Contact Details
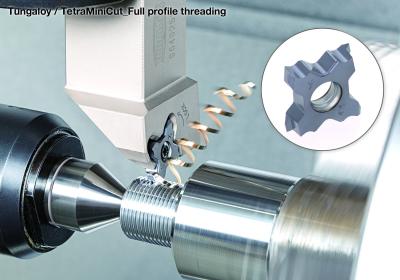
Tungaloy is expanding its TetraMini-Cut, an indexable thread turning tool series with four-edged insert, to include full profile threading inserts for machining external threads in ISO metric thread standards.
The TetraMini-Cut insert comes in a compact profile with four economical cutting edges. Its unique insert clamping ensures high repeatability, accuracy and tool life predictability. The new full profile threading insert can be mounted on the existing standard TetraMini-Cut toolholder for 60° V-profile or grooving inserts. Since the insert cuts a complete thread profile including the crest, no deburring of the thread profile is needed. In addition, the optimized tool design provides minimal interference when turning towards the tailstock of the lathe. Inserts are offered in two grades: SH725 allows free cutting of fine pitch threads in small diameter bores and AH725 for universal threading applications on Swiss-type machines, as well as general lathes. The enhanced lineup of TetraMini-Cut series provides customers with increased productivity.
At a Glance:
Full profile threading insert with four cost-effective cutting edges
Complete thread profiling is possible with no need for deburring of the crest
Available in SH725 and AH725 to address varieties of thread pitches
Applicable for thread pitches ranging from 0.5 mm to 1.5 mm of external ISO metric threads
Eliminates interference when turning towards the lathe tailstock.
Seven inserts will be added in this expansion
Related Glossary Terms
- grooving
grooving
Machining grooves and shallow channels. Example: grooving ball-bearing raceways. Typically performed by tools that are capable of light cuts at high feed rates. Imparts high-quality finish.
- lathe
lathe
Turning machine capable of sawing, milling, grinding, gear-cutting, drilling, reaming, boring, threading, facing, chamfering, grooving, knurling, spinning, parting, necking, taper-cutting, and cam- and eccentric-cutting, as well as step- and straight-turning. Comes in a variety of forms, ranging from manual to semiautomatic to fully automatic, with major types being engine lathes, turning and contouring lathes, turret lathes and numerical-control lathes. The engine lathe consists of a headstock and spindle, tailstock, bed, carriage (complete with apron) and cross slides. Features include gear- (speed) and feed-selector levers, toolpost, compound rest, lead screw and reversing lead screw, threading dial and rapid-traverse lever. Special lathe types include through-the-spindle, camshaft and crankshaft, brake drum and rotor, spinning and gun-barrel machines. Toolroom and bench lathes are used for precision work; the former for tool-and-die work and similar tasks, the latter for small workpieces (instruments, watches), normally without a power feed. Models are typically designated according to their “swing,” or the largest-diameter workpiece that can be rotated; bed length, or the distance between centers; and horsepower generated. See turning machine.
- pitch
pitch
1. On a saw blade, the number of teeth per inch. 2. In threading, the number of threads per inch.
- profiling
profiling
Machining vertical edges of workpieces having irregular contours; normally performed with an endmill in a vertical spindle on a milling machine or with a profiler, following a pattern. See mill, milling machine.
- threading
threading
Process of both external (e.g., thread milling) and internal (e.g., tapping, thread milling) cutting, turning and rolling of threads into particular material. Standardized specifications are available to determine the desired results of the threading process. Numerous thread-series designations are written for specific applications. Threading often is performed on a lathe. Specifications such as thread height are critical in determining the strength of the threads. The material used is taken into consideration in determining the expected results of any particular application for that threaded piece. In external threading, a calculated depth is required as well as a particular angle to the cut. To perform internal threading, the exact diameter to bore the hole is critical before threading. The threads are distinguished from one another by the amount of tolerance and/or allowance that is specified. See turning.
- toolholder
toolholder
Secures a cutting tool during a machining operation. Basic types include block, cartridge, chuck, collet, fixed, modular, quick-change and rotating.
- turning
turning
Workpiece is held in a chuck, mounted on a face plate or secured between centers and rotated while a cutting tool, normally a single-point tool, is fed into it along its periphery or across its end or face. Takes the form of straight turning (cutting along the periphery of the workpiece); taper turning (creating a taper); step turning (turning different-size diameters on the same work); chamfering (beveling an edge or shoulder); facing (cutting on an end); turning threads (usually external but can be internal); roughing (high-volume metal removal); and finishing (final light cuts). Performed on lathes, turning centers, chucking machines, automatic screw machines and similar machines.