Contact Details
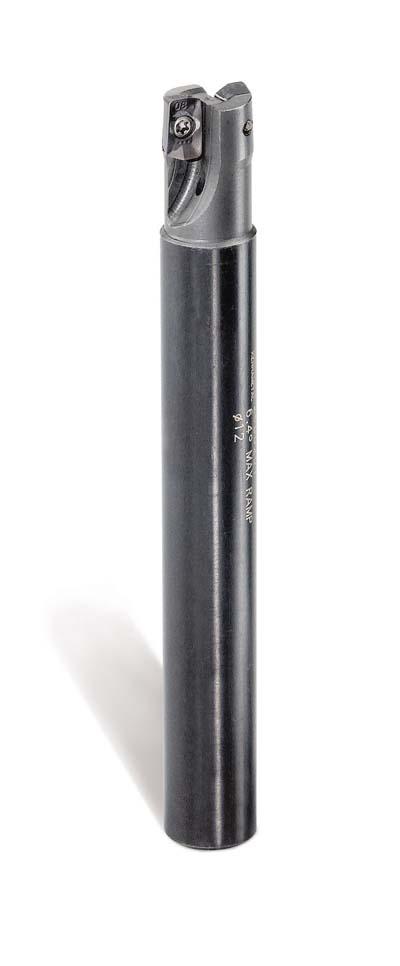
As the latest complement to the Mill 1 platform for finishing operations, Mill 1-7 is Kennametal's solution for finishing in small diameter milling. This new line is specifically engineered to cover ramping, slotting, and plunging for aerospace, energy, and general engineering applications. Mill 1-7 is a diverse tool for roughing and finishing operations, where small diameter end mills are required.
Multifunctional Mill 1-7 cutters can be used for shoulder-, ramp-, slot-, plunge-, and helical milling all while using a single insert to improve productivity, reduce inventory, and decrease machining costs. The small Mill 1-7 inserts enable the use of higher density cutters rather than larger inserts, providing greater feed and higher metal removal rates. The super positive rake of these inserts provides soft action and low cutting forces for smooth entry and exit from the component. This feature also enables the cutters to run at higher feed rates while using less power.
Mill 1-7 inserts are designed with elliptical cutting edges that are optimized with a straight 90° wall and true 0° lead, making them capable of replacing SCEM finish machining in certain applications.
Mill 1-7 inserts come in three grades to cover various applications and conditions:
The KC725M grade for general and heavy steel, stainless steel, and ductile cast iron milling applications is engineered for both wet and dry machining.
The multilayered TiN-TiCN-Al2O3-CVD-coated KCPK30 grade has advanced Beyond post-coat treatment for a wide application area in general and rough milling of steels and cast irons. This grade works best dry but functions under wet conditions.
The KC522M grade is engineered to provide better performance in general machining of high-temperature alloys and stainless steel. KC522M resists breakage and offers improved wear resistance and increased strength.
Related Glossary Terms
- alloys
alloys
Substances having metallic properties and being composed of two or more chemical elements of which at least one is a metal.
- cast irons
cast irons
Cast ferrous alloys containing carbon in excess of solubility in austenite that exists in the alloy at the eutectic temperature. Cast irons include gray cast iron, white cast iron, malleable cast iron and ductile, or nodular, cast iron. The word “cast” is often left out.
- feed
feed
Rate of change of position of the tool as a whole, relative to the workpiece while cutting.
- gang cutting ( milling)
gang cutting ( milling)
Machining with several cutters mounted on a single arbor, generally for simultaneous cutting.
- milling
milling
Machining operation in which metal or other material is removed by applying power to a rotating cutter. In vertical milling, the cutting tool is mounted vertically on the spindle. In horizontal milling, the cutting tool is mounted horizontally, either directly on the spindle or on an arbor. Horizontal milling is further broken down into conventional milling, where the cutter rotates opposite the direction of feed, or “up” into the workpiece; and climb milling, where the cutter rotates in the direction of feed, or “down” into the workpiece. Milling operations include plane or surface milling, endmilling, facemilling, angle milling, form milling and profiling.
- milling machine ( mill)
milling machine ( mill)
Runs endmills and arbor-mounted milling cutters. Features include a head with a spindle that drives the cutters; a column, knee and table that provide motion in the three Cartesian axes; and a base that supports the components and houses the cutting-fluid pump and reservoir. The work is mounted on the table and fed into the rotating cutter or endmill to accomplish the milling steps; vertical milling machines also feed endmills into the work by means of a spindle-mounted quill. Models range from small manual machines to big bed-type and duplex mills. All take one of three basic forms: vertical, horizontal or convertible horizontal/vertical. Vertical machines may be knee-type (the table is mounted on a knee that can be elevated) or bed-type (the table is securely supported and only moves horizontally). In general, horizontal machines are bigger and more powerful, while vertical machines are lighter but more versatile and easier to set up and operate.
- rake
rake
Angle of inclination between the face of the cutting tool and the workpiece. If the face of the tool lies in a plane through the axis of the workpiece, the tool is said to have a neutral, or zero, rake. If the inclination of the tool face makes the cutting edge more acute than when the rake angle is zero, the rake is positive. If the inclination of the tool face makes the cutting edge less acute or more blunt than when the rake angle is zero, the rake is negative.
- slotting
slotting
Machining, normally milling, that creates slots, grooves and similar recesses in workpieces, including T-slots and dovetails.
- wear resistance
wear resistance
Ability of the tool to withstand stresses that cause it to wear during cutting; an attribute linked to alloy composition, base material, thermal conditions, type of tooling and operation and other variables.
Additional Products from Kennametal Inc.
Pagination
- First page
- Previous page
- 1
- 2
- 3
- 4
- 5
- 6
- 7
- 8
- 9