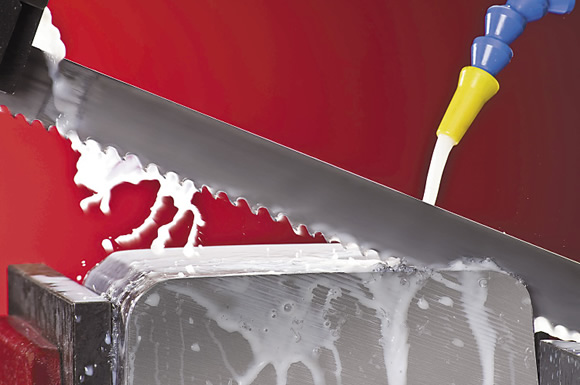
Courtesy of L.S. Starrett
L.S. Starrett’s Advanz TS carbide-tipped bandsaw blades resist wear even when cutting difficult-to-machine materials, such as Inconel, austenitic stainless steel and heat-treated steel.
Tips and techniques for improving bandsaw blade life and performance.
Similar to other cutting tools, bandsaw blades eventually wear—sometimes prematurely. While the easiest way to deal with early blade wear is to just replace the blade, it’s better to examine the possible causes, such as:
■ Incorrect speeds and feeds;
■ Improper or nonexistent break-in process;
■ Too few or too many teeth in the cut;
■ A worn chip brush;
■ Incorrect coolant flow or mixture;
■ Worn blade guides; and
■ Incorrect blade tension on the band.
“In a lot of facilities, sawing tends to be looked on as a simpler operation and is overlooked in the manufacturing process,” said Dave McCallen, North America sales manager–metal products for Simonds International, Fitchburg, Mass. “By paying more attention to the sawing operation—getting a better finish or a squarer cut—customers could possibly eliminate secondary operations. And [better sawing] could also help reduce material waste.”
Concern over tool life varies by user. For example, a big production saw house that runs 24/7 has different needs than a small job shop that uses its bandsaw machine intermittently.
“A 12 '- long, 1 "-wide bimetal bandsaw blade costs about $40,” said Gene Ramsdell, manager of North America saw R&D for The L.S. Starrett Co., Athol, Mass. “But a 25 '-long, 2 "-wide blade for a big production bandsaw machine could be $150 to $200. A 25/8 "-wide carbide-tipped blade can be $400 to $500. You can live with short life on a $40 blade, but not on a $200 one.”
Bimetal blades are, by far, the most common type of bandsaw blade used and are the most versatile for cutting various materials. These blades feature a thin strip of HSS welded to a wide strip of spring-steel backing material. The HSS offers effective cutting and the flexible backing resists fatigue, prolonging blade life.
Carbide-tipped bandsaw blades resist wear even when cutting difficult-to-machine materials. These blades also have a steel backing. Carbide-tipped blades do not need to be changed as frequently as bimetal blades, but cost more.
“Carbide-tipped blades are for users who want to cut faster and obtain a better surface finish, and they are very good on metals such as tool steel, stainless steel, titanium and nickel-base alloys,” said Matthew Lacroix, director of marketing for Lenox, East Longmeadow, Mass. However, these blades require a more rigid bandsaw machine to minimize vibration because carbide teeth are less forgiving than bimetal ones, he noted.
“Carbide-tipped blades don’t like a lot of vibration,” Lacroix said. “Although the teeth are harder, they can be fragile and so they don’t like high impacts. Carbide isn’t a great choice for thin-walled tube or pipes because of the excess vibration caused by the interrupted cut. That is one reason why bimetal blades are recommended more often for structural applications.”
Bandsaw blades made of carbon steel typically are used in nonferrous applications. “Carbon steel makes up a very small part of the metal sawing market,” Lacroix said. “The bulk of the market is bimetal with 75 percent, and carbide-tipped is about 20 percent.”
Watch the Speeds and Feeds
A good place to start preventing premature wear is by monitoring sawing parameters. Saw blade manufacturers provide guidelines for speeds and feed rates for an application to avoid problems.
“If your speed is too fast and your down-feed is insufficient, the bandsaw blade will rub the workpiece rather than dig into it,” Ramsdell said, adding that rubbing generates frictional heat and dulls the blade.
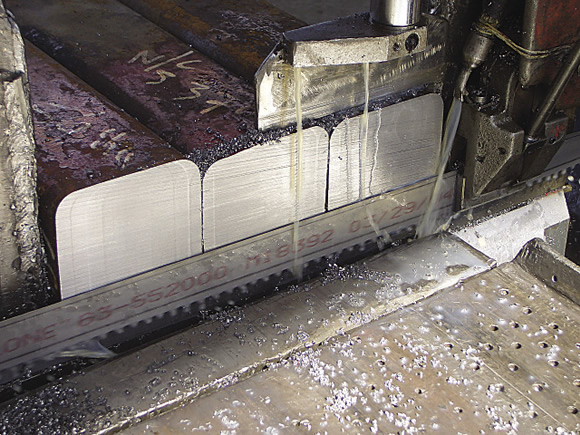
Courtesy of Simonds International
Simonds’ SiClone bimetal bandsaw blade is made for cutting materials prone to workhardening, such as stainless steel.
Running too slowly while cutting certain cross-sections (structurals) such as I- beams or H-beams can cause the teeth to contact a wall or surface too heavily and cause the teeth to chip, Ramsdell noted.
A too-low feed rate is a common error when cutting materials prone to workhardening, such as nickel-base alloys and austenitic stainless and tool steels. “You have to make sure you are constantly taking a chip and cutting under the area that could workharden,” Ramsdell said. Otherwise, the blade will workharden the material and wear prematurely.
Chip formation assists the user in determining if the speed and feed rate are appropriate. “A knowledgeable operator will know what to expect from the material they are cutting,” said Alan Peterson, global product manager for The M. K. Morse Co., Canton, Ohio. “Any deviation from the normal chip appearance will guide them in determining what type of adjustment they need to make. Small adjustments to the speed and feed can position the blade so it is cutting most effectively.”
Chips should be nicely curled “6s” and “9s” and silvery in color. This indicates correct feed pressure, cutting speed and tooth pitch selection. Chip formation is based on the workpiece material.
Chips that are thin like whiskers or powdery indicate the speed is too high and the feed rate is too low. The blade is taking little cuts rather than forming a full chip. (Powdery chips are acceptable when cutting certain cast irons and D-2 tool steel.)
Chips that are too thick and tightly coiled and discolored indicate excessive feed pressure and a too-low speed. “Blue chips mean heat and heat is not good,” Ramsdell said. “Overheating can cause the teeth and band to wear more quickly.”
Don’t Skip the Break-in
The blade break-in process is often compared to taking the sharp point off a pencil. Leaving the sharp point and pushing too hard will cause the point to break. “Starting the blade with less force allows the very sharp points to become honed and withstand the normal speeds and feed rates,” Peterson said.
According to Simonds’ McCallen, a proper blade break-in procedure requires reducing the feed rate by about half of what is normal for production mode, removing anywhere from 25 to 100 sq. in. of material, then gradually increasing the feed so to hone the edges of the teeth, he explained.
Generally, an incorrect break-in that doesn’t apply a high enough feed can cause problems when cutting workhardening materials, according to McCallen. “The blade will rub,” he said. “You still want to be sure you are creating some type of chip.”
Some saw blade manufacturers offer or are working on blades with honed tips to minimize the need for break-in and decrease the possibility of damaging the blade.
This will be a great help because some operators skip the break-in procedure. “Most users are aware of the need for break- in but not everyone does it for a number of reasons,” Lenox’s Lacroix said. “People that really measure blade performance can increase their productivity and cost savings by breaking in the blades to extend their life.”
Brush Your Teeth
Having the wrong number of teeth in the cut negatively impacts wear. The basic rule is to keep at least three and no more than 24 in the workpiece, with six to 12 teeth being optimal. Fewer than three teeth risks tooth strippage and more than 24 teeth risks strippage and gullet clogging.
“If you have too many teeth in the cut, it is hard for the teeth to penetrate because the down force is spread over so many tooth points and the teeth are going to rub,” Ramsdell said. “Also, your gullet capacity is minimized. The gullets will tend to fill up with chips and the teeth can’t penetrate anymore.”
Chip brushes remove chips from the gullets after they have gone through the cut. If the teeth reenter the cut with chips in the gullets, tooth strippage and chip welding are more likely to occur. The chip brush also prevents the blade from carrying chips into the machine, where they can cause damage.
Although the brush is a function of the bandsaw machine, the operator must make adjustments to the brush as it wears to ensure it stays in contact with the blade gullet area and removes the chips. “Sometimes we find customers with brushes so worn out they are not even making contact with the gullets,” McCallen said. “And it is such as an easy thing to change.”
Coolant also helps extend blade life. A proper coolant flow and coolant mixture reduces the amount of heat—a blade’s worst enemy—in the cut. “In general, flood coolant that flows into the actual tooth contact area is preferred,” Ramsdell said. “The coolant manufacturer can fine tune the coolant mix, but a 10 percent concentration is typically a good starting point.”
The Right Guide
Blade guides play an important role in a bandsaw machine. Blade guides support the blade and hold it in place as it passes through the workpiece so it will not run off the drive and idler wheels, which move the blade. Regardless of whether the guide is a solid-carbide block or roller, all guides undergo wear-causing friction and require replacement.
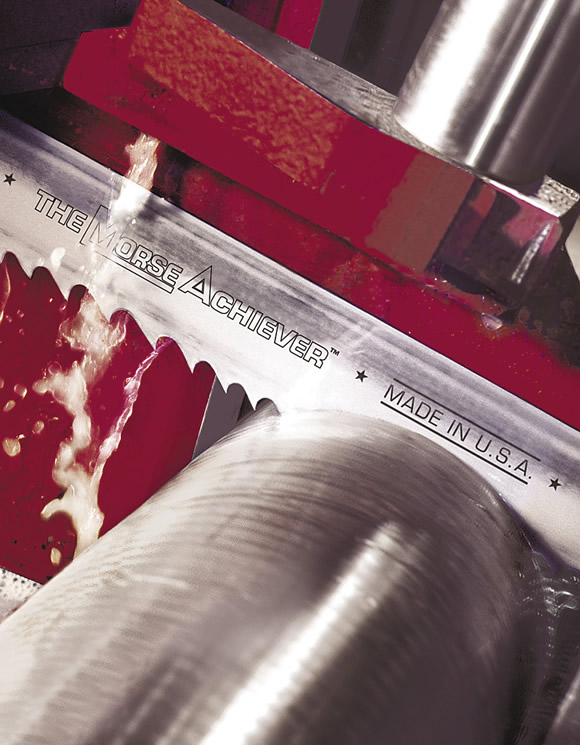
Courtesy of M. K. Morse
The Morse Achiever bimetal bandsaw is for cutting a range of solids, from carbon steel to stainless steel (shown).
Often, an out-of-square cut means the blade guides are starting to wear, McCallen noted. “If the back guides are completely worn, you could start to get cracks in the back edge of the band, which can cause fatigue and eventually blade breakage.”
Fractures on the back edge of the band can also occur when the blade rubs the wheel flange. “It comes down to how the blade is tracking in the idler and drive wheels,” McCallen said. “Adjustments to the machine have to be made at that point.”
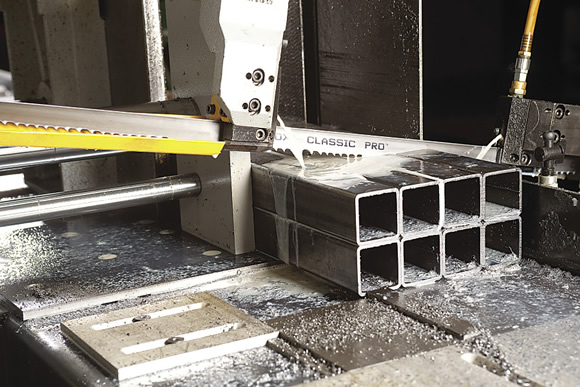
Courtesy of Lenox
Lenox’s Classic Pro bimetal bandsaw blades can cut a range of solids and structurals, from carbon steel to higher strength alloys.
It is also important that the blade guide gap matches the blade thickness to prevent excess movement during use. “It is critical that the guide arms are placed as close to the workpiece as possible to minimize twisting stresses on the blade,” Ramsdell said. “This also prevents blade deflection. If the arms are too far apart, one side of the blade tends to wear more.”
Cut the Tension
Improper blade tension can affect blade wear, to some extent. With the correct blade tension, the blade will cut straight. “If the blade tension is too low, the blade may wander a bit,” Ramsdell said. “If the tension is too high, the blade will still cut but blade life decreases due to fatigue.”
Generally, bimetal and carbide-tipped blades work best at a blade tension of around 30,000 psi, he added. It could be slightly higher, say, 40,000 psi, on wider blades, such as those 2 " to 3 " wide.
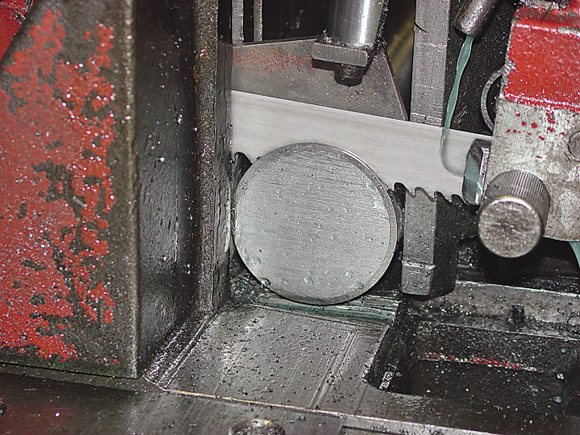
Courtesy of L.S. Starrett
L.S. Starrett says its AdvanzCS carbide-tipped bandsaw blades allow for fast cutting, impart a fine surface finish and cut hard materials, such as metals casehardened to 65 HRC.
Most automated bandsaw machines have hydraulic tensioning systems. Older machines and pull-down machines have manual hand tensioning and it is important that the operator is turning the tension knob correctly and using a tension gage to check final blade tension.
Although there are many causes of premature blade wear, “the largest single variable is the operator,” said M. K. Morse’s Peterson. “How well that person is trained on operating the bandsaw machine and the material being cut can determine the success of a cutting operation.”
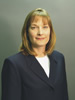
Simonds’ McCallen agreed that operator education is key, but is often lacking. “Shops don’t always realize there are a lot of variables that can affect a bandsaw blade running properly or poorly. With proper education and training, the operator can make adjustments during operation because he understands the cause and effect of these variables.” CTE
About the Author: Susan Woods is a contributing editor for CTE. Contact her at (224) 225-6120 or [email protected].
Making the most of bandsaw blades
Although preventing premature wear is the ultimate goal when maximizing bandsaw blade life, there is another option—resharpening.
Vollmer of America Corp., Carnegie, Pa., offers machines for resharpening bandsaw blades and circular saw blades, as well as for producing new blades.
Almost any blade can be resharpened, whether it is carbide-tipped, bimetal or carbon steel. The question is whether it is economically feasible to remove the blade before it is completely worn.
The general thought in the industry is that while circular saw blades can be resharpened, bandsaw blades should not be. “One of the biggest problems in the U.S. for us is that mindset of having to just use the bandsaw blade up each time no matter what,” said Shannon Fox, manager of sawing technology for Vollmer. “The blade is typically used to the point where it’s too late to be resharpened. The teeth are broken off or too worn down or the backs of the teeth are cracked.”
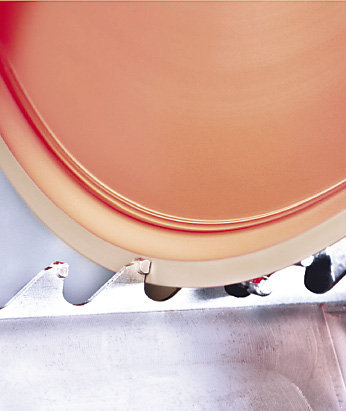
Courtesy of Vollmer of America
Face grinding a carbide-tipped bandsaw blade using a diamond grinding wheel on the Vollmer CB200.
Instead of running the bandsaw blade to 100 percent of its life, Fox said, if the operator removed it at the first signs that it was beginning to dull and then resharpened it, in many cases he could expect to see at least an additional 50 percent of life out of the blade. For example, Vollmer has found bimetal blades have, on average, lasted an additional 2/3 to ¾ of the original life after resharpening.
Fox noted that according to his colleagues in Germany, Vollmer sees a lot more bandsaw blade resharpening in Europe than in the U.S.
So how does the operator know when the bandsaw blade is beginning to dull? “A sharp blade at the proper feeds and speeds will produce a C-shaped chip without color,” Fox said. “Blue chips or flakes instead of the C-shape would be a good indicator it is time to resharpen the blade. Take it off while there is some tooth left to resharpen.”
A machine for resharpening bandsaw blades needs to be versatile. Carbide-tipped blades require a diamond wheel for grinding; bimetal and carbon steel blades typically are sharpened with a CBN wheel. According to Fox, due to the variety of bandsaw blades available, the machine should cover the common blade lengths of up to at least 18 ' and widths from 3/8 " to 3 ", in addition to a multitude of tooth pitches and shapes.
Although Vollmer offers a machine that can be used to sharpen bandsaw and circular blades for the wood industry, Fox recommends separate machines for resharpening bandsaw and circular blades for cutting metal.
“The geometries on metalcutting teeth often require a high-tech CNC machine that allows you to accurately recreate those shapes,” Fox said.
More people sharpen their circular saw blades because of the cost, according to Fox. Circular blades produce a very smooth, clean cut. But because the circular blade cannot flex like a bandsaw blade, there is more chance of breakage or deflection. A bandsaw blade tends to “wave” a bit so it doesn’t produce as accurate a cut as a circular blade, but there is also less chance of breakage.
“The capability to resharpen circular saw blades is pretty well known,” Fox said. “People need to now consider stopping those bandsaw blades before they are dead and get more life out of them.”
—S. Woods
Contributors
Lenox
(800) 628-3030
www.lenoxtools.com
The L.S. Starrett Co.
(978) 249-3551
www.starrett.com
The M. K. Morse Co.
(800) 733-3377
www.mkmorse.com
Simonds International
(800) 343-1616
www.simondsinternational.com
Vollmer of America Corp.
(412) 278-0655
www.vollmer-us.com
SaveSave
Related Glossary Terms
- alloys
alloys
Substances having metallic properties and being composed of two or more chemical elements of which at least one is a metal.
- backing
backing
1. Flexible portion of a bandsaw blade. 2. Support material behind the cutting edge of a tool. 3. Base material for coated abrasives.
- bandsaw
bandsaw
Machine that utilizes an endless band, normally with serrated teeth, for cutoff or contour sawing. See saw, sawing machine.
- bandsaw blade ( band)
bandsaw blade ( band)
Endless band, normally with serrated teeth, that serves as the cutting tool for cutoff or contour band machines.
- bandsaw blade ( band)2
bandsaw blade ( band)
Endless band, normally with serrated teeth, that serves as the cutting tool for cutoff or contour band machines.
- cast irons
cast irons
Cast ferrous alloys containing carbon in excess of solubility in austenite that exists in the alloy at the eutectic temperature. Cast irons include gray cast iron, white cast iron, malleable cast iron and ductile, or nodular, cast iron. The word “cast” is often left out.
- circular saw
circular saw
Cutoff machine utilizing a circular blade with serrated teeth. See saw, sawing machine.
- computer numerical control ( CNC)
computer numerical control ( CNC)
Microprocessor-based controller dedicated to a machine tool that permits the creation or modification of parts. Programmed numerical control activates the machine’s servos and spindle drives and controls the various machining operations. See DNC, direct numerical control; NC, numerical control.
- coolant
coolant
Fluid that reduces temperature buildup at the tool/workpiece interface during machining. Normally takes the form of a liquid such as soluble or chemical mixtures (semisynthetic, synthetic) but can be pressurized air or other gas. Because of water’s ability to absorb great quantities of heat, it is widely used as a coolant and vehicle for various cutting compounds, with the water-to-compound ratio varying with the machining task. See cutting fluid; semisynthetic cutting fluid; soluble-oil cutting fluid; synthetic cutting fluid.
- cubic boron nitride ( CBN)
cubic boron nitride ( CBN)
Crystal manufactured from boron nitride under high pressure and temperature. Used to cut hard-to-machine ferrous and nickel-base materials up to 70 HRC. Second hardest material after diamond. See superabrasive tools.
- cutting speed
cutting speed
Tangential velocity on the surface of the tool or workpiece at the cutting interface. The formula for cutting speed (sfm) is tool diameter 5 0.26 5 spindle speed (rpm). The formula for feed per tooth (fpt) is table feed (ipm)/number of flutes/spindle speed (rpm). The formula for spindle speed (rpm) is cutting speed (sfm) 5 3.82/tool diameter. The formula for table feed (ipm) is feed per tooth (ftp) 5 number of tool flutes 5 spindle speed (rpm).
- fatigue
fatigue
Phenomenon leading to fracture under repeated or fluctuating stresses having a maximum value less than the tensile strength of the material. Fatigue fractures are progressive, beginning as minute cracks that grow under the action of the fluctuating stress.
- feed
feed
Rate of change of position of the tool as a whole, relative to the workpiece while cutting.
- grinding
grinding
Machining operation in which material is removed from the workpiece by a powered abrasive wheel, stone, belt, paste, sheet, compound, slurry, etc. Takes various forms: surface grinding (creates flat and/or squared surfaces); cylindrical grinding (for external cylindrical and tapered shapes, fillets, undercuts, etc.); centerless grinding; chamfering; thread and form grinding; tool and cutter grinding; offhand grinding; lapping and polishing (grinding with extremely fine grits to create ultrasmooth surfaces); honing; and disc grinding.
- grinding wheel
grinding wheel
Wheel formed from abrasive material mixed in a suitable matrix. Takes a variety of shapes but falls into two basic categories: one that cuts on its periphery, as in reciprocating grinding, and one that cuts on its side or face, as in tool and cutter grinding.
- high-speed steels ( HSS)
high-speed steels ( HSS)
Available in two major types: tungsten high-speed steels (designated by letter T having tungsten as the principal alloying element) and molybdenum high-speed steels (designated by letter M having molybdenum as the principal alloying element). The type T high-speed steels containing cobalt have higher wear resistance and greater red (hot) hardness, withstanding cutting temperature up to 1,100º F (590º C). The type T steels are used to fabricate metalcutting tools (milling cutters, drills, reamers and taps), woodworking tools, various types of punches and dies, ball and roller bearings. The type M steels are used for cutting tools and various types of dies.
- interrupted cut
interrupted cut
Cutting tool repeatedly enters and exits the work. Subjects tool to shock loading, making tool toughness, impact strength and flexibility vital. Closely associated with milling operations. See shock loading.
- metalcutting ( material cutting)
metalcutting ( material cutting)
Any machining process used to part metal or other material or give a workpiece a new configuration. Conventionally applies to machining operations in which a cutting tool mechanically removes material in the form of chips; applies to any process in which metal or material is removed to create new shapes. See metalforming.
- pitch
pitch
1. On a saw blade, the number of teeth per inch. 2. In threading, the number of threads per inch.
- sawing
sawing
Machining operation in which a powered machine, usually equipped with a blade having milled or ground teeth, is used to part material (cutoff) or give it a new shape (contour bandsawing, band machining). Four basic types of sawing operations are: hacksawing (power or manual operation in which the blade moves back and forth through the work, cutting on one of the strokes); cold or circular sawing (a rotating, circular, toothed blade parts the material much as a workshop table saw or radial-arm saw cuts wood); bandsawing (a flexible, toothed blade rides on wheels under tension and is guided through the work); and abrasive sawing (abrasive points attached to a fiber or metal backing part stock, could be considered a grinding operation).
- sawing machine ( saw)
sawing machine ( saw)
Machine designed to use a serrated-tooth blade to cut metal or other material. Comes in a wide variety of styles but takes one of four basic forms: hacksaw (a simple, rugged machine that uses a reciprocating motion to part metal or other material); cold or circular saw (powers a circular blade that cuts structural materials); bandsaw (runs an endless band; the two basic types are cutoff and contour band machines, which cut intricate contours and shapes); and abrasive cutoff saw (similar in appearance to the cold saw, but uses an abrasive disc that rotates at high speeds rather than a blade with serrated teeth).
- tool steels
tool steels
Group of alloy steels which, after proper heat treatment, provide the combination of properties required for cutting tool and die applications. The American Iron and Steel Institute divides tool steels into six major categories: water hardening, shock resisting, cold work, hot work, special purpose and high speed.
- turning
turning
Workpiece is held in a chuck, mounted on a face plate or secured between centers and rotated while a cutting tool, normally a single-point tool, is fed into it along its periphery or across its end or face. Takes the form of straight turning (cutting along the periphery of the workpiece); taper turning (creating a taper); step turning (turning different-size diameters on the same work); chamfering (beveling an edge or shoulder); facing (cutting on an end); turning threads (usually external but can be internal); roughing (high-volume metal removal); and finishing (final light cuts). Performed on lathes, turning centers, chucking machines, automatic screw machines and similar machines.
- wheel flange
wheel flange
Metal plate inside the grinding-wheel hole that allows the wheel to be mounted on a spindle.
- workhardening
workhardening
Tendency of all metals to become harder when they are machined or subjected to other stresses and strains. This trait is particularly pronounced in soft, low-carbon steel or alloys containing nickel and manganese—nonmagnetic stainless steel, high-manganese steel and the superalloys Inconel and Monel.