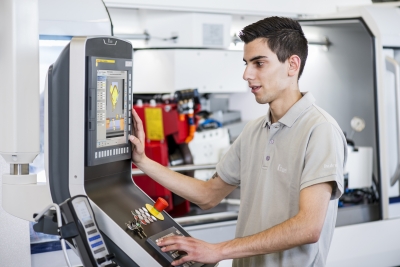
Swiss cylindrical grinding specialist STUDER called on grinding experts to compete against the StuderTechnology computer. Seventy specialists took up the challenge. Each had the same grinding task: Six criteria had to be fulfilled for an optimum grinding result. The result? Only eleven percent of the experts achieved optimal values at the first attempt. The StuderTechnology software achieved 100 percent and thus sets new standards in cylindrical grinding.
Several hundred parameters of a grinding machine determine the machining process for cylindrical grinding. A complex process, which is the preserve of absolute specialists. Or maybe not? The StuderTechnology computer breaks with this opinion, and also breaks records when it comes to grinding. Explained in simple terms, the software automatically determines all necessary data for cylindrical grinding. With just a few inputs the program calculates the production goal and grinds perfectly and with maximum feed at first attempt.
"For 13 years I knew that as a turner I would never be able to grind, the process was too demanding. I was proved wrong. Thanks to StuderTechnology we can now grind complex parts. And bear in mind that we had no employees who could grind. It was a bold decision to invest in the STUDER S33 machine with StuderTechnology, but it was the best decision we have every made", Michael Jauer, CEO of Drehtech AG in Herzogenbuchsee (CH) is still passionate today.
StuderTechnology helps to radically facilitate the operation of cylindrical grinding machines. Component quality, unit costs, machining time, energy efficiency, in short: all key production factors benefit enormously. What makes this software so unique? Its history! It incorporates 107 years of grinding experience. It combines formulas from grinding technology, empirical data and many years of expertise. The program contains data from countless grinding tests, in which the best machining strategy has been determined for a wide variety of components. StuderTechnology takes recourse to these values depending on the specific application and precisely applies them. Imagine a modern camera: You can select automatic programs for different lighting and shooting situations on the dial. These result in optimum images in every situation. And of course you can also choose your own settings. StuderTechnology works in a similar way.
With StuderTechnology you no longer have to be a grinding expert. It is incredibly easy to operate. "In principle, as a production specialist I need to know which parameters are decisive. The tolerances are crucial, on the one hand, and the surfaces on the other. I provide the grinding wheel specifications, the workpiece material and hardness, and decide whether the focus should be on rapid feed or a good surface. On the basis of these values the software suggests the cutting sequence and cutting values. In the past I have always directly adopted the recommendations made by StuderTechnology. This has always worked, from the very first workpiece, without any rejects", explains Marcel Wagner, production manager at Drehtech AG.
The individual times can be drastically reduced. The grinding times alone are generally reduced by 25 to 50 percent. But setup, programming and documentation times are also reduced by using the software. The operator no longer has to laboriously try to find the optimal value. The optimization time is eliminated in most cases. If you use the software consistently, the costs per part are considerably reduced. Or in other words, the production volume can be practically doubled with one and the same machine. As a welcome side effect the energy consumption is also positively influenced, which is why StuderTechnology has been awarded the "Bluecompetence" label.
StuderTechnology has impressed experts since its launch. This innovation won the Prodex Award in 2012 and the INTEC Award in 2013. "The software is exceptionally quick and supports the process so effectively that at best I only need to individually fine tune the grinding parameters suggested by the program", explains Stefan Köhler, master craftsman and grinding division manager at Pabst Komponentenfertigung GmbH.
And what are the disadvantages of this unique STUDER solution? "Grinders are cautious souls and take a careful approach to machining. StuderTechnology goes all out", explains Daniel Zürcher, customer center training manager at Fritz Studer AG. "So to completely rely on the software takes some willpower, but it pays off every time." He knows from his own experience.
A workpiece drawing or work instruction is always provided as the starting point. This shows the dimensional, form, position and surface tolerances. The user is repeatedly faced with the question of how he must set the machine, in order to fulfill the requirements. To be as quick as possible? Or as precise as possible? He must also include material and hardness, as well as abrasive and cooling lubricant, in his decision. From these variables he derives his setting values, which are shaped by personal experience, and thus his production goal.
StuderTechnology suggests such production goals. The "Normal grinding" production goal stands for applications in the tolerance range ~ H5/h5 and surface quality ~ Ra 0.3. The production goal for increased removal capacity can be used for pregrinding operations in particular. The program provides two further production goals for higher precision or higher surface quality.
You can rarely achieve the optimal grinding result without support. A great advantage of StuderTechnology is that it takes account of the machine characteristics and the configuration of the grinding cycles. Grinding wheels and dressing tools can be used for much longer, as abrasive is not removed unnecessarily, which in turn results in less wear.
Grinding is an exacting science. StuderTechnology provides companies with a tool which anyone can use for grinding. It also offers experts targeted support. Thanks to the new teach-in function, operators can save their own programs.
The workpiece boasts better roundness and surface roughness. Good quality and a quick, stable process are achieved at first attempt, independently of the operator. Through the reduction of error costs, shorter grinding times, lower tool costs and the elimination of complicated calculations, productivity can often be increased by 50 percent. "The STUDER specialists told us that StuderTechnology would be of enormous support to us in setting up and programming the machine. We were skeptical, as promises are easy to make. But everything that STUDER promised us was true. Perhaps even more so, which was really impressive", acknowledges Wagner.
Contact Details
Related Glossary Terms
- abrasive
abrasive
Substance used for grinding, honing, lapping, superfinishing and polishing. Examples include garnet, emery, corundum, silicon carbide, cubic boron nitride and diamond in various grit sizes.
- cylindrical grinding
cylindrical grinding
Grinding operation in which the workpiece is rotated around a fixed axis while the grinding wheel is fed into the outside surface in controlled relation to the axis of rotation. The workpiece is usually cylindrical, but it may be tapered or curvilinear in profile. See centerless grinding; grinding.
- dressing
dressing
Removal of undesirable materials from “loaded” grinding wheels using a single- or multi-point diamond or other tool. The process also exposes unused, sharp abrasive points. See loading; truing.
- feed
feed
Rate of change of position of the tool as a whole, relative to the workpiece while cutting.
- grinding
grinding
Machining operation in which material is removed from the workpiece by a powered abrasive wheel, stone, belt, paste, sheet, compound, slurry, etc. Takes various forms: surface grinding (creates flat and/or squared surfaces); cylindrical grinding (for external cylindrical and tapered shapes, fillets, undercuts, etc.); centerless grinding; chamfering; thread and form grinding; tool and cutter grinding; offhand grinding; lapping and polishing (grinding with extremely fine grits to create ultrasmooth surfaces); honing; and disc grinding.
- grinding machine
grinding machine
Powers a grinding wheel or other abrasive tool for the purpose of removing metal and finishing workpieces to close tolerances. Provides smooth, square, parallel and accurate workpiece surfaces. When ultrasmooth surfaces and finishes on the order of microns are required, lapping and honing machines (precision grinders that run abrasives with extremely fine, uniform grits) are used. In its “finishing” role, the grinder is perhaps the most widely used machine tool. Various styles are available: bench and pedestal grinders for sharpening lathe bits and drills; surface grinders for producing square, parallel, smooth and accurate parts; cylindrical and centerless grinders; center-hole grinders; form grinders; facemill and endmill grinders; gear-cutting grinders; jig grinders; abrasive belt (backstand, swing-frame, belt-roll) grinders; tool and cutter grinders for sharpening and resharpening cutting tools; carbide grinders; hand-held die grinders; and abrasive cutoff saws.
- grinding wheel
grinding wheel
Wheel formed from abrasive material mixed in a suitable matrix. Takes a variety of shapes but falls into two basic categories: one that cuts on its periphery, as in reciprocating grinding, and one that cuts on its side or face, as in tool and cutter grinding.
- hardness
hardness
Hardness is a measure of the resistance of a material to surface indentation or abrasion. There is no absolute scale for hardness. In order to express hardness quantitatively, each type of test has its own scale, which defines hardness. Indentation hardness obtained through static methods is measured by Brinell, Rockwell, Vickers and Knoop tests. Hardness without indentation is measured by a dynamic method, known as the Scleroscope test.
- tolerance
tolerance
Minimum and maximum amount a workpiece dimension is allowed to vary from a set standard and still be acceptable.