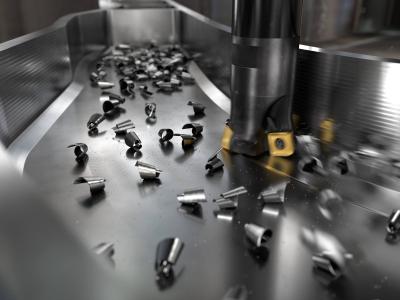
A high-feed milling cutter for diameters 13–25 mm and 0.500–1.000 inches has been introduced by Sandvik Coromant. Among the advantages of using the new CoroMill 415 are enhanced security, thanks to iLock insert seat interface technology, and high metal-removal rates as a result of high cutter density and high feed capacity.
CoroMill 415 covers the application area between Sandvik Coromant's current round tools product offer and existing high-feed products, such as CoroMill 210 and CoroMill 419.
A major feature is the cutter’s iLock insert seat interface, which has been designed to deliver high stability and reduce the potential for scrap workpieces. In addition, the insert seat itself ensures that the small inserts are easier to handle.
The extra stability during cutting is one of the factors that makes CoroMill 415 a suitable option for machine shops seeking productive solutions. For example, the tool is capable of delivering elevated metal-removal rates, an outcome that is supported further by the cutter’s high-density and high-feed capacity. In turn, high metal-removal rates help increase productivity, and this is supplemented by the extra-close H pitch, which can be deployed thanks to the tool’s inherent high stability, ensuring more than one tooth is always engaged in the cut.
A further benefit for manufacturers is that, although the inserts are small, each offers four cutting edges to help reduce cost per component and boost competitive advantage.
For those looking to lower their tooling inventory and minimize machine downtime, CoroMill 415 is also available with the Coromant EH (Exchangeable Head) interface. With Coromant EH, manufacturers can access a wide assortment of solid-carbide cutting heads, indexable milling cutters, boring heads, integrated machine adapters and shanks to reduce their inventory of tools.
This added versatility is backed by the suitability of CoroMill 415 for all ISO materials and many different component machining applications.
Contact Details
Related Glossary Terms
- boring
boring
Enlarging a hole that already has been drilled or cored. Generally, it is an operation of truing the previously drilled hole with a single-point, lathe-type tool. Boring is essentially internal turning, in that usually a single-point cutting tool forms the internal shape. Some tools are available with two cutting edges to balance cutting forces.
- feed
feed
Rate of change of position of the tool as a whole, relative to the workpiece while cutting.
- gang cutting ( milling)
gang cutting ( milling)
Machining with several cutters mounted on a single arbor, generally for simultaneous cutting.
- milling
milling
Machining operation in which metal or other material is removed by applying power to a rotating cutter. In vertical milling, the cutting tool is mounted vertically on the spindle. In horizontal milling, the cutting tool is mounted horizontally, either directly on the spindle or on an arbor. Horizontal milling is further broken down into conventional milling, where the cutter rotates opposite the direction of feed, or “up” into the workpiece; and climb milling, where the cutter rotates in the direction of feed, or “down” into the workpiece. Milling operations include plane or surface milling, endmilling, facemilling, angle milling, form milling and profiling.
- milling cutter
milling cutter
Loosely, any milling tool. Horizontal cutters take the form of plain milling cutters, plain spiral-tooth cutters, helical cutters, side-milling cutters, staggered-tooth side-milling cutters, facemilling cutters, angular cutters, double-angle cutters, convex and concave form-milling cutters, straddle-sprocket cutters, spur-gear cutters, corner-rounding cutters and slitting saws. Vertical cutters use shank-mounted cutting tools, including endmills, T-slot cutters, Woodruff keyseat cutters and dovetail cutters; these may also be used on horizontal mills. See milling.
- pitch
pitch
1. On a saw blade, the number of teeth per inch. 2. In threading, the number of threads per inch.