Contact Details
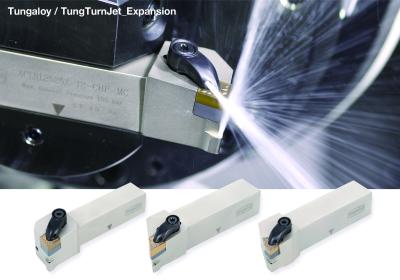
Tungaloy is expanding its TungTurn-Jet series of high-pressure coolant capable turning holders by adding a coolant-through feature and Double-Clamp technology for rigid insert holding and high productivity.
The TungTurn-Jet holder strategically directs the internal coolant jet exactly where it is needed, close to the cutting point on the insert rake face. This dramatically improves chip control during the machining of difficult-to-cut materials, which is not the case with conventional coolant delivery methods. In addition, the other coolant jet is fed from the bottom to minimize flank wear for increased insert life and productivity.
The new TungTurn-Jet holder’s Double-Clamp technology allows the insert to be clamped and pulled towards the wall simultaneously with a single clamp screw operation for rigid insert holding. Now the clamp accommodates an internal coolant exit aperture built into it to deliver coolant jet to the optimal position on the cutting point for improved chip control. The internal coolant can be supplied either by using conventional external coolant subassembly or directly through applicable adapter of DirectTungJet-compatible machines.
At a glance:
The clamp provides secure insert retention and through-coolant supply
Hybrid through-coolant connection design allows the holder to be used on DirectTungJet-compatible machines or with conventional external coolant subassembly
Coolant jets from top and bottom dramatically improve chip control and insert life
Related Glossary Terms
- coolant
coolant
Fluid that reduces temperature buildup at the tool/workpiece interface during machining. Normally takes the form of a liquid such as soluble or chemical mixtures (semisynthetic, synthetic) but can be pressurized air or other gas. Because of water’s ability to absorb great quantities of heat, it is widely used as a coolant and vehicle for various cutting compounds, with the water-to-compound ratio varying with the machining task. See cutting fluid; semisynthetic cutting fluid; soluble-oil cutting fluid; synthetic cutting fluid.
- flank wear
flank wear
Reduction in clearance on the tool’s flank caused by contact with the workpiece. Ultimately causes tool failure.
- rake
rake
Angle of inclination between the face of the cutting tool and the workpiece. If the face of the tool lies in a plane through the axis of the workpiece, the tool is said to have a neutral, or zero, rake. If the inclination of the tool face makes the cutting edge more acute than when the rake angle is zero, the rake is positive. If the inclination of the tool face makes the cutting edge less acute or more blunt than when the rake angle is zero, the rake is negative.
- turning
turning
Workpiece is held in a chuck, mounted on a face plate or secured between centers and rotated while a cutting tool, normally a single-point tool, is fed into it along its periphery or across its end or face. Takes the form of straight turning (cutting along the periphery of the workpiece); taper turning (creating a taper); step turning (turning different-size diameters on the same work); chamfering (beveling an edge or shoulder); facing (cutting on an end); turning threads (usually external but can be internal); roughing (high-volume metal removal); and finishing (final light cuts). Performed on lathes, turning centers, chucking machines, automatic screw machines and similar machines.