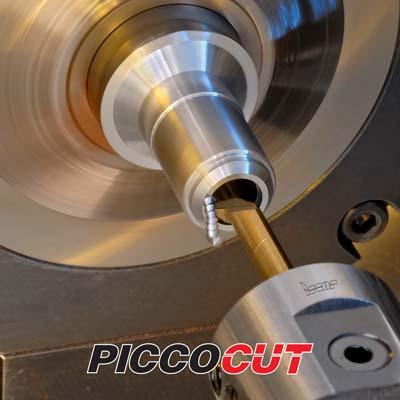
ISCAR continues to create fresh solutions for difficult ID machining problems through strategic additions to its popular PICCO family of solid carbide inserts. The company's latest innovations attack three specific trouble spots in ID machining: bottoming of blind holes, reaching deeper into high-aspect bores and reducing mismatch between matching tool diameters and bore sizes. The better the match between tool and hole geometry, the more efficiently the operation will run. Ideally, both diameters and lengths should be matched.
To improve bottom flatness in blind holes, the new PICCO 050.20 insert features a higher 20°Frontal clearance angle, up from 8 degrees. The added clearance creates more room to eliminate chip jamming and minimize re-cutting of chips. The inserts are available in 4.0 and 5.0mm shank diameters for bore diameters of 2.0mm and up. For high-aspect bores with at least 6.8mm diameter, a new style PICCO 060 chamfering insert now comes with a long-reach 40mm shank, providing more than twice the reach-in as the existing 19mm shank.
A new 6mm insert has also been added to the line, enabling better size matches in the 5 to 6.8mm diameter line. Three additional bore diameters also widen the tool selections available in the PICCO 050 family, which covers the bore diameter range of 0.5 to 4.0mm. New diameters are 0.8, 2.5 and 3.5mm. All PICCO 050 internal turning and chamfering inserts come in several shank lengths, to optimize the size match between tool and hole.
All ISCAR PICCO tools come in left- and right-hand styles and are available in grade IC900, the most versatile PVD coated carbide grade. The thin PVD coating protects the cutting edge while preserving the optimal cutting geometry built into the substrate.
Contact Details
Related Glossary Terms
- chamfering
chamfering
Machining a bevel on a workpiece or tool; improves a tool’s entrance into the cut.
- clearance
clearance
Space provided behind a tool’s land or relief to prevent rubbing and subsequent premature deterioration of the tool. See land; relief.
- inner diameter ( ID)
inner diameter ( ID)
Dimension that defines the inside diameter of a cavity or hole. See OD, outer diameter.
- physical vapor deposition ( PVD)
physical vapor deposition ( PVD)
Tool-coating process performed at low temperature (500° C), compared to chemical vapor deposition (1,000° C). Employs electric field to generate necessary heat for depositing coating on a tool’s surface. See CVD, chemical vapor deposition.
- shank
shank
Main body of a tool; the portion of a drill or similar end-held tool that fits into a collet, chuck or similar mounting device.
- turning
turning
Workpiece is held in a chuck, mounted on a face plate or secured between centers and rotated while a cutting tool, normally a single-point tool, is fed into it along its periphery or across its end or face. Takes the form of straight turning (cutting along the periphery of the workpiece); taper turning (creating a taper); step turning (turning different-size diameters on the same work); chamfering (beveling an edge or shoulder); facing (cutting on an end); turning threads (usually external but can be internal); roughing (high-volume metal removal); and finishing (final light cuts). Performed on lathes, turning centers, chucking machines, automatic screw machines and similar machines.