Contact Details
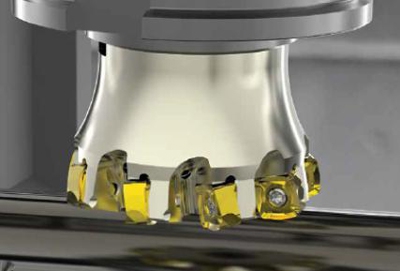
Late last year, Kennametal finalized its acquisition of the tungsten materials business from Allegheny Technologies Inc., including the full line of Stellram metalworking tools (formerly ATI Stellram). Now the full platform of Stellram products, with solutions specifically tailored to support energy, aerospace, transportation and other vital industries, are available as part of the Kennametal portfolio.
Driven by Kennametal's commitment to "Different Thinking is Better Thinking," the Stellram group of products include such production-enhancing milling technologies such as the 7792 and 7793 high-feed milling cutter systems and the 5230 Chevron long-edge mill cutter system, along with X-Grade carbide insert technology. High-performance materials such as titanium and other low-weight/high-strength alloys of particular interest to the aerospace industry are the materials of choice for these proprietary cutter designs, inserts, and grades.
The Stellram 7792 and 7793 milling cutters direct cutting forces axially into the spindle, lessening spindle wear and improving machining stability. Both modern and older equipment benefit from this cutting tool technology. These Stellram face mills operate at shallow depths of cut and very high feed rates, resulting in metal-removal rates up to 5 times greater than conventional cutters. In addition to high-feed face milling, the 7792 is capable of pocketing, slotting, and plunging.
High-feed milling nserts are available with proprietary Stellram X-Grade technology. X-Grade technology uses ruthenium as a key ingredient, combined with a cobalt binder, for superior thermal-cracking and propagation resistance. The results are metal-removal rates up to three times higher than conventional cutting tools and longer tool life.
X-Grade inserts are available in a variety of styles for a variety of applications. X-Grade inserts are also designed to yield the highest levels of material removal rates in high-performance materials like titanium as well as other difficult-to-machine alloys such as nickel-based alloys, cobalt-based alloys and titanium-based alloys used extensively in aerospace and energy Markets.
The Stellram 5230 Chevron long-edge milling series of inserts and cutters work together to provide substantial reductions in machining time for titanium and other high-strength alloys. The advanced chevron insert design ensures that one cutting point is always in contact with the work material during entrance and exit. Single-line contact on the cutter body means no two inserts are contacting the workpiece on the same axial plane. Together this provides optimum harmonic stability, reducing power consumption and maximizing tool life.
Additionally, threaded coolant ports on the cutter body allow selective blocking to adjust pressure and volume. Each insert has its own coolant jet for optimum chip evacuation.
Related Glossary Terms
- alloys
alloys
Substances having metallic properties and being composed of two or more chemical elements of which at least one is a metal.
- coolant
coolant
Fluid that reduces temperature buildup at the tool/workpiece interface during machining. Normally takes the form of a liquid such as soluble or chemical mixtures (semisynthetic, synthetic) but can be pressurized air or other gas. Because of water’s ability to absorb great quantities of heat, it is widely used as a coolant and vehicle for various cutting compounds, with the water-to-compound ratio varying with the machining task. See cutting fluid; semisynthetic cutting fluid; soluble-oil cutting fluid; synthetic cutting fluid.
- feed
feed
Rate of change of position of the tool as a whole, relative to the workpiece while cutting.
- gang cutting ( milling)
gang cutting ( milling)
Machining with several cutters mounted on a single arbor, generally for simultaneous cutting.
- metalworking
metalworking
Any manufacturing process in which metal is processed or machined such that the workpiece is given a new shape. Broadly defined, the term includes processes such as design and layout, heat-treating, material handling and inspection.
- milling
milling
Machining operation in which metal or other material is removed by applying power to a rotating cutter. In vertical milling, the cutting tool is mounted vertically on the spindle. In horizontal milling, the cutting tool is mounted horizontally, either directly on the spindle or on an arbor. Horizontal milling is further broken down into conventional milling, where the cutter rotates opposite the direction of feed, or “up” into the workpiece; and climb milling, where the cutter rotates in the direction of feed, or “down” into the workpiece. Milling operations include plane or surface milling, endmilling, facemilling, angle milling, form milling and profiling.
- milling cutter
milling cutter
Loosely, any milling tool. Horizontal cutters take the form of plain milling cutters, plain spiral-tooth cutters, helical cutters, side-milling cutters, staggered-tooth side-milling cutters, facemilling cutters, angular cutters, double-angle cutters, convex and concave form-milling cutters, straddle-sprocket cutters, spur-gear cutters, corner-rounding cutters and slitting saws. Vertical cutters use shank-mounted cutting tools, including endmills, T-slot cutters, Woodruff keyseat cutters and dovetail cutters; these may also be used on horizontal mills. See milling.
- milling machine ( mill)
milling machine ( mill)
Runs endmills and arbor-mounted milling cutters. Features include a head with a spindle that drives the cutters; a column, knee and table that provide motion in the three Cartesian axes; and a base that supports the components and houses the cutting-fluid pump and reservoir. The work is mounted on the table and fed into the rotating cutter or endmill to accomplish the milling steps; vertical milling machines also feed endmills into the work by means of a spindle-mounted quill. Models range from small manual machines to big bed-type and duplex mills. All take one of three basic forms: vertical, horizontal or convertible horizontal/vertical. Vertical machines may be knee-type (the table is mounted on a knee that can be elevated) or bed-type (the table is securely supported and only moves horizontally). In general, horizontal machines are bigger and more powerful, while vertical machines are lighter but more versatile and easier to set up and operate.
- slotting
slotting
Machining, normally milling, that creates slots, grooves and similar recesses in workpieces, including T-slots and dovetails.