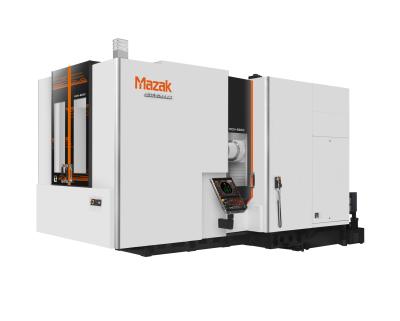
Mazak Corp.'s HCN-6800 is a heavy-duty horizontal machining center that combines advanced technology and value with a high level of performance and productivity for large-part machining. Equipped with the Mazatrol SmoothG CNC, the machine’s advanced programming features and functions offer ease of use, speed and further enhanced machine performance.
The HCN-6800 has a special integral spindle/motor headstock that minimizes vibration and heat generation. It comes with a robust 50-hp, 10,000-rpm, CAT 50 spindle that delivers exceptional metal-removal capabilities in a variety of materials, from steels to nonferrous metals. Optional high-speed, high-torque and hard-metal spindles are also
available to effectively tackle a wide range of application requirements. For greater versatility and fast, efficient part processing, the cam-driven automatic toolchanger (ATC) also reduces noncut times via fast, reliable 4.2-second chip-to-chip tool change cycles.
For positioning speed, even at high feed rates, the machine’s travels – measuring 41.34" in X, 35.43" in Y and 38.58" in Z – rapid traverse at 2,362 ipm per axis at 0.8G acceleration. Smooth high-gain servo and high-power AC servomotors allow for fast, vibration-free acceleration and deceleration rates.
The machine’s MazatrolL SmoothG CNC makes it easy to generate programs for processing large complex parts through off-centerline machining, as well as angled drilling, milling and tapping. The CNC is key to the company’s Smooth Technology platform, which spans the part-production landscape from programming and data collection to metal removal and specialized machining functions, and allows the machine to offer unmatched speed, functionality and ease of use.
The HCN-6800 comes standard with a two-pallet changer that allows an operator to load and unload parts on one pallet while the second pallet is active inside the machine. The machine’s pallet size is 24.8" x 24.8" with a maximum load capacity of 3,307 lbs. The twi-pallet changer also makes it possible for the HCN-6800 to be integrated with Mazak’s modular, pre-engineered Palletech system for continuous, high-volume parts production.
Contact Details
Related Glossary Terms
- automatic toolchanger
automatic toolchanger
Mechanism typically included in a machining center that, on the appropriate command, removes one cutting tool from the spindle nose and replaces it with another. The changer restores the used tool to the magazine and selects and withdraws the next desired tool from the storage magazine. The changer is controlled by a set of prerecorded/predetermined instructions associated with the part(s) to be produced.
- computer numerical control ( CNC)
computer numerical control ( CNC)
Microprocessor-based controller dedicated to a machine tool that permits the creation or modification of parts. Programmed numerical control activates the machine’s servos and spindle drives and controls the various machining operations. See DNC, direct numerical control; NC, numerical control.
- feed
feed
Rate of change of position of the tool as a whole, relative to the workpiece while cutting.
- gang cutting ( milling)
gang cutting ( milling)
Machining with several cutters mounted on a single arbor, generally for simultaneous cutting.
- inches per minute ( ipm)
inches per minute ( ipm)
Value that refers to how far the workpiece or cutter advances linearly in 1 minute, defined as: ipm = ipt 5 number of effective teeth 5 rpm. Also known as the table feed or machine feed.
- machining center
machining center
CNC machine tool capable of drilling, reaming, tapping, milling and boring. Normally comes with an automatic toolchanger. See automatic toolchanger.
- milling
milling
Machining operation in which metal or other material is removed by applying power to a rotating cutter. In vertical milling, the cutting tool is mounted vertically on the spindle. In horizontal milling, the cutting tool is mounted horizontally, either directly on the spindle or on an arbor. Horizontal milling is further broken down into conventional milling, where the cutter rotates opposite the direction of feed, or “up” into the workpiece; and climb milling, where the cutter rotates in the direction of feed, or “down” into the workpiece. Milling operations include plane or surface milling, endmilling, facemilling, angle milling, form milling and profiling.
- rapid traverse
rapid traverse
Movement on a CNC mill or lathe that is from point to point at full speed but, usually, without linear interpolation.
- tapping
tapping
Machining operation in which a tap, with teeth on its periphery, cuts internal threads in a predrilled hole having a smaller diameter than the tap diameter. Threads are formed by a combined rotary and axial-relative motion between tap and workpiece. See tap.
- toolchanger
toolchanger
Carriage or drum attached to a machining center that holds tools until needed; when a tool is needed, the toolchanger inserts the tool into the machine spindle. See automatic toolchanger.