Contact Details
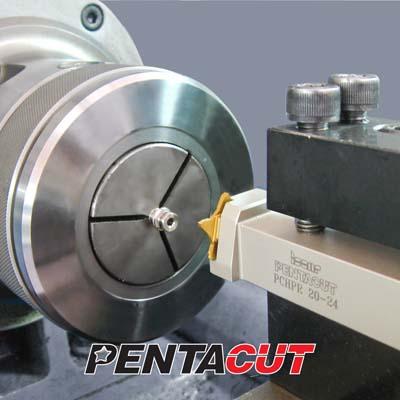
June 2011 — ISCAR's new perpendicular toolholder makes it easier to fit PENTACUT 24 grooving and parting tools into overcrowded turrets in high-volume turning operations. It holds the same popular PENTACUT five-edged grooving and parting tool, but from a different angle.
The PCHPRL square-shank toolholder clamps the PENTACUT insert perpendicular to its axis, so the shank can line up with the spindle's centerline. This creates more tool presentation options and can eliminate interference issues in some setups. Popular and proven for years, the star-shaped PENTACUT parting insert provides five straight indexable cutting edges with several types of chipformers.
The combination of a very secure clamping system and strong insert design enables grooving, parting, recessing and chamfering. Users report straighter sidewalls and flatter groove bottoms. Due to the star-shaped design, the insert survives despite failure on one edge. The other four edges remain intact and useable, leading to much lower tooling labor and inventory costs.
Three toolholder sizes are available in the perpendicular arrangement: 16, 20 and 24mm cross sections. The new tools are suitable for regular turret machines, perpendicular orientation and gang/turret type CNC lathe machines.
Related Glossary Terms
- chamfering
chamfering
Machining a bevel on a workpiece or tool; improves a tool’s entrance into the cut.
- computer numerical control ( CNC)
computer numerical control ( CNC)
Microprocessor-based controller dedicated to a machine tool that permits the creation or modification of parts. Programmed numerical control activates the machine’s servos and spindle drives and controls the various machining operations. See DNC, direct numerical control; NC, numerical control.
- grooving
grooving
Machining grooves and shallow channels. Example: grooving ball-bearing raceways. Typically performed by tools that are capable of light cuts at high feed rates. Imparts high-quality finish.
- lathe
lathe
Turning machine capable of sawing, milling, grinding, gear-cutting, drilling, reaming, boring, threading, facing, chamfering, grooving, knurling, spinning, parting, necking, taper-cutting, and cam- and eccentric-cutting, as well as step- and straight-turning. Comes in a variety of forms, ranging from manual to semiautomatic to fully automatic, with major types being engine lathes, turning and contouring lathes, turret lathes and numerical-control lathes. The engine lathe consists of a headstock and spindle, tailstock, bed, carriage (complete with apron) and cross slides. Features include gear- (speed) and feed-selector levers, toolpost, compound rest, lead screw and reversing lead screw, threading dial and rapid-traverse lever. Special lathe types include through-the-spindle, camshaft and crankshaft, brake drum and rotor, spinning and gun-barrel machines. Toolroom and bench lathes are used for precision work; the former for tool-and-die work and similar tasks, the latter for small workpieces (instruments, watches), normally without a power feed. Models are typically designated according to their “swing,” or the largest-diameter workpiece that can be rotated; bed length, or the distance between centers; and horsepower generated. See turning machine.
- parting
parting
When used in lathe or screw-machine operations, this process separates a completed part from chuck-held or collet-fed stock by means of a very narrow, flat-end cutting, or parting, tool.
- recessing
recessing
A turning operation in which a groove is produced on the periphery or inside a hole of a workpiece. The grooving tool moves at right angles to the axis of rotation.
- shank
shank
Main body of a tool; the portion of a drill or similar end-held tool that fits into a collet, chuck or similar mounting device.
- toolholder
toolholder
Secures a cutting tool during a machining operation. Basic types include block, cartridge, chuck, collet, fixed, modular, quick-change and rotating.
- turning
turning
Workpiece is held in a chuck, mounted on a face plate or secured between centers and rotated while a cutting tool, normally a single-point tool, is fed into it along its periphery or across its end or face. Takes the form of straight turning (cutting along the periphery of the workpiece); taper turning (creating a taper); step turning (turning different-size diameters on the same work); chamfering (beveling an edge or shoulder); facing (cutting on an end); turning threads (usually external but can be internal); roughing (high-volume metal removal); and finishing (final light cuts). Performed on lathes, turning centers, chucking machines, automatic screw machines and similar machines.