Contact Details
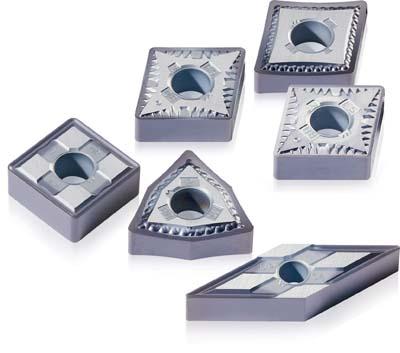
Because of their high performance strength and relatively light weight, high-temperature alloys are growing in applications across many manufacturing industries, notably aerospace and defense, automotive, heavy equipment, and energy.
Higher-temperature-strength materials, however, also mean high cutting forces when machining. Titanium, for example, also exhibits high work hardening and a large strain rate, which also raises temperatures and the energy required to remove the chip. In most applications, the answer means slower speeds and feeds, since a carbide cutting tool's strength decreases as temperatures increase.
New Beyond grades from Kennametal are delivering higher productivity for turning tough alloys, both in higher speeds and feeds (faster turnaround time) and longer tool life (more parts per tool). KCU10 is specifically engineered for increased performance in OD and ID turning, grooving, plunging, undercutting, and threading. KCU25 covers threading, grooving, cutoff, and selected additional turning applications. Both take advantage of new PVD (physical vapor deposition) coating technology, including special surface treatments that improve machining performance in high-temperature materials.
In many cases, speeds, feeds, or depth-of-cut can be increased, while related wear issues like depth-of-cut notching are reduced. KCU10 additionally features a dual-layer coating application, a top layer of AlSiTiN atop a second layer of AlTiN. The boundary between the two serves to help deflect micro-cracks.
Related Glossary Terms
- alloys
alloys
Substances having metallic properties and being composed of two or more chemical elements of which at least one is a metal.
- cutoff
cutoff
Step that prepares a slug, blank or other workpiece for machining or other processing by separating it from the original stock. Performed on lathes, chucking machines, automatic screw machines and other turning machines. Also performed on milling machines, machining centers with slitting saws and sawing machines with cold (circular) saws, hacksaws, bandsaws or abrasive cutoff saws. See saw, sawing machine; turning.
- grooving
grooving
Machining grooves and shallow channels. Example: grooving ball-bearing raceways. Typically performed by tools that are capable of light cuts at high feed rates. Imparts high-quality finish.
- hardening
hardening
Process of increasing the surface hardness of a part. It is accomplished by heating a piece of steel to a temperature within or above its critical range and then cooling (or quenching) it rapidly. In any heat-treatment operation, the rate of heating is important. Heat flows from the exterior to the interior of steel at a definite rate. If the steel is heated too quickly, the outside becomes hotter than the inside and the desired uniform structure cannot be obtained. If a piece is irregular in shape, a slow heating rate is essential to prevent warping and cracking. The heavier the section, the longer the heating time must be to achieve uniform results. Even after the correct temperature has been reached, the piece should be held at the temperature for a sufficient period of time to permit its thickest section to attain a uniform temperature. See workhardening.
- inner diameter ( ID)
inner diameter ( ID)
Dimension that defines the inside diameter of a cavity or hole. See OD, outer diameter.
- outer diameter ( OD)
outer diameter ( OD)
Dimension that defines the exterior diameter of a cylindrical or round part. See ID, inner diameter.
- physical vapor deposition ( PVD)
physical vapor deposition ( PVD)
Tool-coating process performed at low temperature (500° C), compared to chemical vapor deposition (1,000° C). Employs electric field to generate necessary heat for depositing coating on a tool’s surface. See CVD, chemical vapor deposition.
- threading
threading
Process of both external (e.g., thread milling) and internal (e.g., tapping, thread milling) cutting, turning and rolling of threads into particular material. Standardized specifications are available to determine the desired results of the threading process. Numerous thread-series designations are written for specific applications. Threading often is performed on a lathe. Specifications such as thread height are critical in determining the strength of the threads. The material used is taken into consideration in determining the expected results of any particular application for that threaded piece. In external threading, a calculated depth is required as well as a particular angle to the cut. To perform internal threading, the exact diameter to bore the hole is critical before threading. The threads are distinguished from one another by the amount of tolerance and/or allowance that is specified. See turning.
- turning
turning
Workpiece is held in a chuck, mounted on a face plate or secured between centers and rotated while a cutting tool, normally a single-point tool, is fed into it along its periphery or across its end or face. Takes the form of straight turning (cutting along the periphery of the workpiece); taper turning (creating a taper); step turning (turning different-size diameters on the same work); chamfering (beveling an edge or shoulder); facing (cutting on an end); turning threads (usually external but can be internal); roughing (high-volume metal removal); and finishing (final light cuts). Performed on lathes, turning centers, chucking machines, automatic screw machines and similar machines.
Additional Products from Kennametal Inc.
Pagination
- First page
- Previous page
- 1
- 2
- 3
- 4
- 5
- 6
- 7
- 8
- 9