Contact Details
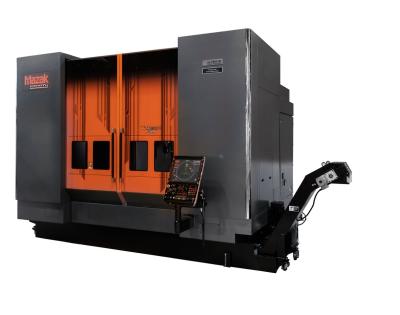
Mazak Corp.'s family of hybrid multitask machining centers includes the VTC-300C FSW, which combines advanced milling capabilities with friction stir welding (FSW) technology. With a full traveling-column design, automatic toolchanger and powerful 40-taper spindle in addition to the FSW package, this machine helps shops achieve reduced lead times and greater part accuracy with less required capital equipment and floor space – all while enabling completely novel methods for processing parts with strong welds.
Designed and manufactured in Kentucky in partnership with the Provo, Utah-based Mazak MegaStir, the VTC-300C FSW adds advanced additive, joining and gear-cutting technologies to the multitasking capabilities found in Mazak machines.
The machine’s FSW package uses a process that involves frictional heat and forging pressure to create full-penetration, defect-free welded joints stronger than conventional methods. A solid-state joining process with a non-consumable tool pin, the Mazak FSW head joins two metal plates without melting the workpiece. Commonly considered a forging process, FSW is well-suited for joining alloys with low melting points.
MegaStir, which was acquired by Mazak in late 2018, has led the industry with improved FSW tool material innovation and applications since 2002. Mazak first collaborated with MegaStir on the full 5-axis VTC-800 FSW vertical machining center. The new Mazak MegaStir will continue to pursue further system advancements while providing technical
expertise as the future home of a full FSW technology center.
The FSW process is performed with a Mazak MegaStir-supplied instrumented toolholder equipped with a Bluetooth-enabled wireless sensor connection; a second toolholder or FSW tool pin is available as an option. The closed-loop FSW process utilizes integrated thrust and temperature sensors for constant thrust control and the ability to
perform manual thrust offsets during welding operations. The VTC-300C FSW comes equipped with robust HMI software designed for the quick and simple programming of plunge/traverse/extract operations, with all process data logged and stored.
The new welding technology complements the existing VTC-300C machine platform, which delivers a standard 15,000-rpm, 30-hp, 40-taper spindle capable of handling a wide variety of metalcutting applications. Additionally, the machine and waycover design has been enhanced to provide 1,574 ipm rapid feedrates on all axes. Its fixed 78.74" x
30" table provides process flexibility for a wide range of applications, while an optional center partition can divide the machine’s work envelope into two separate work zones to allow the machine to be in cycle in one area while loading, unloading or setting up a part in the other. The machine’s axis travels measure 65.35" in X, 30" in Y and 25.6" in Z.
The machine also features Mazak’s Mazatrol SmoothG CNC, which makes it easy to generate programs for the production of highly complex parts. It has several advanced functions that ensure the shortest possible machining cycle times, especially with fine-increment programs for free-form die/mold machining. These functions include
High-Gain Feed Forward Control, Fast Rotary Axis Speeds, Variable Acceleration Control and Intelligent Pocket Milling.
Ergonomics play an important role in the functionality of the Mazatrol SmoothG CNC. A large 19" display presents all of the critical machine data on a single screen, while the tilt control panel allows for optimal positioning based on operator height. An intuitive multitouch screen, which is similar to that of a smartphone, enables fast and
smooth programming operations. An SD card allows the CNC to store up to 32GB of data.
The VTC-300C FSW machine also seamlessly integrates with a variety of robotic loader solutions provided by Mazak Automation Systems, and its SmoothG control makes it easy to take advantage of machine monitoring software like Smooth Link and IIoT connectivity tools like MTConnect and the Mazak SmartBox.
Related Glossary Terms
- alloys
alloys
Substances having metallic properties and being composed of two or more chemical elements of which at least one is a metal.
- automatic toolchanger
automatic toolchanger
Mechanism typically included in a machining center that, on the appropriate command, removes one cutting tool from the spindle nose and replaces it with another. The changer restores the used tool to the magazine and selects and withdraws the next desired tool from the storage magazine. The changer is controlled by a set of prerecorded/predetermined instructions associated with the part(s) to be produced.
- centers
centers
Cone-shaped pins that support a workpiece by one or two ends during machining. The centers fit into holes drilled in the workpiece ends. Centers that turn with the workpiece are called “live” centers; those that do not are called “dead” centers.
- computer numerical control ( CNC)
computer numerical control ( CNC)
Microprocessor-based controller dedicated to a machine tool that permits the creation or modification of parts. Programmed numerical control activates the machine’s servos and spindle drives and controls the various machining operations. See DNC, direct numerical control; NC, numerical control.
- feed
feed
Rate of change of position of the tool as a whole, relative to the workpiece while cutting.
- gang cutting ( milling)
gang cutting ( milling)
Machining with several cutters mounted on a single arbor, generally for simultaneous cutting.
- inches per minute ( ipm)
inches per minute ( ipm)
Value that refers to how far the workpiece or cutter advances linearly in 1 minute, defined as: ipm = ipt 5 number of effective teeth 5 rpm. Also known as the table feed or machine feed.
- machining center
machining center
CNC machine tool capable of drilling, reaming, tapping, milling and boring. Normally comes with an automatic toolchanger. See automatic toolchanger.
- metalcutting ( material cutting)
metalcutting ( material cutting)
Any machining process used to part metal or other material or give a workpiece a new configuration. Conventionally applies to machining operations in which a cutting tool mechanically removes material in the form of chips; applies to any process in which metal or material is removed to create new shapes. See metalforming.
- milling
milling
Machining operation in which metal or other material is removed by applying power to a rotating cutter. In vertical milling, the cutting tool is mounted vertically on the spindle. In horizontal milling, the cutting tool is mounted horizontally, either directly on the spindle or on an arbor. Horizontal milling is further broken down into conventional milling, where the cutter rotates opposite the direction of feed, or “up” into the workpiece; and climb milling, where the cutter rotates in the direction of feed, or “down” into the workpiece. Milling operations include plane or surface milling, endmilling, facemilling, angle milling, form milling and profiling.
- toolchanger
toolchanger
Carriage or drum attached to a machining center that holds tools until needed; when a tool is needed, the toolchanger inserts the tool into the machine spindle. See automatic toolchanger.
- toolholder
toolholder
Secures a cutting tool during a machining operation. Basic types include block, cartridge, chuck, collet, fixed, modular, quick-change and rotating.
- work envelope
work envelope
Cube, sphere, cylinder or other physical space within which the cutting tool is capable of reaching.