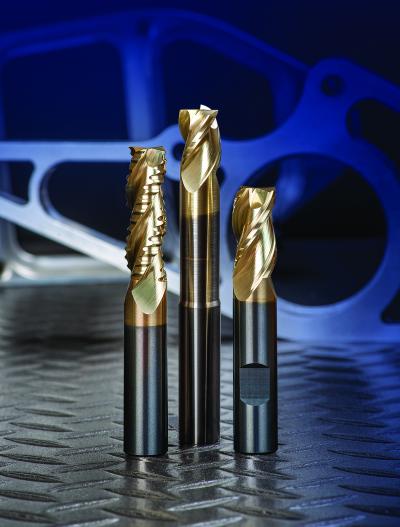
Machining productivity in aluminum alloys takes a major step forward with new STREAKERS M223 and M233 high-performance cutting tools, introduced by IMCO Carbide Tool.
“We designed these new STREAKERS specifically to make working in aluminum alloys more productive – faster cycle times, lower cost per part, higher metal removal rates even with heavy tool engagement, while getting better floor and wall finishes,” said Perry Osburn, president and CEO of IMCO Carbide Tool. “We reached those goals and then some.”
Developed for aggressive chip evacuation under extremely heavy chip loads, new M223 and M233 endmills combine unique flute designs, higher corner strength, high-performance ZrN coating and other features of IMCO’s advanced technologies. They’re ideal for high-performance milling in all types of aluminum, including high-silicon, die cast and extruded aluminum parts. Testing in IMCO’s in-house lab showed they perform well at speeds as low as 3,000 rpm and reach their peak performance at speeds above 10,000 rpm.
“So whether you’re roughing or finishing, you get better finishes without chip packing or maxing out horsepower,” Osburn said.
Contact Details
Related Glossary Terms
- alloys
alloys
Substances having metallic properties and being composed of two or more chemical elements of which at least one is a metal.
- aluminum alloys
aluminum alloys
Aluminum containing specified quantities of alloying elements added to obtain the necessary mechanical and physical properties. Aluminum alloys are divided into two categories: wrought compositions and casting compositions. Some compositions may contain up to 10 alloying elements, but only one or two are the main alloying elements, such as copper, manganese, silicon, magnesium, zinc or tin.
- gang cutting ( milling)
gang cutting ( milling)
Machining with several cutters mounted on a single arbor, generally for simultaneous cutting.
- milling
milling
Machining operation in which metal or other material is removed by applying power to a rotating cutter. In vertical milling, the cutting tool is mounted vertically on the spindle. In horizontal milling, the cutting tool is mounted horizontally, either directly on the spindle or on an arbor. Horizontal milling is further broken down into conventional milling, where the cutter rotates opposite the direction of feed, or “up” into the workpiece; and climb milling, where the cutter rotates in the direction of feed, or “down” into the workpiece. Milling operations include plane or surface milling, endmilling, facemilling, angle milling, form milling and profiling.