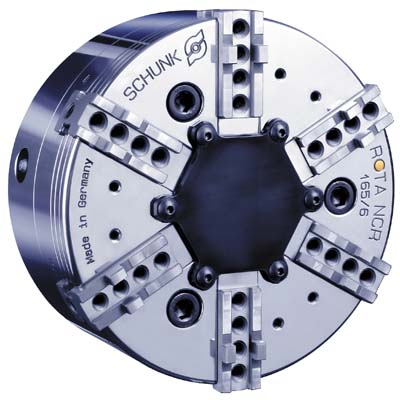
The clamping of thin-walled and easily deformed components is challenging. With its ROTA NCR 6-jaw compensation chuck, Schunk Inc. offers a standard solution for this type of workpiece. The company has now standardized the sizes of the ROTA NCR with diameters of up to 1,200mm and, in doing so, opened up the possibilities for precision workpiece clamping with large lathe chucks. The ROTA NCR consists of a central chuck piston, which has three inner pendulums positioned at 120 degrees. Each pendulum works in conjunction with three pairs of base jaws, resulting in six-point contact. With clamping force points being aligned towards the chuck center of rotation, even premachined parts can be centered without deformation of the workpiece. The ROTA NCR is available in sizes 165mm, 200mm, 250mm, 315mm, 400mm, 500mm, 630mm, 800mm, 1,000mm and 1,200mm diameters. The ROTA NCR chuck offering can also be utilized on virtually any turning application. For example, the challenge of contamination issues caused by the machining of materials like gray cast iron can be minimized by the utilization of Schunk's vertical turning product, also available in sizes up to 1,200mm diameters.
Contact Details
Related Glossary Terms
- chuck
chuck
Workholding device that affixes to a mill, lathe or drill-press spindle. It holds a tool or workpiece by one end, allowing it to be rotated. May also be fitted to the machine table to hold a workpiece. Two or more adjustable jaws actually hold the tool or part. May be actuated manually, pneumatically, hydraulically or electrically. See collet.
- lathe
lathe
Turning machine capable of sawing, milling, grinding, gear-cutting, drilling, reaming, boring, threading, facing, chamfering, grooving, knurling, spinning, parting, necking, taper-cutting, and cam- and eccentric-cutting, as well as step- and straight-turning. Comes in a variety of forms, ranging from manual to semiautomatic to fully automatic, with major types being engine lathes, turning and contouring lathes, turret lathes and numerical-control lathes. The engine lathe consists of a headstock and spindle, tailstock, bed, carriage (complete with apron) and cross slides. Features include gear- (speed) and feed-selector levers, toolpost, compound rest, lead screw and reversing lead screw, threading dial and rapid-traverse lever. Special lathe types include through-the-spindle, camshaft and crankshaft, brake drum and rotor, spinning and gun-barrel machines. Toolroom and bench lathes are used for precision work; the former for tool-and-die work and similar tasks, the latter for small workpieces (instruments, watches), normally without a power feed. Models are typically designated according to their “swing,” or the largest-diameter workpiece that can be rotated; bed length, or the distance between centers; and horsepower generated. See turning machine.
- turning
turning
Workpiece is held in a chuck, mounted on a face plate or secured between centers and rotated while a cutting tool, normally a single-point tool, is fed into it along its periphery or across its end or face. Takes the form of straight turning (cutting along the periphery of the workpiece); taper turning (creating a taper); step turning (turning different-size diameters on the same work); chamfering (beveling an edge or shoulder); facing (cutting on an end); turning threads (usually external but can be internal); roughing (high-volume metal removal); and finishing (final light cuts). Performed on lathes, turning centers, chucking machines, automatic screw machines and similar machines.