Contact Details
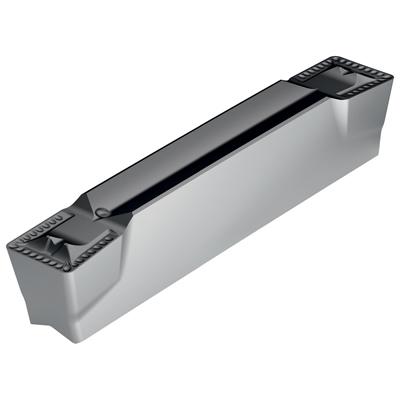
Walter USA LLC has introduced three new Walter Cut GX Tiger-tec Silver CVD grooving and parting grades, the WKP13S, WKP23S and WKP33S, which are being introduced in combination with Walter's provden geometries UD4, UA4, UF4, RD4 and the plunge grooving and parting geometries GD3 and CE4.
This advanced cutting tool combination is enhanced by the latest developments in Tiger-tec Silver technology, a wear-resistant cutting material that delivers an increase in cutting parameters, while maintaining or improving tool life, according to the company. The new, thicker Tiger-tec Silver CVD coating used with the WKP grades features aluminum oxide with optimized microstructure for maximum crater wear resistance, and enhanced cutting speed due, in part, to reduced friction. A new silver flank face permits easy wear detection and full cutting edge usage.
In addition, a second generation mechanical post-treatment is used to create compressive stresses, enhancing toughness, reducing the chance of cracks on the cutting edge and boosting load capability and metal removal rates. Additionally, the greater toughness produces longer and more consistent tool life.
The WKP13S is for use under good machining conditions, primarily on ISO P and ISO K materials including steels such as high grade, bearing and carbon steels. ISO K materials include gray cast iron and ductile iron, as well as compacted graphite cast iron. This grade reportedly delivers excellent wear resistance and cutting speed especially in continuous cuts. WKP23S, used primarily on ISO P and K materials, is a universal grade for a variety of applications, from continuous cutting on bar stock to machining interrupted cuts. It delivers superior wear resistance and cutting speed. WKP33S, also aimed at ISO P and K materials, provides excellent wear resistance and high toughness during unfavorable machining conditions.
Related Glossary Terms
- aluminum oxide
aluminum oxide
Aluminum oxide, also known as corundum, is used in grinding wheels. The chemical formula is Al2O3. Aluminum oxide is the base for ceramics, which are used in cutting tools for high-speed machining with light chip removal. Aluminum oxide is widely used as coating material applied to carbide substrates by chemical vapor deposition. Coated carbide inserts with Al2O3 layers withstand high cutting speeds, as well as abrasive and crater wear.
- carbon steels
carbon steels
Known as unalloyed steels and plain carbon steels. Contains, in addition to iron and carbon, manganese, phosphorus and sulfur. Characterized as low carbon, medium carbon, high carbon and free machining.
- chemical vapor deposition ( CVD)
chemical vapor deposition ( CVD)
High-temperature (1,000° C or higher), atmosphere-controlled process in which a chemical reaction is induced for the purpose of depositing a coating 2µm to 12µm thick on a tool’s surface. See coated tools; PVD, physical vapor deposition.
- cutting speed
cutting speed
Tangential velocity on the surface of the tool or workpiece at the cutting interface. The formula for cutting speed (sfm) is tool diameter 5 0.26 5 spindle speed (rpm). The formula for feed per tooth (fpt) is table feed (ipm)/number of flutes/spindle speed (rpm). The formula for spindle speed (rpm) is cutting speed (sfm) 5 3.82/tool diameter. The formula for table feed (ipm) is feed per tooth (ftp) 5 number of tool flutes 5 spindle speed (rpm).
- grooving
grooving
Machining grooves and shallow channels. Example: grooving ball-bearing raceways. Typically performed by tools that are capable of light cuts at high feed rates. Imparts high-quality finish.
- microstructure
microstructure
Structure of a metal as revealed by microscopic examination of the etched surface of a polished specimen.
- parting
parting
When used in lathe or screw-machine operations, this process separates a completed part from chuck-held or collet-fed stock by means of a very narrow, flat-end cutting, or parting, tool.
- wear resistance
wear resistance
Ability of the tool to withstand stresses that cause it to wear during cutting; an attribute linked to alloy composition, base material, thermal conditions, type of tooling and operation and other variables.