Contact Details
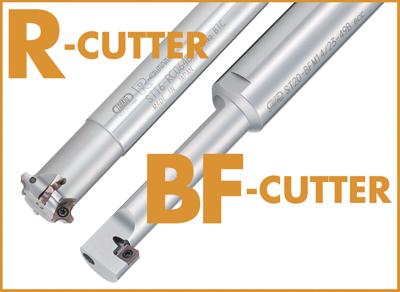
BIG Kaiser Precision Tooling Inc. introduces the R-Cutter (Pat. P) and BF-Cutter from BIG Daishowa. The R-Cutter is an ultra high feed front and back radius chamfering mill which features high rake angles that reduce cutting resistance and minimize burr generation. The radius chamfering mill is offered as a single-insert design and a four-insert design for higher feed rates.
The coated carbide insert design allows for four indexes, is available with radii of 0.02" to 0.16", and is optimized for all steels (including stainless), cast iron and aluminum. A variety of R-Cutter types are available, including a single insert front chamfering-only design with shank diameters of 16mm and 20mm, and front-and-back combination chamfering models with cutting shank diameters of 10mm, 16mm and 32mm. Each model featuring a single insert design allows for cutting in the tightest of spaces.
The BF-Cutter was exclusively designed for back spot facing of cap bolt holes, sizes M6-M16. It features the a small square indexable insert (with 4 indexes), and is for all steels (including stainless), cast iron and aluminum. The coolant-through capability helps cool down the back side cutting area, increasing tool life. The BF-Cutter is available for minimum facing diameters beginning at 0.433" and up to 1.024". A unique, offset design allows for easy programming; simply offset the centers between the machine spindle and the hole when entering or exiting the hole with the cutter. The minimum hole diameter for possible entry is 0.256".
"Whether front or back radius chamfering, or back spot facing bolt holes, these new cutters from BIG Daishowa with very unique features are great additions to any shop's tool arsenal in that they optimize productivity for any applicable operation they are called up for," says Jack Burley, vice president, sales and engineering, BIG Kaiser. "Both tools are available from BIG Kaiser's new Indexable Cutting Tools Catalog, which details BIG Daishowa's entire line of high performance indexable cutting tool systems."
Related Glossary Terms
- burr
burr
Stringy portions of material formed on workpiece edges during machining. Often sharp. Can be removed with hand files, abrasive wheels or belts, wire wheels, abrasive-fiber brushes, waterjet equipment or other methods.
- centers
centers
Cone-shaped pins that support a workpiece by one or two ends during machining. The centers fit into holes drilled in the workpiece ends. Centers that turn with the workpiece are called “live” centers; those that do not are called “dead” centers.
- chamfering
chamfering
Machining a bevel on a workpiece or tool; improves a tool’s entrance into the cut.
- feed
feed
Rate of change of position of the tool as a whole, relative to the workpiece while cutting.
- indexable insert
indexable insert
Replaceable tool that clamps into a tool body, drill, mill or other cutter body designed to accommodate inserts. Most inserts are made of cemented carbide. Often they are coated with a hard material. Other insert materials are ceramic, cermet, polycrystalline cubic boron nitride and polycrystalline diamond. The insert is used until dull, then indexed, or turned, to expose a fresh cutting edge. When the entire insert is dull, it is usually discarded. Some inserts can be resharpened.
- milling machine ( mill)
milling machine ( mill)
Runs endmills and arbor-mounted milling cutters. Features include a head with a spindle that drives the cutters; a column, knee and table that provide motion in the three Cartesian axes; and a base that supports the components and houses the cutting-fluid pump and reservoir. The work is mounted on the table and fed into the rotating cutter or endmill to accomplish the milling steps; vertical milling machines also feed endmills into the work by means of a spindle-mounted quill. Models range from small manual machines to big bed-type and duplex mills. All take one of three basic forms: vertical, horizontal or convertible horizontal/vertical. Vertical machines may be knee-type (the table is mounted on a knee that can be elevated) or bed-type (the table is securely supported and only moves horizontally). In general, horizontal machines are bigger and more powerful, while vertical machines are lighter but more versatile and easier to set up and operate.
- rake
rake
Angle of inclination between the face of the cutting tool and the workpiece. If the face of the tool lies in a plane through the axis of the workpiece, the tool is said to have a neutral, or zero, rake. If the inclination of the tool face makes the cutting edge more acute than when the rake angle is zero, the rake is positive. If the inclination of the tool face makes the cutting edge less acute or more blunt than when the rake angle is zero, the rake is negative.
- shank
shank
Main body of a tool; the portion of a drill or similar end-held tool that fits into a collet, chuck or similar mounting device.