Contact Details
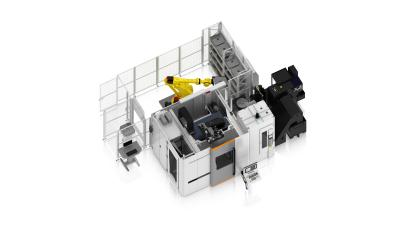
To grow as production needs increase, the design features of the new MILL P 800 U S full 5-axis milling machine from GF Machining Solutions provide for easy, seamless automation integration. As a flexible and scalable solution, shops can start with a simple standalone MILL P 800 U S, then expand their production capabilities into fully automated multiple-machine cells.
GF Machining Solutions constructed the MILL P 800 U S as a more compact machine with a reduced footprint and engineered it specifically for automation. The company relocated the electrical cabinet from the back of the machine to its lefthand side, thus allowing for direct robot loading from the rear of the machine.
Prior to the design change, a robot would load parts on to one of the pallets of the machine’s two-pallet changer. Now, there is no pallet changer, and the robot arm itself moves into the machine with a pallet of loaded workpieces.
In terms of operator ergonomics and accessibility, having the automation in the back frees up the front of the machine for the operator and makes for a safer work environment. Typically, automated loading happens at either the front or at one of a machine’s sides. That type of layout requires more floorspace and that the machines either face the automation with no access to their fronts or are turned 90 degrees. Automating from the back also helps reduce the entire footprint of a cell.
For increased stability and precision, GF Machining Solutions engineered the MILL P 800 U S as a unique full twin-ballscrew drive/twin-linear scale gantry machine. The twin drives compensate for any imbalanced cutting forces between the two drive torque motors on each gantry side, while the twin linear scales ensure both gantry axis ends are always synchronized. The design also lowers stress on the machine to help reduce ballscrew and guide wear for longer life and less maintenance.
The MILL P 800 U S features a torque-motor driven rotary/tilt trunnion-style table that contributes to the machine’s continuous full 5-axis simultaneous movement for smooth part surface contouring. The high-performance, high dynamic torque motor drives eliminate backlash (pitch and reverse errors), friction, wear and heat generation. This equates to increased rigidity, longer lasting accuracy and less maintenance, unlike worm or G-driven type tables that often require significant amounts of maintenance because of their inherent mechanical play.
Optimized for both roughing and finishing, the StepTec spindle on the MILL P 800U S features a maximum speed of 20,000 rpm, an HSK-A63 interface, torque rating of 120Nm and power output of 36Kw. This balance of speed and torque makes the spindle especially well suited for a wide range of applications.
In addition to 120 and 170 tool storage capacities and 15-pallet storge unit, GF Machining Solutions offers several other performance-enhancing options for the MILL P 800U S. These include the company’s Operator Support System OSS module, Machine Spindle Protection (MSP) system, Automatic Machine Calibration (AMC) feature and EconoWatt function.
The OSS module enables selection of machine settings for adapted, optimal machining. In doing so, the module takes into account such machining priorities and parameters as time, precision, surface quality and worktable load.
To protect machine spindles, MSP prevents serious spindle damage in the event of a crash. The magnet-based collision system uses self-contained mechanical protection units composed of magnets within the spindle housing. These magnets separate and enable the spindle to essentially spring back to its normal position after a collision. The machine is immediately back in production and without the need for any geometry adjustments.
Sensors on the magnets register movement and automatically trigger the machine to abort its current operations. As a result of what appears as instantaneous detection, spindles experience 90 percent less force during crashes.
As a new option, the GF Machining Solutions AMC automatically runs a program cycle to check and recalibrate a machine’s kinematics. This feature is particularly critical for when ambient temperatures fluctuate in a manufacturing facility and when performing full 5-axis machining because those operations involve multiple, simultaneous complex machine movements that require consistent accuracy.
For increased sustainability, the EconoWatt function available for the MILL P 800U S saves energy, allowing operators to program a standby or sleeping mode. In standby, the machine will automatically initiate a warmup cycle prior to the operator arriving to run a job, while the sleeping mode shuts down unnecessary pumps and motors when the machine is not actually cutting.
Related Glossary Terms
- backlash
backlash
Reaction in dynamic motion systems where potential energy that was created while the object was in motion is released when the object stops. Release of this potential energy or inertia causes the device to quickly snap backward relative to the last direction of motion. Backlash can cause a system’s final resting position to be different from what was intended and from where the control system intended to stop the device.
- calibration
calibration
Checking measuring instruments and devices against a master set to ensure that, over time, they have remained dimensionally stable and nominally accurate.
- gang cutting ( milling)
gang cutting ( milling)
Machining with several cutters mounted on a single arbor, generally for simultaneous cutting.
- milling
milling
Machining operation in which metal or other material is removed by applying power to a rotating cutter. In vertical milling, the cutting tool is mounted vertically on the spindle. In horizontal milling, the cutting tool is mounted horizontally, either directly on the spindle or on an arbor. Horizontal milling is further broken down into conventional milling, where the cutter rotates opposite the direction of feed, or “up” into the workpiece; and climb milling, where the cutter rotates in the direction of feed, or “down” into the workpiece. Milling operations include plane or surface milling, endmilling, facemilling, angle milling, form milling and profiling.
- milling machine ( mill)
milling machine ( mill)
Runs endmills and arbor-mounted milling cutters. Features include a head with a spindle that drives the cutters; a column, knee and table that provide motion in the three Cartesian axes; and a base that supports the components and houses the cutting-fluid pump and reservoir. The work is mounted on the table and fed into the rotating cutter or endmill to accomplish the milling steps; vertical milling machines also feed endmills into the work by means of a spindle-mounted quill. Models range from small manual machines to big bed-type and duplex mills. All take one of three basic forms: vertical, horizontal or convertible horizontal/vertical. Vertical machines may be knee-type (the table is mounted on a knee that can be elevated) or bed-type (the table is securely supported and only moves horizontally). In general, horizontal machines are bigger and more powerful, while vertical machines are lighter but more versatile and easier to set up and operate.
- milling machine ( mill)2
milling machine ( mill)
Runs endmills and arbor-mounted milling cutters. Features include a head with a spindle that drives the cutters; a column, knee and table that provide motion in the three Cartesian axes; and a base that supports the components and houses the cutting-fluid pump and reservoir. The work is mounted on the table and fed into the rotating cutter or endmill to accomplish the milling steps; vertical milling machines also feed endmills into the work by means of a spindle-mounted quill. Models range from small manual machines to big bed-type and duplex mills. All take one of three basic forms: vertical, horizontal or convertible horizontal/vertical. Vertical machines may be knee-type (the table is mounted on a knee that can be elevated) or bed-type (the table is securely supported and only moves horizontally). In general, horizontal machines are bigger and more powerful, while vertical machines are lighter but more versatile and easier to set up and operate.