Contact Details
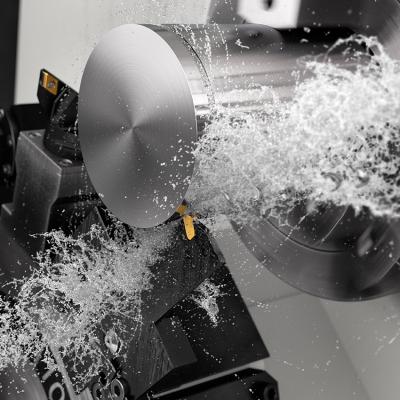
Sandvik Coromant has unveiled a new blade for its CoroCut QD parting-off system, which in combination with new process methodology, substantially improves the tool’s stability by realigning the resultant cutting force. Among numerous benefits available to the customer are improved productivity, enhanced surface quality, and reduced noise levels.
With conventional parting-off tool configurations on turning centers and multi-task machines, the capability of feed motion in the XZ plane is an inherent limitation. When performing parting operations, the resultant vector of cutting forces is inevitably directed sharply across the tool’s cross-section, leading to high loads and potential deformation.
To remedy the situation, Sandvik Coromant engineers have developed a solution that takes advantage of capability in modern turning centers and multitask machines to feed the tool in the Y direction. In the new concept, the top face of the insert is placed parallel to the end of the blade, rotating the insert seat 90° counterclockwise. The new blade cuts its way into the workpiece with its front end, which roughly aligns the resultant vector of cutting forces with the longitudinal axis of the blade. FEM analysis confirms that this eliminates the critical stresses typical to conventional blades and increases blade stiffness by six times compared with standard designs. With enhanced stiffness, customers can increase feed rates or use a longer overhang without losing stability.
When deployed on turning centers, the biggest benefits of Y-axis parting are improved productivity and process security. For multitask machine users, Y-axis parting blades offer increased accessibility and capability for larger diameters. In fact, a pre-test confirmed a 50% increase in overhang when parting-off a conventional 120 mm diameter bar at the maximum feed capacity of the insert, thus helping to maximize the full potential of the machine. Furthermore, a 300% productivity increase was achieved without any compromise to process security.
In a customer test case, Y-axis parting successfully replaced band sawing for a 180 mm diameter Inconel bar, resulting in significant productivity improvement thanks to dramatically shorter machining times.
Another advantage of Y-axis parting is that it requires minimal changes to typical production setups. The same program can be used for all components, while practically no extra tool costs are incurred as existing CoroCut QD tooling can be utilized. There is also high potential to make real time savings when the workpiece is clamped at both ends since no other operations are possible during parting-off.
The new CoroCut QD blades come in widths of 3 and 4 mm. Standard length versions (in both 3 and 4 mm widths) are offered for parting up to 120 mm diameter, as well as an extra-long 4 mm wide blade for parting up to 180 mm diameter. Conventional CoroCut QD blade adapters and inserts can be used with the new blades.
Related Glossary Terms
- bandsaw blade ( band)
bandsaw blade ( band)
Endless band, normally with serrated teeth, that serves as the cutting tool for cutoff or contour band machines.
- centers
centers
Cone-shaped pins that support a workpiece by one or two ends during machining. The centers fit into holes drilled in the workpiece ends. Centers that turn with the workpiece are called “live” centers; those that do not are called “dead” centers.
- cutting force
cutting force
Engagement of a tool’s cutting edge with a workpiece generates a cutting force. Such a cutting force combines tangential, feed and radial forces, which can be measured by a dynamometer. Of the three cutting force components, tangential force is the greatest. Tangential force generates torque and accounts for more than 95 percent of the machining power. See dynamometer.
- feed
feed
Rate of change of position of the tool as a whole, relative to the workpiece while cutting.
- parallel
parallel
Strip or block of precision-ground stock used to elevate a workpiece, while keeping it parallel to the worktable, to prevent cutter/table contact.
- parting
parting
When used in lathe or screw-machine operations, this process separates a completed part from chuck-held or collet-fed stock by means of a very narrow, flat-end cutting, or parting, tool.
- sawing
sawing
Machining operation in which a powered machine, usually equipped with a blade having milled or ground teeth, is used to part material (cutoff) or give it a new shape (contour bandsawing, band machining). Four basic types of sawing operations are: hacksawing (power or manual operation in which the blade moves back and forth through the work, cutting on one of the strokes); cold or circular sawing (a rotating, circular, toothed blade parts the material much as a workshop table saw or radial-arm saw cuts wood); bandsawing (a flexible, toothed blade rides on wheels under tension and is guided through the work); and abrasive sawing (abrasive points attached to a fiber or metal backing part stock, could be considered a grinding operation).
- stiffness
stiffness
1. Ability of a material or part to resist elastic deflection. 2. The rate of stress with respect to strain; the greater the stress required to produce a given strain, the stiffer the material is said to be. See dynamic stiffness; static stiffness.
- turning
turning
Workpiece is held in a chuck, mounted on a face plate or secured between centers and rotated while a cutting tool, normally a single-point tool, is fed into it along its periphery or across its end or face. Takes the form of straight turning (cutting along the periphery of the workpiece); taper turning (creating a taper); step turning (turning different-size diameters on the same work); chamfering (beveling an edge or shoulder); facing (cutting on an end); turning threads (usually external but can be internal); roughing (high-volume metal removal); and finishing (final light cuts). Performed on lathes, turning centers, chucking machines, automatic screw machines and similar machines.