Contact Details
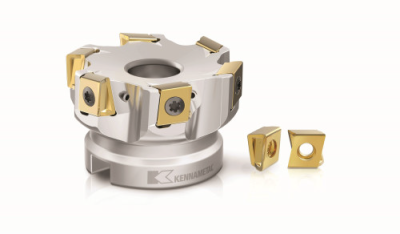
Kennametal announced its new Mill 4-12KT, the next generation of tangential shoulder mills, producing high quality floor surface finishes for nearly all steel and cast iron applications.
“The Mill 4-12KT uses15% lower cutting forces, an important consideration with today’s lighter-duty, 40-taper machine tools,” said Tim Marshall, senior global product manager. “That allows customers to feed faster without putting additional stress on the spindle. And in long overhang situations or where the part fixturing is less than optimal, lower forces equate to less chatter, reduced edge chipping, and smoother surface finishes.”
Mill 4-12KT has tangentially mounted inserts with four cutting edges per insert for reduced tooling costs. Seven corner radii from 0.016" (0.4 mm) to 0.122" (3.1 mm) are available, along with coolant-through, medium and coarse-pitch cutter bodies 2" (50mm) to 8" (200mm) in diameter. With an axial DOC range from 0.019" to 0.472" (0.5 to 12mm), Mill 4-12KT covers most shoulder milling applications.
Multiple factors contribute to significant performance increases, even in aggressive cutting conditions. The tangential, “on-edge” insert design also allows the insert to take advantage of the strength of the carbide thickness more so than radially mounted inserts found on traditional milling cutters. A shallow pocket design, allows the core size of the cutter body to be robust.
The axial and radial seating surface designs provide exceptional stability. The Mill 4-12KT is the perfect complement to Kennametal’s existing shoulder milling portfolio. This includes the Mill 4-11 and Mill 4-15, cutters known for their ability to generate shoulders with high-quality wall surface finishes.
Related Glossary Terms
- chatter
chatter
Condition of vibration involving the machine, workpiece and cutting tool. Once this condition arises, it is often self-sustaining until the problem is corrected. Chatter can be identified when lines or grooves appear at regular intervals in the workpiece. These lines or grooves are caused by the teeth of the cutter as they vibrate in and out of the workpiece and their spacing depends on the frequency of vibration.
- feed
feed
Rate of change of position of the tool as a whole, relative to the workpiece while cutting.
- gang cutting ( milling)
gang cutting ( milling)
Machining with several cutters mounted on a single arbor, generally for simultaneous cutting.
- milling
milling
Machining operation in which metal or other material is removed by applying power to a rotating cutter. In vertical milling, the cutting tool is mounted vertically on the spindle. In horizontal milling, the cutting tool is mounted horizontally, either directly on the spindle or on an arbor. Horizontal milling is further broken down into conventional milling, where the cutter rotates opposite the direction of feed, or “up” into the workpiece; and climb milling, where the cutter rotates in the direction of feed, or “down” into the workpiece. Milling operations include plane or surface milling, endmilling, facemilling, angle milling, form milling and profiling.
- milling machine ( mill)
milling machine ( mill)
Runs endmills and arbor-mounted milling cutters. Features include a head with a spindle that drives the cutters; a column, knee and table that provide motion in the three Cartesian axes; and a base that supports the components and houses the cutting-fluid pump and reservoir. The work is mounted on the table and fed into the rotating cutter or endmill to accomplish the milling steps; vertical milling machines also feed endmills into the work by means of a spindle-mounted quill. Models range from small manual machines to big bed-type and duplex mills. All take one of three basic forms: vertical, horizontal or convertible horizontal/vertical. Vertical machines may be knee-type (the table is mounted on a knee that can be elevated) or bed-type (the table is securely supported and only moves horizontally). In general, horizontal machines are bigger and more powerful, while vertical machines are lighter but more versatile and easier to set up and operate.