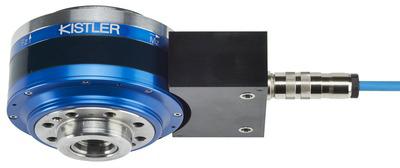
Kistler expands its range of RCDs (Rotating Cutting Force Dynamometers) with the new Type 9171A rotating dynamometer for use in high-performance cutting applications. Type 9171A measures forces and torques even under very heavy loads and thereby allows machining processes to be analyzed and optimized while drawing conclusions on tool wear. The fully revamped piezoelectric dynamometer delivers a much larger range of spindle speed, improved dynamic properties, and a sig-nificant weight reduction.
The latest generation of the Type 9171A 4-component RCD adds a particularly robust model to the existing RCD family, delivering perfect measuring results even under in-creased loads. Like all stationary and rotating dynamometers from Kistler, the Type 9171A also includes a piezoelectric sensor, which is able to measure forces and torques in the machining process with extreme precision thanks to its especially high rigidity and natural frequency.
The fully revamped successor to Type 9124B displays numerous improvements: 2.5 times the range of spindle speed, improved dynamic properties, and a significant weight reduction over the previous RCD allow forces and torques to be measured under high loads. The use of a new, fully rotationally symmetrical 4-component force sensor minimizes the influence of centrifugal forces, while more powerful system electronics deliver superlative signal quality.
With a large force range of up to 20 kN (Fx, Fy) or 30 kN (Fz) and a maximum torque of 1000 Nm, the RCD Type 9171A is perfectly equipped for machining processes in extreme ranges. High-performance cutting is characterized by removal of very large volumes of material in a short time. It involves very large forces and very high torques. The large measuring range and the compact design make the RCD Type 9171A well suited to the spindle interfaces HSK-A100 and Capto C8 often used in HPC. Smaller spindle adapters can, however, also be used.
Kistler dynamometers have an impressively robust and compact design and are easy to use. The Type 9171A rotating dynamometer is inserted in the machine spindle like a standard toolholder. Various designs of spindle adapter and toolholder are available from Kistler and can be inter-changed by the customer. This enables users who use different spindle interfaces on their machine tools to equip the RCD as required.
Measurement data is transferred and energy is supplied through a noncontact near-field telemetry, which permits greater distances between rotor and stator. With immediate effect, three different low-pass filter levels can be set. The individual force and torque ranges can also be selected inde-pendently of one another, making optimum signal control possible.
Contact Details
Related Glossary Terms
- cutting force
cutting force
Engagement of a tool’s cutting edge with a workpiece generates a cutting force. Such a cutting force combines tangential, feed and radial forces, which can be measured by a dynamometer. Of the three cutting force components, tangential force is the greatest. Tangential force generates torque and accounts for more than 95 percent of the machining power. See dynamometer.
- dynamometer
dynamometer
When drilling, a device for measuring the generated torque and axial force (thrust). When milling, a device for measuring the generated torque and feed force. When turning, a device for measuring the tangential, feed and radial forces.
- spindle adapter
spindle adapter
Bushing or toolholder that permits affixing a variety of taper- and straight-shank tools to a machine spindle.
- toolholder
toolholder
Secures a cutting tool during a machining operation. Basic types include block, cartridge, chuck, collet, fixed, modular, quick-change and rotating.