Contact Details
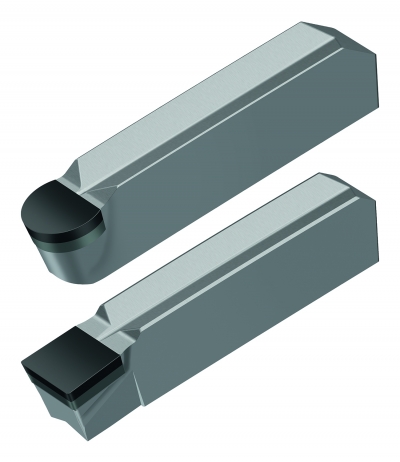
WBH20 and WBS10, part of the latest generation of CBN insert grades from Walter, deliver optimum surface quality, high process reliability, and extended tool life in grooving operations on the toughest materials. WBH20 is a grade well suited for ISO-H Group of material such as for hard turning applications. WBS10 is well suited for ISO-S materials, specifically nickel-based (such as Inconel), iron-based (such as Udimet) or cobalt-based (such as Hayens).
WBH20, with 50% CBN content and optimized grain structure, is wear-resistant at medium cutting speed. With a T-land of 0.008 in. x 20° it was developed to enable components of hard ISO H materials up to 65 HRC, to be grooved efficiently and with low wear during either smooth or interrupted cut. Typical areas of application include the automotive and agricultural equipment industry, but also general machining and energy.
WBS10 grade was developed for aerospace materials, specifically super alloys from ISO-S materials group. Among other tasks, it excels in grooving materials such as Inconel on engine components, and in the oil, gas and energy industries, as well as general mechanical engineering.
With its light hone and medium CBN content (65%) this grade is well suited for higher cutting speeds (800-980 sfm) in super alloys such as Inconel-718. Increased production capacity from the same machine to free up machine time, and highly cost-effective operation due to low unit costs are some additional benefits of this grade.
Related Glossary Terms
- alloys
alloys
Substances having metallic properties and being composed of two or more chemical elements of which at least one is a metal.
- cubic boron nitride ( CBN)
cubic boron nitride ( CBN)
Crystal manufactured from boron nitride under high pressure and temperature. Used to cut hard-to-machine ferrous and nickel-base materials up to 70 HRC. Second hardest material after diamond. See superabrasive tools.
- cutting speed
cutting speed
Tangential velocity on the surface of the tool or workpiece at the cutting interface. The formula for cutting speed (sfm) is tool diameter 5 0.26 5 spindle speed (rpm). The formula for feed per tooth (fpt) is table feed (ipm)/number of flutes/spindle speed (rpm). The formula for spindle speed (rpm) is cutting speed (sfm) 5 3.82/tool diameter. The formula for table feed (ipm) is feed per tooth (ftp) 5 number of tool flutes 5 spindle speed (rpm).
- grooving
grooving
Machining grooves and shallow channels. Example: grooving ball-bearing raceways. Typically performed by tools that are capable of light cuts at high feed rates. Imparts high-quality finish.
- hard turning
hard turning
Single-point cutting of a workpiece that has a hardness value higher than 45 HRC.
- interrupted cut
interrupted cut
Cutting tool repeatedly enters and exits the work. Subjects tool to shock loading, making tool toughness, impact strength and flexibility vital. Closely associated with milling operations. See shock loading.
- turning
turning
Workpiece is held in a chuck, mounted on a face plate or secured between centers and rotated while a cutting tool, normally a single-point tool, is fed into it along its periphery or across its end or face. Takes the form of straight turning (cutting along the periphery of the workpiece); taper turning (creating a taper); step turning (turning different-size diameters on the same work); chamfering (beveling an edge or shoulder); facing (cutting on an end); turning threads (usually external but can be internal); roughing (high-volume metal removal); and finishing (final light cuts). Performed on lathes, turning centers, chucking machines, automatic screw machines and similar machines.