Contact Details
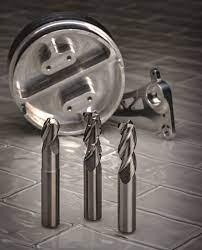
IMCO Carbide Tool Inc. has launched a new series – M213 STREAKERS – designed to handle extreme tool paths in aluminum alloys, provide superior surface finishes and meet the demands of today’s aerospace industry.
M213 STREAKERS feature three extremely large flute cavities, uniquely designed end face and gashing, and 37-degree helixes to achieve deep cuts and high feed rates. IMCO’s special end face and flute grinds combine to create a free cutting action allowing aggressive plunging and ramping moves.
“Milling in aluminum has unique challenges, especially for aerospace parts,” said Matt Osburn, Vice President, Technical Director for IMCO. “So we’ve focused our advanced technologies on making customers’ work easier and faster with end mills specially designed for milling deep slots, running steep ramp angles with high feed rates on entry moves, and plunging at high feed rates without a peck cycle, and providing a superior surface finish as part of the package.”
Like all IMCO high-performance end mills, M213 STREAKERS also feature improved corner strength for longer tool life. Micro-fine cutting edges slice cleanly through work material, and high-polish flute faces keep chips moving out of the cutting zone. M213 STREAKERS are available uncoated with square, corner radius and ball nose ends, as well as chip management system (CMS) and neck relief options.
IMCO’s online ToolBot is available 24/7 to generate fast, easy and customizable cutting parameters. Just answer the prompts and get your results, customized for your machining task and machine.
“As with all IMCO advanced technology, ToolBot helps give our customers the edge in a competitive industry to achieve higher productivity and profitability,” Osburn said. “That’s what we do best."
Related Glossary Terms
- alloys
alloys
Substances having metallic properties and being composed of two or more chemical elements of which at least one is a metal.
- aluminum alloys
aluminum alloys
Aluminum containing specified quantities of alloying elements added to obtain the necessary mechanical and physical properties. Aluminum alloys are divided into two categories: wrought compositions and casting compositions. Some compositions may contain up to 10 alloying elements, but only one or two are the main alloying elements, such as copper, manganese, silicon, magnesium, zinc or tin.
- feed
feed
Rate of change of position of the tool as a whole, relative to the workpiece while cutting.
- gang cutting ( milling)
gang cutting ( milling)
Machining with several cutters mounted on a single arbor, generally for simultaneous cutting.
- milling
milling
Machining operation in which metal or other material is removed by applying power to a rotating cutter. In vertical milling, the cutting tool is mounted vertically on the spindle. In horizontal milling, the cutting tool is mounted horizontally, either directly on the spindle or on an arbor. Horizontal milling is further broken down into conventional milling, where the cutter rotates opposite the direction of feed, or “up” into the workpiece; and climb milling, where the cutter rotates in the direction of feed, or “down” into the workpiece. Milling operations include plane or surface milling, endmilling, facemilling, angle milling, form milling and profiling.
- relief
relief
Space provided behind the cutting edges to prevent rubbing. Sometimes called primary relief. Secondary relief provides additional space behind primary relief. Relief on end teeth is axial relief; relief on side teeth is peripheral relief.