Contact Details
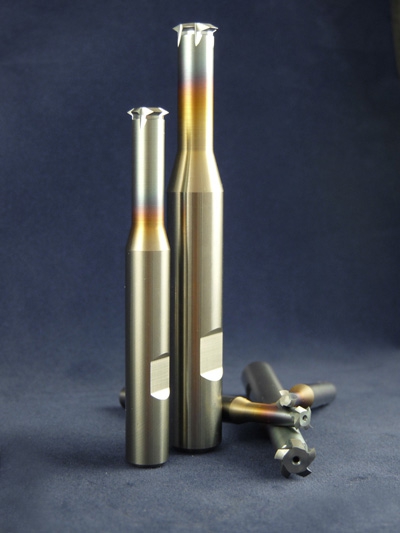
Emuge Corp. offers an expanded line of solid-carbide thread mills in its THREADS-ALL program, to include new 3XD sizes designed for maximum reach. A total of 17 new sizes have been added, from miniature to standard size tools, providing maximum versatility in a wide range of thread milling applications.
The 3XD THREADS-ALL tools, as well as the 2XD offering, enable easy machining of a variety of difficult-to-cut materials such as stainless, titanium and inconel, most often used in the demanding industries of aerospace, defense and medical. Both 2XD and 3XD THREADS-ALL tools provide a single tool solution for through and blind holes and offer full bottom threading to within one pitch. With THREADS-ALL, pitch diameter can be easily controlled. In addition, STI threads can be readily produced with THREADS-ALL, ideal for aerospace threading applications.
Emuge's new ZGF-I 3XD Thread Mills require only eight stock standard tool sizes, #10,¼, 5/16, 3/8, 7/16,½, 5⁄8, ¾, that allow for over 100 commonly produced screw thread designations. The ZGF-I 3XD line also includes Miniature size thread mills, available in four sizes ranging from 2 to 8.
Emuge's new thread mill range produces excellent thread finish and gaging to meet today's most demanding quality standards, while helping manufacturers reduce costs and improve delivery.
"Emuge understands the challenges of today's threading applications," said Emuge Corp. Product Director, Mark Hatch. "The new 3XD sizes in the THREADS-ALL program will give manufacturers additional versatility, and enable them to minimize tool inventories and help increase profitability."
Related Glossary Terms
- gang cutting ( milling)
gang cutting ( milling)
Machining with several cutters mounted on a single arbor, generally for simultaneous cutting.
- milling
milling
Machining operation in which metal or other material is removed by applying power to a rotating cutter. In vertical milling, the cutting tool is mounted vertically on the spindle. In horizontal milling, the cutting tool is mounted horizontally, either directly on the spindle or on an arbor. Horizontal milling is further broken down into conventional milling, where the cutter rotates opposite the direction of feed, or “up” into the workpiece; and climb milling, where the cutter rotates in the direction of feed, or “down” into the workpiece. Milling operations include plane or surface milling, endmilling, facemilling, angle milling, form milling and profiling.
- milling machine ( mill)
milling machine ( mill)
Runs endmills and arbor-mounted milling cutters. Features include a head with a spindle that drives the cutters; a column, knee and table that provide motion in the three Cartesian axes; and a base that supports the components and houses the cutting-fluid pump and reservoir. The work is mounted on the table and fed into the rotating cutter or endmill to accomplish the milling steps; vertical milling machines also feed endmills into the work by means of a spindle-mounted quill. Models range from small manual machines to big bed-type and duplex mills. All take one of three basic forms: vertical, horizontal or convertible horizontal/vertical. Vertical machines may be knee-type (the table is mounted on a knee that can be elevated) or bed-type (the table is securely supported and only moves horizontally). In general, horizontal machines are bigger and more powerful, while vertical machines are lighter but more versatile and easier to set up and operate.
- pitch
pitch
1. On a saw blade, the number of teeth per inch. 2. In threading, the number of threads per inch.
- threading
threading
Process of both external (e.g., thread milling) and internal (e.g., tapping, thread milling) cutting, turning and rolling of threads into particular material. Standardized specifications are available to determine the desired results of the threading process. Numerous thread-series designations are written for specific applications. Threading often is performed on a lathe. Specifications such as thread height are critical in determining the strength of the threads. The material used is taken into consideration in determining the expected results of any particular application for that threaded piece. In external threading, a calculated depth is required as well as a particular angle to the cut. To perform internal threading, the exact diameter to bore the hole is critical before threading. The threads are distinguished from one another by the amount of tolerance and/or allowance that is specified. See turning.