Contact Details
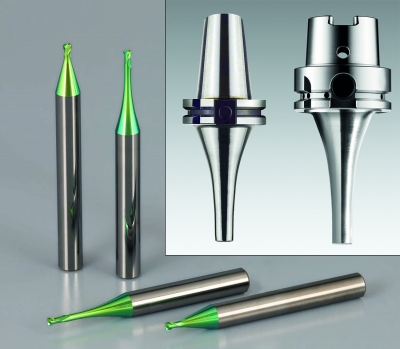
Emuge Corp. has announced the introduction of its new Micro End Mills and Micro Milling/Drilling Chucks for a wide range of applications such as die and mold, medical and more. The Micro End Mills feature a patented neck design with up to 10x diameter, enabling reach into deep contours. For optimal machining performance, a high radial bending strength withstands alternating stress on the cutting edge and relieved neck. The new Emuge end mills offer High Speed Cutting finishing of 2D and 3D contours, and are offered in square, ball nose, and torus end types. Featuring a short, stable cutting geometry, the end mills are available in Solid Carbide and CBN designs.
The Solid Carbide Micro End Mills are designed for high precision machining applications up to 55 HRC, and can machine small engravings, electrodes, components and cavities with varying depths. For heat and wear resistance, the end mills have a PVD applied thin film ALCR coating which results in long tool life. Ball Nose and Torus Solid Carbide End Mills provide high accuracy dimensional tolerances of ±5 µm. The solid carbide end mills are available with neck lengths of 2.2 x dia., 5 x dia. and 10 dia. and a cutting diameter of 0.2 to 2 mm.
Emuge CBN Micro End Mills offer increased tool life for high precision, accurate machining applications up to 66 HRC. The end mills produce highly polished surface finishes without the need for rework. The CBN Micro End Mills are available with neck lengths of 1.5 x dia., 3 x dia. and 4.5 x dia. and a range of cutting diameters from 0.3 to 2 mm.
New Emuge Micro Milling/ Drilling Chucks feature a slim design for hard to access areas, as well as high gripping torque and accuracy. The new Micro Chucks are part of the high precision/ performance Emuge FPC Mill/ Drill Chucks Line, providing unprecedented rigidity, vibration dampening, concentricity, machining speed, and tool life versus conventional chuck technologies for milling and drilling applications. Featuring the world's only chuck with a 1:16 worm gear, the Emuge FPC Chuck's patented design delivers three tons of traction force. The unique design and body provide 100% holding power for maximum rigidity, and the collet-cone assembly absorbs virtually all vibration for maximum dampening.
Emuge Micro Chucks are offered in a range of models in five shank styles (CAT, HSK, SK, BT and PSC) and hold 1- 6 mm or 1/8"-1/4" shank tools. Special coated collets provide high strength and lubricity. For ease of use, the chucks can be operated from behind with a supplied hex-key.
Related Glossary Terms
- chuck
chuck
Workholding device that affixes to a mill, lathe or drill-press spindle. It holds a tool or workpiece by one end, allowing it to be rotated. May also be fitted to the machine table to hold a workpiece. Two or more adjustable jaws actually hold the tool or part. May be actuated manually, pneumatically, hydraulically or electrically. See collet.
- cubic boron nitride ( CBN)
cubic boron nitride ( CBN)
Crystal manufactured from boron nitride under high pressure and temperature. Used to cut hard-to-machine ferrous and nickel-base materials up to 70 HRC. Second hardest material after diamond. See superabrasive tools.
- gang cutting ( milling)
gang cutting ( milling)
Machining with several cutters mounted on a single arbor, generally for simultaneous cutting.
- lubricity
lubricity
Measure of the relative efficiency with which a cutting fluid or lubricant reduces friction between surfaces.
- milling
milling
Machining operation in which metal or other material is removed by applying power to a rotating cutter. In vertical milling, the cutting tool is mounted vertically on the spindle. In horizontal milling, the cutting tool is mounted horizontally, either directly on the spindle or on an arbor. Horizontal milling is further broken down into conventional milling, where the cutter rotates opposite the direction of feed, or “up” into the workpiece; and climb milling, where the cutter rotates in the direction of feed, or “down” into the workpiece. Milling operations include plane or surface milling, endmilling, facemilling, angle milling, form milling and profiling.
- physical vapor deposition ( PVD)
physical vapor deposition ( PVD)
Tool-coating process performed at low temperature (500° C), compared to chemical vapor deposition (1,000° C). Employs electric field to generate necessary heat for depositing coating on a tool’s surface. See CVD, chemical vapor deposition.
- precision machining ( precision measurement)
precision machining ( precision measurement)
Machining and measuring to exacting standards. Four basic considerations are: dimensions, or geometrical characteristics such as lengths, angles and diameters of which the sizes are numerically specified; limits, or the maximum and minimum sizes permissible for a specified dimension; tolerances, or the total permissible variations in size; and allowances, or the prescribed differences in dimensions between mating parts.
- shank
shank
Main body of a tool; the portion of a drill or similar end-held tool that fits into a collet, chuck or similar mounting device.
- wear resistance
wear resistance
Ability of the tool to withstand stresses that cause it to wear during cutting; an attribute linked to alloy composition, base material, thermal conditions, type of tooling and operation and other variables.