Contact Details
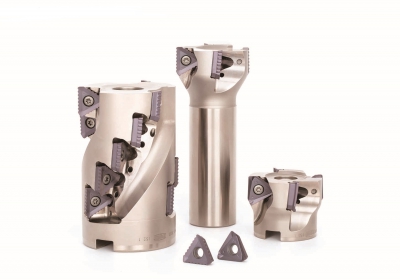
Tungaloy Corp. introduces TungTri-Shred, a new shoulder milling cutter for highly productive machining. With today’s dramatic growth in the performance of machine tools, high-speed machining is often the first choice for manufacturers. In high-speed machining, vibration of the tool, the machine or the workpiece can cause chattering. If the depth or the width of cut is increased, the revolution or the feed will need to be reduced. If the revolution or the feed is increased, the depth or the width of cut must be reduced as well. These are factors that limit milling productivity.
TungTri-Shred offers a solution to this issue. The inserts are available in two types: an NMJ insert with serrated cutting edges for roughing and an MJ insert with straight cutting edges for finishing. The NMJ insert provides high performance in roughing operations by shredding chips and minimizing chattering, while the MJ insert, with its straight cutting edges, provides a smooth finish on the wall without step marks.
The TungTri-Shred cutter body features innovative chip shredding technology: Insert pockets are located on the flute so that its cutting edges are positioned in alignment without overlapping one another. This unique design helps the NMJ insert produce small chips with reduced cutting force. The MJ insert leaves an fine wall surface finish. TungTri-Shred’s insert cutting edges all use the same geometry, eliminating the chance for improper mounting and simplifying the indexing process.
The tool diameters start at 2.00” (50 mm) in the standard and the long shank types; 2.00”- 4.00” (50-100 mm) for the bore type; and 2.50” and 3.00” (63 and 80 mm) in the extended-flute type.
Related Glossary Terms
- cutting force
cutting force
Engagement of a tool’s cutting edge with a workpiece generates a cutting force. Such a cutting force combines tangential, feed and radial forces, which can be measured by a dynamometer. Of the three cutting force components, tangential force is the greatest. Tangential force generates torque and accounts for more than 95 percent of the machining power. See dynamometer.
- feed
feed
Rate of change of position of the tool as a whole, relative to the workpiece while cutting.
- gang cutting ( milling)
gang cutting ( milling)
Machining with several cutters mounted on a single arbor, generally for simultaneous cutting.
- milling
milling
Machining operation in which metal or other material is removed by applying power to a rotating cutter. In vertical milling, the cutting tool is mounted vertically on the spindle. In horizontal milling, the cutting tool is mounted horizontally, either directly on the spindle or on an arbor. Horizontal milling is further broken down into conventional milling, where the cutter rotates opposite the direction of feed, or “up” into the workpiece; and climb milling, where the cutter rotates in the direction of feed, or “down” into the workpiece. Milling operations include plane or surface milling, endmilling, facemilling, angle milling, form milling and profiling.
- milling cutter
milling cutter
Loosely, any milling tool. Horizontal cutters take the form of plain milling cutters, plain spiral-tooth cutters, helical cutters, side-milling cutters, staggered-tooth side-milling cutters, facemilling cutters, angular cutters, double-angle cutters, convex and concave form-milling cutters, straddle-sprocket cutters, spur-gear cutters, corner-rounding cutters and slitting saws. Vertical cutters use shank-mounted cutting tools, including endmills, T-slot cutters, Woodruff keyseat cutters and dovetail cutters; these may also be used on horizontal mills. See milling.
- shank
shank
Main body of a tool; the portion of a drill or similar end-held tool that fits into a collet, chuck or similar mounting device.
- width of cut
width of cut
Width of the milled surface, reflecting a face milling cutter’s radial engagement, and a peripheral milling cutter’s axial engagement, in the cut.