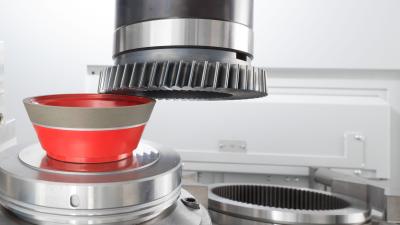
A fully integrated on-board cutter resharpening unit is now available for Gleason vertical Power Skiving machines, allowing for the completely automated resharpening of cutters used in the production of both soft and hardened gears up to 600 mm in workpiece diameter.
By automating cutter resharpening operations, Gleason Power Skiving machines require minimum operator involvement, greatly reducing the time typically required for frequent tool changes and subsequent first-part inspection cycles. Additionally, the usual cost for external tool refurbishment can be avoided.
As compared to the typical cutter resharpening process, the new on-board unit is remarkably fast and simple. The machine’s axes position the cutter to the grinding wheel. The integrated cutter resharpening unit then executes the necessary grinding strokes while the cutter performs the infeed and the indexing from tooth to tooth, all performed automatically and based on the cutter geometry that exists after a certain number of gears have been cut. After the initial corrections are made based on the first gear cut, a consistent gear quality is more easily maintained throughout the complete tool life. The frequency of the resharpening cycles can be chosen depending on the gear quality required.
Tool cost-per-piece is also considerably lower as compared to external reconditioning with no tool changes, first-part-inspections and machine adjustments during a cutter’s lifetime, as well as no handling and logistics costs for reconditioning cycles. With a lot less cutters in circulation, tool investment is significantly reduced.
Contact Details
Related Glossary Terms
- grinding
grinding
Machining operation in which material is removed from the workpiece by a powered abrasive wheel, stone, belt, paste, sheet, compound, slurry, etc. Takes various forms: surface grinding (creates flat and/or squared surfaces); cylindrical grinding (for external cylindrical and tapered shapes, fillets, undercuts, etc.); centerless grinding; chamfering; thread and form grinding; tool and cutter grinding; offhand grinding; lapping and polishing (grinding with extremely fine grits to create ultrasmooth surfaces); honing; and disc grinding.
- grinding wheel
grinding wheel
Wheel formed from abrasive material mixed in a suitable matrix. Takes a variety of shapes but falls into two basic categories: one that cuts on its periphery, as in reciprocating grinding, and one that cuts on its side or face, as in tool and cutter grinding.