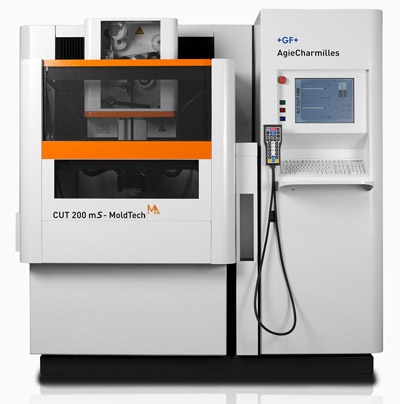
GF Machining Solutions has introduced the AgieCharmilles CUT 200/300 MoldTech series of wire EDMs that meets the specific needs of moldmakers. The machines are equipped with a special bundle of dedicated technical features and capabilities for accurate and efficient machining of highly complex parts with variable surface heights or taper cuts. Such challenging components include those for plastic injection molds, aluminum extrusion dies and for the aerospace and medical industries.
At the heart of the MoldTech package is the TAPER-EXPERT smart module for cutting highly precise large taper angles with perfect surface finishes. TAPER-EXPERT allows the use of large radius wire guides and soft brass wire, and it compensates in real time for the pivoting point drift in the Z direction when the angle changes. The results are surface finishes of 0.2µm Ra and better angle cuts up to 30 degrees.
With the dedicated onboard AgieCharmilles AC CUT HMI (human-machine interface), the MoldTech machines reduce setup time and improve productivity. The interface is easy to use and provides TAPER-EXPERT ADVANCE, a new taper adjustment function that lets operators fine-tune the CNC parameters and control taper accuracy. Also through the AC CUT HMI, a powerful onboard CAM system called AC OPTICAM 3D seamlessly imports 3D CAD files, including Parasolid and IGES. Users can then bring solid model files into the control, quickly extract all ruled shapes and automatically generate the ISO code for each profile.
Other features in the MoldTech package include a smart threading system called the MULTIJET, a wire-breakage prevention module called POWER-EXPERT and a smart system called SURFACE-EXPERT. The MULTIJET system uses nozzles that can automatically thread start holes as small as 1.5mm in diameter, even while the machine is in a position to cut tapers of up to 30 degrees.
The POWER-EXPERT smart module continuously calculates part thickness, checks injection pressure and adjusts machine power accordingly to prevent wire breakage and improve accuracy and cutting speed. SURFACE-EXPERT constantly tweaks sparking parameters when cutting parts with abrupt variations in height, which also helps prevent wire breakage.
The specialized MoldTech package is available on four of GF Machining Solutions' high-speed wire EDM models built for machining larger, complex workpieces. For such applications, the machines deliver excellent surface integrity and boost productivity, while helping to control production costs. The series includes the CUT 200 mS, CUT 200 Sp, CUT 300 mS, and the CUT 300 Sp.
Contact Details
Related Glossary Terms
- computer numerical control ( CNC)
computer numerical control ( CNC)
Microprocessor-based controller dedicated to a machine tool that permits the creation or modification of parts. Programmed numerical control activates the machine’s servos and spindle drives and controls the various machining operations. See DNC, direct numerical control; NC, numerical control.
- computer-aided design ( CAD)
computer-aided design ( CAD)
Product-design functions performed with the help of computers and special software.
- computer-aided manufacturing ( CAM)
computer-aided manufacturing ( CAM)
Use of computers to control machining and manufacturing processes.
- cutting speed
cutting speed
Tangential velocity on the surface of the tool or workpiece at the cutting interface. The formula for cutting speed (sfm) is tool diameter 5 0.26 5 spindle speed (rpm). The formula for feed per tooth (fpt) is table feed (ipm)/number of flutes/spindle speed (rpm). The formula for spindle speed (rpm) is cutting speed (sfm) 5 3.82/tool diameter. The formula for table feed (ipm) is feed per tooth (ftp) 5 number of tool flutes 5 spindle speed (rpm).
- electrical-discharge machining ( EDM)
electrical-discharge machining ( EDM)
Process that vaporizes conductive materials by controlled application of pulsed electrical current that flows between a workpiece and electrode (tool) in a dielectric fluid. Permits machining shapes to tight accuracies without the internal stresses conventional machining often generates. Useful in diemaking.
- extrusion
extrusion
Conversion of an ingot or billet into lengths of uniform cross section by forcing metal to flow plastically through a die orifice.
- solid model
solid model
3-D model created using “building blocks.” This is the most accurate way of representing real-world objects in CAD.
- threading
threading
Process of both external (e.g., thread milling) and internal (e.g., tapping, thread milling) cutting, turning and rolling of threads into particular material. Standardized specifications are available to determine the desired results of the threading process. Numerous thread-series designations are written for specific applications. Threading often is performed on a lathe. Specifications such as thread height are critical in determining the strength of the threads. The material used is taken into consideration in determining the expected results of any particular application for that threaded piece. In external threading, a calculated depth is required as well as a particular angle to the cut. To perform internal threading, the exact diameter to bore the hole is critical before threading. The threads are distinguished from one another by the amount of tolerance and/or allowance that is specified. See turning.
- wire EDM
wire EDM
Process similar to ram electrical-discharge machining except a small-diameter copper or brass wire is used as a traveling electrode. Usually used in conjunction with a CNC and only works when a part is to be cut completely through. A common analogy is wire electrical-discharge machining is like an ultraprecise, electrical, contour-sawing operation.