oxidation. 2. In grinding, getting the workpiece hot enough to cause discoloration or to change the microstructure by tempering or hardening.
- cast irons
cast irons
Cast ferrous alloys containing carbon in excess of solubility in austenite that exists in the alloy at the eutectic temperature. Cast irons include gray cast iron, white cast iron, malleable cast iron and ductile, or nodular, cast iron. The word “cast” is often left out.
- coolant
coolant
Fluid that reduces temperature buildup at the tool/workpiece interface during machining. Normally takes the form of a liquid such as soluble or chemical mixtures (semisynthetic, synthetic) but can be pressurized air or other gas. Because of water’s ability to absorb great quantities of heat, it is widely used as a coolant and vehicle for various cutting compounds, with the water-to-compound ratio varying with the machining task. See cutting fluid; semisynthetic cutting fluid; soluble-oil cutting fluid; synthetic cutting fluid.
- cutting fluid
cutting fluid
Liquid used to improve workpiece machinability, enhance tool life, flush out chips and machining debris, and cool the workpiece and tool. Three basic types are: straight oils; soluble oils, which emulsify in water; and synthetic fluids, which are water-based chemical solutions having no oil. See coolant; semisynthetic cutting fluid; soluble-oil cutting fluid; synthetic cutting fluid.
- feed
feed
Rate of change of position of the tool as a whole, relative to the workpiece while cutting.
- flank wear
flank wear
Reduction in clearance on the tool’s flank caused by contact with the workpiece. Ultimately causes tool failure.
- flutes
flutes
Grooves and spaces in the body of a tool that permit chip removal from, and cutting-fluid application to, the point of cut.
- grinding
grinding
Machining operation in which material is removed from the workpiece by a powered abrasive wheel, stone, belt, paste, sheet, compound, slurry, etc. Takes various forms: surface grinding (creates flat and/or squared surfaces); cylindrical grinding (for external cylindrical and tapered shapes, fillets, undercuts, etc.); centerless grinding; chamfering; thread and form grinding; tool and cutter grinding; offhand grinding; lapping and polishing (grinding with extremely fine grits to create ultrasmooth surfaces); honing; and disc grinding.
- point angle
point angle
Included angle at the point of a twist drill or similar tool; for general-purpose tools, the point angle is typically 118°.
- rake
rake
Angle of inclination between the face of the cutting tool and the workpiece. If the face of the tool lies in a plane through the axis of the workpiece, the tool is said to have a neutral, or zero, rake. If the inclination of the tool face makes the cutting edge more acute than when the rake angle is zero, the rake is positive. If the inclination of the tool face makes the cutting edge less acute or more blunt than when the rake angle is zero, the rake is negative.
- stainless steels
stainless steels
Stainless steels possess high strength, heat resistance, excellent workability and erosion resistance. Four general classes have been developed to cover a range of mechanical and physical properties for particular applications. The four classes are: the austenitic types of the chromium-nickel-manganese 200 series and the chromium-nickel 300 series; the martensitic types of the chromium, hardenable 400 series; the chromium, nonhardenable 400-series ferritic types; and the precipitation-hardening type of chromium-nickel alloys with additional elements that are hardenable by solution treating and aging.
- superalloys
superalloys
Tough, difficult-to-machine alloys; includes Hastelloy, Inconel and Monel. Many are nickel-base metals.
Additional Products from Kennametal Inc.
Pagination
- First page
- Previous page
- 1
- 2
- 3
- 4
- 5
- 6
- 7
- 8
- 9