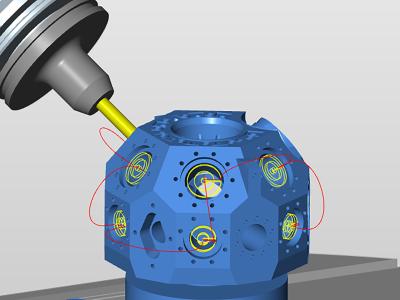
The Optimizer, an optional module in the hyperMILL VIRTUAL Machining simulation solution from Open Mind, enables users to improve NC programs based on the kinematics of the individual machine. The machining process is simulated by using a digital twin. This enables the users to overcome the complexity associated with alternative setup and orientation options in 5-axis machining.
The hyperMILL VIRTUAL Machining Optimizer automatically finds the best solution for collision-free orientation with efficient traverse movements for multi-axis machining. This allows programmers to avoid errors when manually optimizing axis positions. Given the high degree of complexity, it is difficult to determine the effects on all subsequent machining steps and make decisions about the best overall solution. The hyperMILL VIRTUAL Machining Optimizer analyzes complete machining sequences with powerful optimization algorithms while considering axis limitations. Time-consuming repositioning is avoided. The Optimizer ensures efficient and safe machining operations.
Another major advantage of the Optimizer comes into play when programming on a wide variety of machining centers. CAM programs can be created completely independently of machine properties because the simulation software automatically adjusts to the machine in use and it performs comprehensive collision checks. This gives companies greater flexibility when it comes to assigning machining capacity.
The Optimizer can also detect other possible problems. For example, if a machine has a limited axis rotation, the software takes this into account when selecting tool positions and ensures smooth machining. If there is an axis limitation, the Optimizer interrupts the toolpath, gently retracts and rewinds the axis to avoid the limitation. The tool then gently approaches again and machining continues. This method enables spiral machining in a limited machine. Fork head machines can also be used with the Optimizer to enable dynamic machining.
The software optimizes infeed movements and automatically determines whether positioning is faster with the aid of a rotational axis. The rotation axes are moved along the shortest path, and the movements of the linear axes are minimized. This allows greater speeds to be achieved during the movements. If a 3-axis movement is not possible due to detected collisions or axis limitations, the hyperMILL VIRTUAL Machining Optimizer changes the movement with the aid of a fourth or fifth axis. The various operations, whether 2.5D, 3D or 5-axis, are linked in such a way that auxiliary processing times are shortened. The tool travels close to the workpiece while being checked for collisions and it is not retracted to a clearance plane between movements, drastically reducing cycle times.
Contact Details
Related Glossary Terms
- centers
centers
Cone-shaped pins that support a workpiece by one or two ends during machining. The centers fit into holes drilled in the workpiece ends. Centers that turn with the workpiece are called “live” centers; those that do not are called “dead” centers.
- clearance
clearance
Space provided behind a tool’s land or relief to prevent rubbing and subsequent premature deterioration of the tool. See land; relief.
- computer-aided manufacturing ( CAM)
computer-aided manufacturing ( CAM)
Use of computers to control machining and manufacturing processes.
- numerical control ( NC)
numerical control ( NC)
Any controlled equipment that allows an operator to program its movement by entering a series of coded numbers and symbols. See CNC, computer numerical control; DNC, direct numerical control.
- toolpath( cutter path)
toolpath( cutter path)
2-D or 3-D path generated by program code or a CAM system and followed by tool when machining a part.