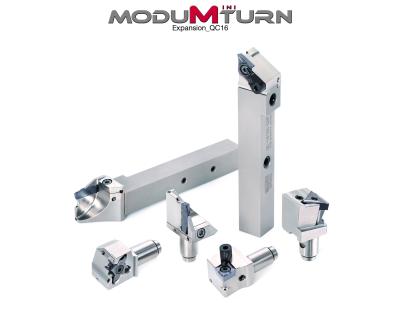
Tungaloy's ModuMini-Turn exchangeable head modular turning tool system for Swiss machines now includes new QC16 line that features 16x16 mm square shanks.
ModuMini-Turn features a unique coupling of the head and shank interface that boasts extremely high repeatability that provides the insert cutting point with a precision of five microns or smaller when the cutting head is re-assembled to the shank. This allows quick tool changes in Swiss machines for minimum downtime.
New QC16 line offers toolholders with 16x16 mm square shanks and the matching modular cutting heads. The new line features an enhanced coupling that is capable of sustaining high cutting edge repeatability and tool rigidity when used for applications generating greater cutting loads that conventional QC12 line was not able to provide reliability with. The QC16 line also offers an array of modular cutting heads to accommodate various types of inserts, including not only standard ISO positive inserts for forward and back O.D. turning, as well as grooving and threading inserts but also cost-efficient double-sided MiniForceTurn negative inserts with positive cutting edges. In addition, modular cutting heads for Y-axis turning are also available allowing shops to use elevated feeds and speeds to gain productivity of small part machining.
Integrating CHP internal coolant channel system that is capable of high pressure coolant supply, ModuMini-Turn toolholder directs the coolant jets precisely to the cutting point close to where it is required for better chip control and to extend insert tool life.
Contact Details
Related Glossary Terms
- coolant
coolant
Fluid that reduces temperature buildup at the tool/workpiece interface during machining. Normally takes the form of a liquid such as soluble or chemical mixtures (semisynthetic, synthetic) but can be pressurized air or other gas. Because of water’s ability to absorb great quantities of heat, it is widely used as a coolant and vehicle for various cutting compounds, with the water-to-compound ratio varying with the machining task. See cutting fluid; semisynthetic cutting fluid; soluble-oil cutting fluid; synthetic cutting fluid.
- grooving
grooving
Machining grooves and shallow channels. Example: grooving ball-bearing raceways. Typically performed by tools that are capable of light cuts at high feed rates. Imparts high-quality finish.
- shank
shank
Main body of a tool; the portion of a drill or similar end-held tool that fits into a collet, chuck or similar mounting device.
- threading
threading
Process of both external (e.g., thread milling) and internal (e.g., tapping, thread milling) cutting, turning and rolling of threads into particular material. Standardized specifications are available to determine the desired results of the threading process. Numerous thread-series designations are written for specific applications. Threading often is performed on a lathe. Specifications such as thread height are critical in determining the strength of the threads. The material used is taken into consideration in determining the expected results of any particular application for that threaded piece. In external threading, a calculated depth is required as well as a particular angle to the cut. To perform internal threading, the exact diameter to bore the hole is critical before threading. The threads are distinguished from one another by the amount of tolerance and/or allowance that is specified. See turning.
- toolholder
toolholder
Secures a cutting tool during a machining operation. Basic types include block, cartridge, chuck, collet, fixed, modular, quick-change and rotating.
- turning
turning
Workpiece is held in a chuck, mounted on a face plate or secured between centers and rotated while a cutting tool, normally a single-point tool, is fed into it along its periphery or across its end or face. Takes the form of straight turning (cutting along the periphery of the workpiece); taper turning (creating a taper); step turning (turning different-size diameters on the same work); chamfering (beveling an edge or shoulder); facing (cutting on an end); turning threads (usually external but can be internal); roughing (high-volume metal removal); and finishing (final light cuts). Performed on lathes, turning centers, chucking machines, automatic screw machines and similar machines.