Contact Details
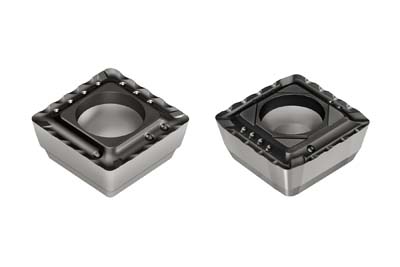
Walter USA LLC has announced that Tiger-tec Silver, its high-performance aluminum oxide coating that has been boosting the productivity of its milling and turning inserts, is now available for its Xtra-tec Insert Drills as well. The addition of Tiger-tec Silver to the drills has been able to boost productivity, increase process reliability, and lower tooling costs.
The new coating combines high temperature wear resistance and superior toughness. This combination is desirable in any application but particularly in drilling. In drilling, the cutting edges must be able to withstand relatively high cutting speeds and forces at the outer edge, but these speeds and forces diminish as one approaches the center of the drill. In order to cope successfully and economically with such disparate and therefore difficult machining conditions, a cutting tool material that couples high temperature wear resistance with excellent toughness is required.
Tiger-tec Silver's heat resistant feature promotes higher productivity by allowing higher speeds, while its toughness promotes higher process reliability, both helping to lengthen tool life and reduce tooling costs.
The new coating is available with several insert materials. For example, the cutting materials WKP25S and WKP35S are suitable for all cast iron and steel materials. If extreme toughness at the drill center is required, as is often the case when machining ISO-P, ISO-M or ISO-S materials, Walter has a PVD coated center indexable insert made of the cutting tool material WXP40 as an alternative. This cutting material is designed for maximum toughness and guarantees optimum process reliability.
Related Glossary Terms
- aluminum oxide
aluminum oxide
Aluminum oxide, also known as corundum, is used in grinding wheels. The chemical formula is Al2O3. Aluminum oxide is the base for ceramics, which are used in cutting tools for high-speed machining with light chip removal. Aluminum oxide is widely used as coating material applied to carbide substrates by chemical vapor deposition. Coated carbide inserts with Al2O3 layers withstand high cutting speeds, as well as abrasive and crater wear.
- gang cutting ( milling)
gang cutting ( milling)
Machining with several cutters mounted on a single arbor, generally for simultaneous cutting.
- indexable insert
indexable insert
Replaceable tool that clamps into a tool body, drill, mill or other cutter body designed to accommodate inserts. Most inserts are made of cemented carbide. Often they are coated with a hard material. Other insert materials are ceramic, cermet, polycrystalline cubic boron nitride and polycrystalline diamond. The insert is used until dull, then indexed, or turned, to expose a fresh cutting edge. When the entire insert is dull, it is usually discarded. Some inserts can be resharpened.
- milling
milling
Machining operation in which metal or other material is removed by applying power to a rotating cutter. In vertical milling, the cutting tool is mounted vertically on the spindle. In horizontal milling, the cutting tool is mounted horizontally, either directly on the spindle or on an arbor. Horizontal milling is further broken down into conventional milling, where the cutter rotates opposite the direction of feed, or “up” into the workpiece; and climb milling, where the cutter rotates in the direction of feed, or “down” into the workpiece. Milling operations include plane or surface milling, endmilling, facemilling, angle milling, form milling and profiling.
- physical vapor deposition ( PVD)
physical vapor deposition ( PVD)
Tool-coating process performed at low temperature (500° C), compared to chemical vapor deposition (1,000° C). Employs electric field to generate necessary heat for depositing coating on a tool’s surface. See CVD, chemical vapor deposition.
- turning
turning
Workpiece is held in a chuck, mounted on a face plate or secured between centers and rotated while a cutting tool, normally a single-point tool, is fed into it along its periphery or across its end or face. Takes the form of straight turning (cutting along the periphery of the workpiece); taper turning (creating a taper); step turning (turning different-size diameters on the same work); chamfering (beveling an edge or shoulder); facing (cutting on an end); turning threads (usually external but can be internal); roughing (high-volume metal removal); and finishing (final light cuts). Performed on lathes, turning centers, chucking machines, automatic screw machines and similar machines.
- wear resistance
wear resistance
Ability of the tool to withstand stresses that cause it to wear during cutting; an attribute linked to alloy composition, base material, thermal conditions, type of tooling and operation and other variables.