Contact Details
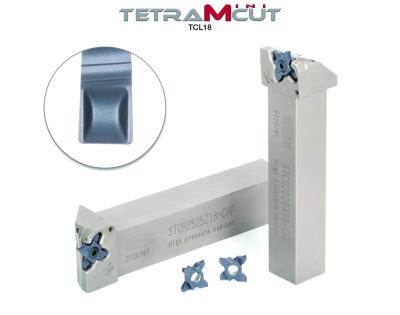
Designed to ensure low cutting force, the TCL18-style chipbreaker is the latest addition to Tungaloy’s TetraMini-Cut line of grooving inserts offering four cutting edges. TetraMini-Cut features a compact grooving insert with economical four cutting edges. Its innovative insert clamping ensures secure insert retention and high repeatability, promising machining accuracy and tool life predictability.
TCL18 ensures light cutting action and effective chip control when fed at low feed rates. The insert is coated in AH7025, a nano-multilayer PVD coating with high-aluminum content that provides hardness and adhesion to the grade for better process security during grooving operations.
The newest addition of TCL18 to the existing TCS18-, TCG18- and TCP18-style chipbreakers will further enhance the TetraMini-Cut insert family to meet the vast needs of grooving applications in general to miniature parts.
At a glance:
TCL18 ensures effective chip control at low feed rates
Available in AH7025, a dedicated grade for grooving operations, featuring a nano-multilayer PVD coating with high-aluminum content that provides hardness and adhesion to the grade for wear and fracture resistance
Designed for grooving an extensive range of materials from steel, alloy steel, stainless steel and heat-resistant alloys
Related Glossary Terms
- alloys
alloys
Substances having metallic properties and being composed of two or more chemical elements of which at least one is a metal.
- chipbreaker
chipbreaker
Groove or other tool geometry that breaks chips into small fragments as they come off the workpiece. Designed to prevent chips from becoming so long that they are difficult to control, catch in turning parts and cause safety problems.
- cutting force
cutting force
Engagement of a tool’s cutting edge with a workpiece generates a cutting force. Such a cutting force combines tangential, feed and radial forces, which can be measured by a dynamometer. Of the three cutting force components, tangential force is the greatest. Tangential force generates torque and accounts for more than 95 percent of the machining power. See dynamometer.
- feed
feed
Rate of change of position of the tool as a whole, relative to the workpiece while cutting.
- grooving
grooving
Machining grooves and shallow channels. Example: grooving ball-bearing raceways. Typically performed by tools that are capable of light cuts at high feed rates. Imparts high-quality finish.
- hardness
hardness
Hardness is a measure of the resistance of a material to surface indentation or abrasion. There is no absolute scale for hardness. In order to express hardness quantitatively, each type of test has its own scale, which defines hardness. Indentation hardness obtained through static methods is measured by Brinell, Rockwell, Vickers and Knoop tests. Hardness without indentation is measured by a dynamic method, known as the Scleroscope test.
- physical vapor deposition ( PVD)
physical vapor deposition ( PVD)
Tool-coating process performed at low temperature (500° C), compared to chemical vapor deposition (1,000° C). Employs electric field to generate necessary heat for depositing coating on a tool’s surface. See CVD, chemical vapor deposition.