Contact Details
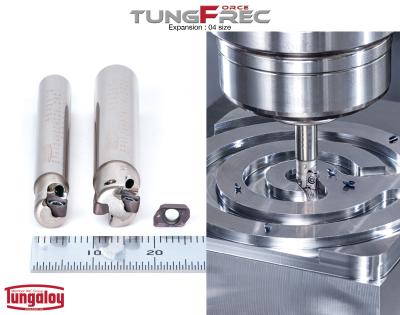
Tungaloy has announced the expansion of TungForce-Rec. The highly productive indexable square shoulder milling cutter series with high insert density now includes 6 mm (.236″) diameter cutter bodies, which is the smallest indexable shoulder mill available in the market, as well as size-04 inserts that are designed for axial cutting depths of up to 4 mm (.157″).
Tool rigidity is a critical factor for small diameter tools to sustain surface quality and process security during machining. Featuring the unique V bottom design of TungForce-Rec inserts in a compact form, the new size-04 inserts enable the cutter body to have a large core diameter and ample insert support, providing high tool rigidity and stability contrary to the small diameter.
The small size-04 inserts also allow TungForce-Rec04 to have a higher teeth density than conventional shoulder cutters of the same size, boasting two teeth for an 8 mm diameter cutter and three for a 10 mm. This allows TungForce-Rec04 to run higher feed speed than competitors when being fed at the same rate per tooth, enabling increased productivity.
An innovative insert design provides the flank face with an obtuse clearance angle for enhanced cutting edge strength and sharpness. Two insert grades are available: AH3225 is the first choice for steel and AH120 is suited for cast iron. Both provides high reliability and long tool life for extremely high shoulder milling productivity. 16 new inserts and cutter bodies are introduced in this expansion.
Related Glossary Terms
- clearance
clearance
Space provided behind a tool’s land or relief to prevent rubbing and subsequent premature deterioration of the tool. See land; relief.
- feed
feed
Rate of change of position of the tool as a whole, relative to the workpiece while cutting.
- gang cutting ( milling)
gang cutting ( milling)
Machining with several cutters mounted on a single arbor, generally for simultaneous cutting.
- milling
milling
Machining operation in which metal or other material is removed by applying power to a rotating cutter. In vertical milling, the cutting tool is mounted vertically on the spindle. In horizontal milling, the cutting tool is mounted horizontally, either directly on the spindle or on an arbor. Horizontal milling is further broken down into conventional milling, where the cutter rotates opposite the direction of feed, or “up” into the workpiece; and climb milling, where the cutter rotates in the direction of feed, or “down” into the workpiece. Milling operations include plane or surface milling, endmilling, facemilling, angle milling, form milling and profiling.
- milling cutter
milling cutter
Loosely, any milling tool. Horizontal cutters take the form of plain milling cutters, plain spiral-tooth cutters, helical cutters, side-milling cutters, staggered-tooth side-milling cutters, facemilling cutters, angular cutters, double-angle cutters, convex and concave form-milling cutters, straddle-sprocket cutters, spur-gear cutters, corner-rounding cutters and slitting saws. Vertical cutters use shank-mounted cutting tools, including endmills, T-slot cutters, Woodruff keyseat cutters and dovetail cutters; these may also be used on horizontal mills. See milling.
- milling machine ( mill)
milling machine ( mill)
Runs endmills and arbor-mounted milling cutters. Features include a head with a spindle that drives the cutters; a column, knee and table that provide motion in the three Cartesian axes; and a base that supports the components and houses the cutting-fluid pump and reservoir. The work is mounted on the table and fed into the rotating cutter or endmill to accomplish the milling steps; vertical milling machines also feed endmills into the work by means of a spindle-mounted quill. Models range from small manual machines to big bed-type and duplex mills. All take one of three basic forms: vertical, horizontal or convertible horizontal/vertical. Vertical machines may be knee-type (the table is mounted on a knee that can be elevated) or bed-type (the table is securely supported and only moves horizontally). In general, horizontal machines are bigger and more powerful, while vertical machines are lighter but more versatile and easier to set up and operate.