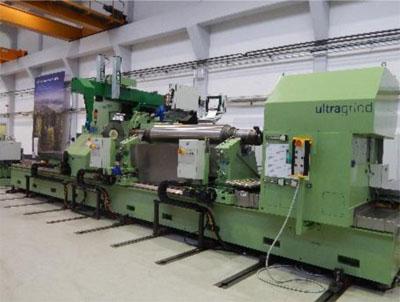
At the occasion of a customer day, Heinrich Georg GmbH Maschinenfabrik presented its new roll grinding machine type ultragrind 700 R. The new machine is designed for center lengths of 5,000mm, grinding diameters of up to 700mm and roll weights up to 10 tons. The machine works fully automatically and reportedly impresses by its high grinding qualities in conventional and CBN grinding. Due to many special design solutions, its solid structure and innovative measuring technologies the machine achieves high precision and at the same time short setting and machining cycles.
More than 70 experts from roll grinding shops of leading steel and aluminum producers as well as experts from roll manufacturers and engineering offices came to see the machine in "live" operation prior to dispatch to the customer Baosteel, China. At first Georg demonstrated the grinding of a work roll in the conventional way and later in CBN technology. In addition GEORG displayed a HSS work roll of a hot rolling mill with CVC profile and a profile height of 1,85mm that had been ground before with a CBN disc.
During the demonstrations the visitors could inspect the high quality of the machine. According to the company, everyone was impressed by the fine surface quality of the ground rolls, neither comma nor feed marks could be detected. They confirmed that whilst the grinding operations took place no vibrations or swing motions of the machine could be felt and that the machine was running very smooth; this applies to the conventional and to the CBN grinding method as well.
A number of design measures enable Georg to reach excellent grinding results, short handling and machining cycles, as well as a long lifetime of the machine. Just to mention the headstock that can be displaced as a whole with fixed main axis and displaceable counter part, the hydrostatic bearing of the grinding spindle and the grinding carriage, the very precise U-axis with a resolution of 0,01 µm, the U1-axis for exact horizontal roll alignment and finally the complete equipment of measuring and control techniques.
Contact Details
Related Glossary Terms
- cubic boron nitride ( CBN)
cubic boron nitride ( CBN)
Crystal manufactured from boron nitride under high pressure and temperature. Used to cut hard-to-machine ferrous and nickel-base materials up to 70 HRC. Second hardest material after diamond. See superabrasive tools.
- feed
feed
Rate of change of position of the tool as a whole, relative to the workpiece while cutting.
- grinding
grinding
Machining operation in which material is removed from the workpiece by a powered abrasive wheel, stone, belt, paste, sheet, compound, slurry, etc. Takes various forms: surface grinding (creates flat and/or squared surfaces); cylindrical grinding (for external cylindrical and tapered shapes, fillets, undercuts, etc.); centerless grinding; chamfering; thread and form grinding; tool and cutter grinding; offhand grinding; lapping and polishing (grinding with extremely fine grits to create ultrasmooth surfaces); honing; and disc grinding.
- grinding machine
grinding machine
Powers a grinding wheel or other abrasive tool for the purpose of removing metal and finishing workpieces to close tolerances. Provides smooth, square, parallel and accurate workpiece surfaces. When ultrasmooth surfaces and finishes on the order of microns are required, lapping and honing machines (precision grinders that run abrasives with extremely fine, uniform grits) are used. In its “finishing” role, the grinder is perhaps the most widely used machine tool. Various styles are available: bench and pedestal grinders for sharpening lathe bits and drills; surface grinders for producing square, parallel, smooth and accurate parts; cylindrical and centerless grinders; center-hole grinders; form grinders; facemill and endmill grinders; gear-cutting grinders; jig grinders; abrasive belt (backstand, swing-frame, belt-roll) grinders; tool and cutter grinders for sharpening and resharpening cutting tools; carbide grinders; hand-held die grinders; and abrasive cutoff saws.
- high-speed steels ( HSS)
high-speed steels ( HSS)
Available in two major types: tungsten high-speed steels (designated by letter T having tungsten as the principal alloying element) and molybdenum high-speed steels (designated by letter M having molybdenum as the principal alloying element). The type T high-speed steels containing cobalt have higher wear resistance and greater red (hot) hardness, withstanding cutting temperature up to 1,100º F (590º C). The type T steels are used to fabricate metalcutting tools (milling cutters, drills, reamers and taps), woodworking tools, various types of punches and dies, ball and roller bearings. The type M steels are used for cutting tools and various types of dies.
- milling machine ( mill)
milling machine ( mill)
Runs endmills and arbor-mounted milling cutters. Features include a head with a spindle that drives the cutters; a column, knee and table that provide motion in the three Cartesian axes; and a base that supports the components and houses the cutting-fluid pump and reservoir. The work is mounted on the table and fed into the rotating cutter or endmill to accomplish the milling steps; vertical milling machines also feed endmills into the work by means of a spindle-mounted quill. Models range from small manual machines to big bed-type and duplex mills. All take one of three basic forms: vertical, horizontal or convertible horizontal/vertical. Vertical machines may be knee-type (the table is mounted on a knee that can be elevated) or bed-type (the table is securely supported and only moves horizontally). In general, horizontal machines are bigger and more powerful, while vertical machines are lighter but more versatile and easier to set up and operate.