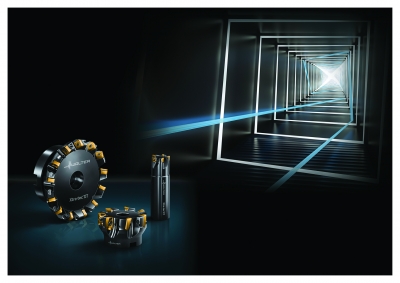
Walter has introduced its next generation of milling tools: the Xtra·tec XT (Xtended Technology). Designed to achieve increased productivity and process reliability, this new generation of milling cutters is being launched with initial offerings of shoulder milling cutters and a facemilling cutter. The mills cover virtually all requirements in shoulder and slot milling in all common material groups.
The key design feature of these new milling tools is the position of the indexable inserts, which is at a greater incline and with a larger contact surface. This reduces the surface pressure in the seat while increasing stability. Their larger screw hole cross-section stabilizes the indexable insert, and the longer screws hold it in place more securely. The cutter body has also been made more stable, as it now has more material behind the insert seat.
Along with greater process reliability, the new position of the indexable inserts also allows for the addition of an extra tooth, thereby increasing productivity. The precise 90° shape of the shoulder milling cutters helps reduce the need for additional finishing operations. The clamping screws, which are easier to access, optimize handling.
Another significant new feature is the smaller indexable inserts that can be fitted to the Xtra·tec XT milling cutters, continuing today’s trend towards reduced machining allowances. This applies especially to the Xtra·tec XT M5009 facemilling cutter, which combines small depths of cut with the advantages of the double-sided Walter Tiger·tec indexable inserts. These inserts have eight useable cutting edges instead of the usual four providing increased efficiency plus fewer required finishing operations.
Contact Details
Related Glossary Terms
- facemilling
facemilling
Form of milling that produces a flat surface generally at right angles to the rotating axis of a cutter having teeth or inserts both on its periphery and on its end face.
- gang cutting ( milling)
gang cutting ( milling)
Machining with several cutters mounted on a single arbor, generally for simultaneous cutting.
- indexable insert
indexable insert
Replaceable tool that clamps into a tool body, drill, mill or other cutter body designed to accommodate inserts. Most inserts are made of cemented carbide. Often they are coated with a hard material. Other insert materials are ceramic, cermet, polycrystalline cubic boron nitride and polycrystalline diamond. The insert is used until dull, then indexed, or turned, to expose a fresh cutting edge. When the entire insert is dull, it is usually discarded. Some inserts can be resharpened.
- milling
milling
Machining operation in which metal or other material is removed by applying power to a rotating cutter. In vertical milling, the cutting tool is mounted vertically on the spindle. In horizontal milling, the cutting tool is mounted horizontally, either directly on the spindle or on an arbor. Horizontal milling is further broken down into conventional milling, where the cutter rotates opposite the direction of feed, or “up” into the workpiece; and climb milling, where the cutter rotates in the direction of feed, or “down” into the workpiece. Milling operations include plane or surface milling, endmilling, facemilling, angle milling, form milling and profiling.