You probably know that boring tools are used to bring holes to the desired size and finish, straighten drilled and cored holes and correct casting defects. But you may not know what to do — and what not to do — to get longer life and better performance out of boring tools, as well as improve the user experience. This knowledge falls into three categories: tool selection, best practices when using the tools, and developments that have had a positive impact on boring tools and processes.
When it comes to selecting the best boring tool for an application, some users are knowledgeable enough about the subject to request tools with specific
features and characteristics. For example, Scientific Cutting Tools Inc. in Simi Valley, California, normally makes boring tools with a 2-degree front angle across the face that facilitates efficient cutting, said Sales Director Todd White.
In some cases, however, “customers want to change that angle, so we make special tools for them based on their preferences and R&D that they have done,” he said. “For one customer, we make the front angle 8 degrees instead of 2 degrees because they find that works better for the materials that they cut.”
Good Guidance
Although some shops know enough about boring tools to make specific requests of suppliers, the majority rely to some extent on recommendations from toolmakers.
“Most of the time, when customers are looking at a finishing operation, they want a little bit of guidance,” said Natalie Wise, manager for finishing products at Allied Machine & Engineering Corp. in Dover, Ohio. The reason, she explained, is that “those are later operations in the manufacturing of their part, so it’s very critical that they get it right the first time. If something goes wrong with those finishing operations, they could be scrapping something very expensive that they’ve spent a lot of time on.”
To come up with the right boring tool for a particular application, White asks customers for basic information, such as the hole diameter, machining speeds and feeds and the part material. If the material is hard and abrasive, Scientific Cutting Tools can supply diamond- or CBN-tipped boring bars. Sometimes, however, he reports that customers dealing with such materials may start with conventional solid-carbide boring bars rather than pay extra for diamond- or CBN-tipped tools.
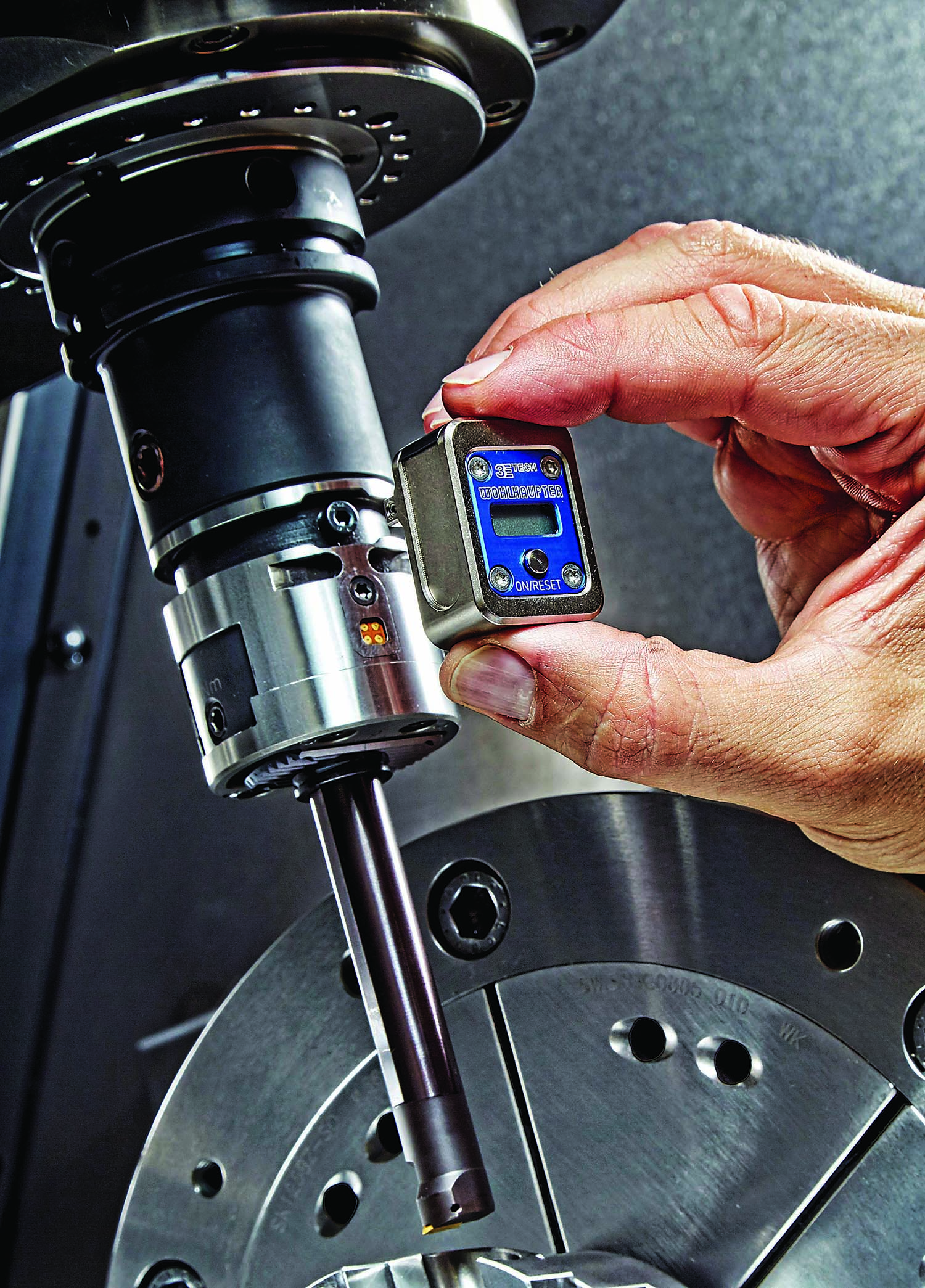
“Then if they’re using them up too fast, they’ll call and I’ll say, ‘You should probably bite the bullet and get a diamond-tipped bar for those materials because they’ll last a long time,’” he said. “Even though they’re quite a bit more expensive, the (number of) parts you get out of them can be phenomenal.”
White said machine shops cutting very abrasive nonferrous materials might get through 5,000 parts with a diamond-tipped boring bar compared with 10 or 15 with a solid-carbide bar.
So even though a solid-carbide bar costs $25 and a diamond-tip option costs $150, “your cost per piece is going to be way less,” he said.
The same is true, White added, of CBN-tipped bars, which are suitable for boring hardened steel.
Once again, in these applications “a lot of people will start out with coated carbide, and if they have a short run, that will get them through and give them a good finish,” he said. “But if the volume is high, then CBN is something to look at.”
In some cases, White pointed out that price considerations lead shops to the least expensive option: an uncoated boring tool. But when those customers cut metals like stainless steel and Inconel, Scientific Cutting Tools urges them to think longer term and opt for a coated tool. He reports that his company has had “great success” with a high-performance AlTiSiN coating called nACo, which provides excellent wear resistance and lubricity.
“I know it’s a couple dollars more,” he said, “but it can make a huge difference.”
Going Deep
Another key factor that comes into play when choosing a boring tool is the ratio of hole depth to diameter. If that number is high, Scientific Cutting Tools can provide boring bars with a helical flute, White said, which minimizes deflection during the boring process.
For boring applications with depth-to-diameter ratios greater than 5-1, Allied Machine & Engineering offers Novitech, a mounted module that reduces vibration when machining hole diameters. Wise said this improves the surface finish of bored holes and increases tool life.
“The boring head is going to last a lot longer because it’s not vibrating,” she said, “so there’s not a lot of radial deflection or pressure.”
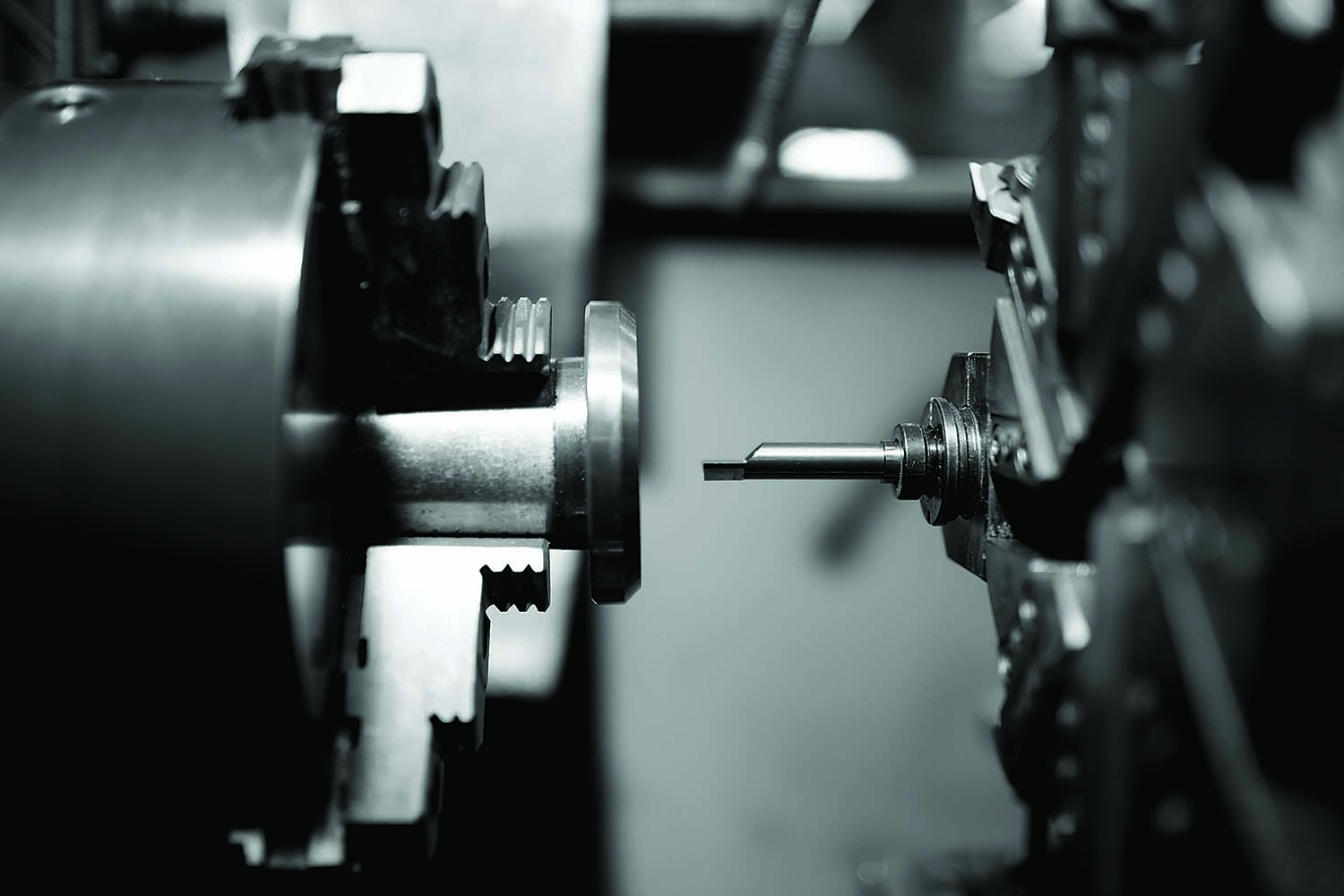
Wise said Novitech also extends the life of machine spindles.
“When you have excessive vibration, it’s really hard on the customer’s machine as well,” she said. “So it’s a win-win when you include some type of vibration-reducing technology.”
On the downside, additional features, such as Novitech, increase the cost of boring operations.
But while shops always are concerned about price, “when customers come to us with a very
important operation like finishing, it’s more important that the tool does what we say it’s going to do,” Wise said, as long as the extra cost is “within reason.”
Best Practices
Once a boring tool has been acquired for a particular application, users should be aware of practices that will help get the most out of that tool. For example, Wise recommends that users make sure they’re removing enough material when boring to completely cover the nose radius of the insert. If this isn’t the case, she said, radial deflection or pressure will cause chatter, which in turn results in poor hole quality or surface finish.
In situations like this, she said shops can do two things. One is to make the pre-drill hole size a little smaller so more material is left for the finishing operation. If this can’t be done, the other option is to swap out the tool insert for one with a smaller nose radius while leaving everything else in the boring tool setup the same.
Other best practices when using boring tools involve coolant-related issues. For one thing, it’s advisable to keep boring coolant clean.
“If you’re running nasty, dirty coolant through the tool,” Wise said, “it’s going to get into internal components and start wearing them down more quickly.”
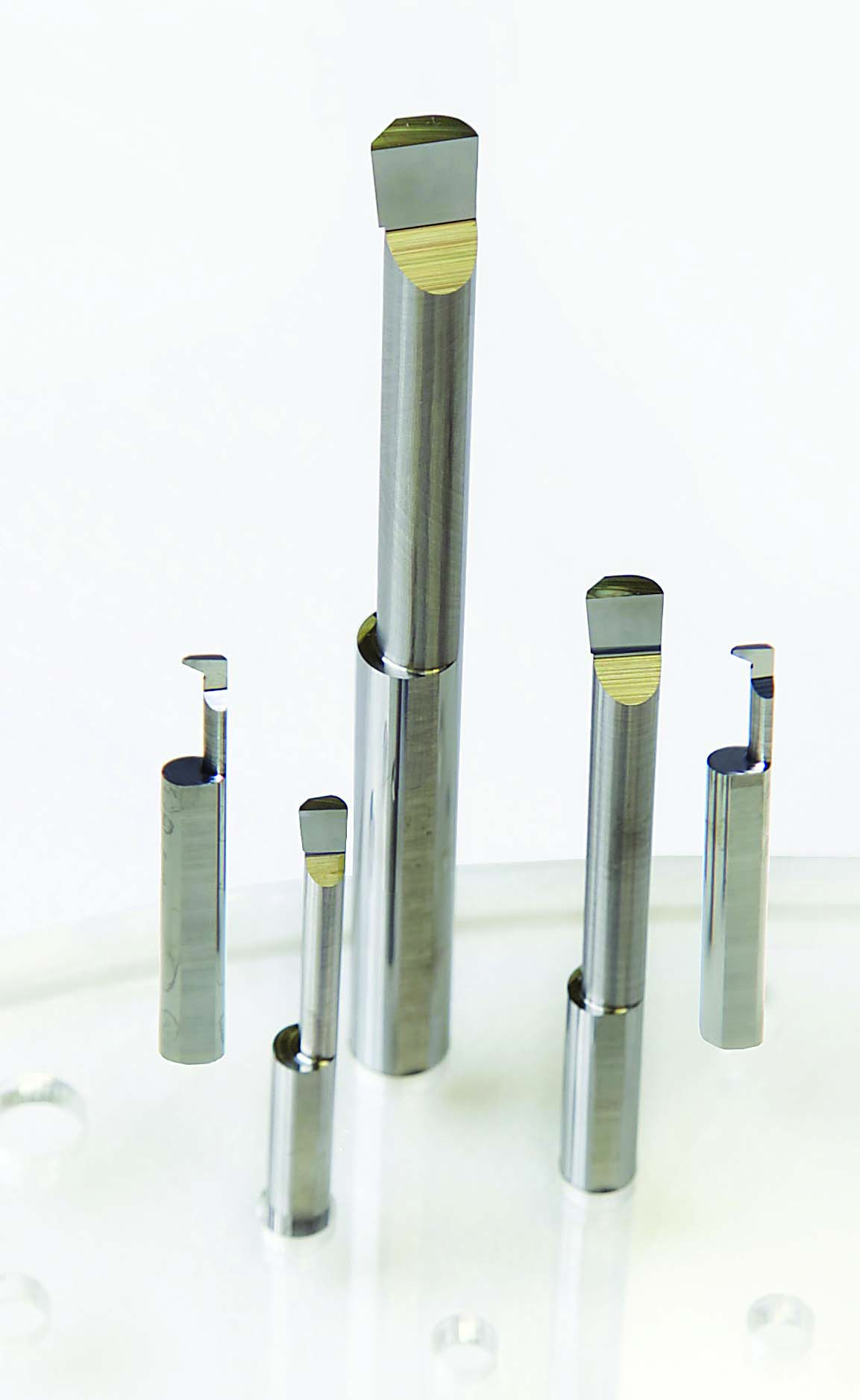
This is especially true when tools contain digital components.
“We need to have seals in place to protect the digital components,” said Wise, whose company makes such tools. “But really nasty coolant can eat up those seals and completely damage those components.”
She added that digital components also can be damaged by high coolant pressures, so she recommends limiting these pressures to 500 psi.
Another coolant-related problem can arise during the use of CBN-tipped boring bars. White said CBN is hard but also brittle, so big temperature swings can crack the material. To prevent this, there can be no interruption of coolant delivery to the tool during a boring process.
If constant coolant flow to the tool can’t be guaranteed, however, another option is to cut dry.
This works because CBN “can take a lot of heat, but it can’t take the big thermal change from hot to cold,” White said. “So as some people move toward dry machining, they’ll just shoot air through their lines to help with the chips. But that (prevents) that thermal up-and-down condition that can crack CBN.”
Boring Boost
Due to its importance during boring and other cutting operations, better coolant delivery has been a focus of Scientific Cutting Tools.
“In small-diameter boring with certain materials like 1018 steel, 316 stainless and 304 stainless, you can get really stringy chips,” White said. “So if you can get that coolant right to the cutting edge and keep it flowing, it could be really beneficial.”
He explained that stringy chips made of these materials can accumulate in blind holes where they are re-cut by the tool and often end up damaging the cutting edge.
“So a key is to get the chips out of there so you can ensure a good finish and not have any interference with the cutting edge,” White said.
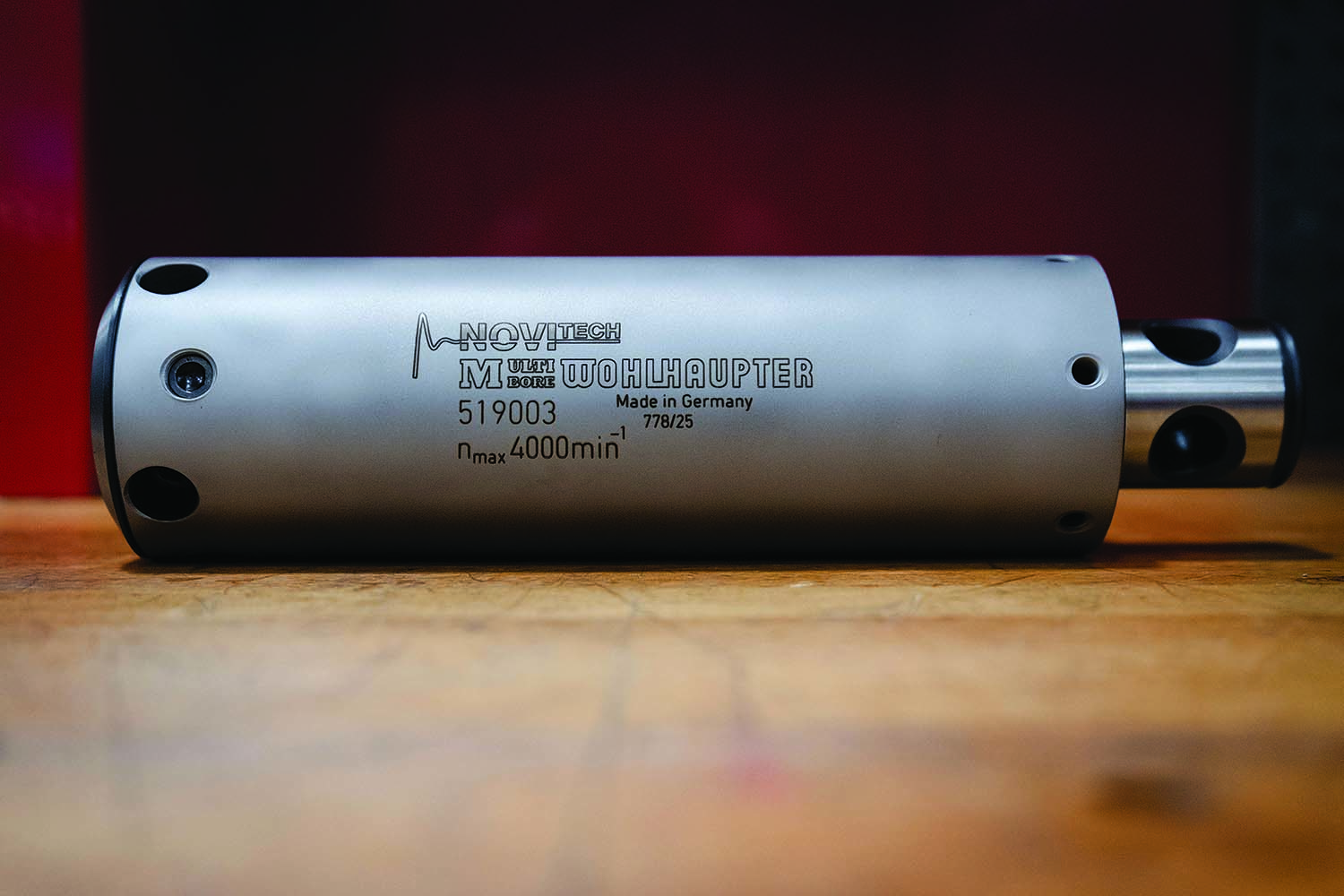
To improve coolant delivery, Scientific Cutting Tools has developed a toolholder featuring a ring around the tool shank. Instead of just directing coolant to a point at the tip of the tool, he said this ring produces a coolant “halo” that surrounds the entire tool.
In addition to coolant delivery advances coming from toolmakers, White stressed the importance of the high-pressure coolant capabilities of current machines. Today, he pointed out that many machines are equipped with pumps that can produce coolant pressures ranging from 300 to 1,000 psi, which is a big help to tools and toolholders designed to get coolant to places where it will be most helpful.
Coolant delivery advances aren’t the only ones boosting boring operations. Allied Machine & Engineering, for example, has come up with boring tools that have a self-balancing feature. This automatic mass balancing is meant to compensate for imbalances that occur as the diameter of a boring tool’s insert holder is adjusted. The idea is to reduce vibration in order to optimize finish machining.
In addition, Wise said her company’s digital technology makes it easier for operators to use boring tools.
These tools can require “a good deal of technical knowledge to set up, run and make those final finishing adjustments,” she said. “So we (offer) digital adjustment instead of an analog vernier scale.”
For boring operations, Allied Machine & Engineering provides two digital tooling options. One is a tool with a built-in digital component: a display fixed to the boring tool. As a user adjusts the tool’s finished diameter setting, the adjustments are shown on the display, Wise
explained.
The other digital option is the company’s 3E Tech display, a small module that can be mounted on a boring tool for diameter adjustment.
“When you’re done making the adjustment,” Wise said, “you just take that digital module off the boring head and you’re ready to go.”
Whatever form it takes, she said this type of technology seems to be a hit with tool users.
“Some people that are newer to the industry don’t even know how to read a vernier scale,” Wise said. “So digital adjustment is becoming a lot more common.”
Contact Details
Contact Details
Related Glossary Terms
- abrasive
abrasive
Substance used for grinding, honing, lapping, superfinishing and polishing. Examples include garnet, emery, corundum, silicon carbide, cubic boron nitride and diamond in various grit sizes.
- boring
boring
Enlarging a hole that already has been drilled or cored. Generally, it is an operation of truing the previously drilled hole with a single-point, lathe-type tool. Boring is essentially internal turning, in that usually a single-point cutting tool forms the internal shape. Some tools are available with two cutting edges to balance cutting forces.
- boring bar
boring bar
Essentially a cantilever beam that holds one or more cutting tools in position during a boring operation. Can be held stationary and moved axially while the workpiece revolves around it, or revolved and moved axially while the workpiece is held stationary, or a combination of these actions. Installed on milling, drilling and boring machines, as well as lathes and machining centers.
- boring head
boring head
Single- or multiple-point precision tool used to bring an existing hole within dimensional tolerance. The head attaches to a standard toolholder and a mechanism permits fine adjustments to be made to the head within a diameter range.
- chatter
chatter
Condition of vibration involving the machine, workpiece and cutting tool. Once this condition arises, it is often self-sustaining until the problem is corrected. Chatter can be identified when lines or grooves appear at regular intervals in the workpiece. These lines or grooves are caused by the teeth of the cutter as they vibrate in and out of the workpiece and their spacing depends on the frequency of vibration.
- coolant
coolant
Fluid that reduces temperature buildup at the tool/workpiece interface during machining. Normally takes the form of a liquid such as soluble or chemical mixtures (semisynthetic, synthetic) but can be pressurized air or other gas. Because of water’s ability to absorb great quantities of heat, it is widely used as a coolant and vehicle for various cutting compounds, with the water-to-compound ratio varying with the machining task. See cutting fluid; semisynthetic cutting fluid; soluble-oil cutting fluid; synthetic cutting fluid.
- cubic boron nitride ( CBN)
cubic boron nitride ( CBN)
Crystal manufactured from boron nitride under high pressure and temperature. Used to cut hard-to-machine ferrous and nickel-base materials up to 70 HRC. Second hardest material after diamond. See superabrasive tools.
- lubricity
lubricity
Measure of the relative efficiency with which a cutting fluid or lubricant reduces friction between surfaces.
- shank
shank
Main body of a tool; the portion of a drill or similar end-held tool that fits into a collet, chuck or similar mounting device.
- toolholder
toolholder
Secures a cutting tool during a machining operation. Basic types include block, cartridge, chuck, collet, fixed, modular, quick-change and rotating.
- wear resistance
wear resistance
Ability of the tool to withstand stresses that cause it to wear during cutting; an attribute linked to alloy composition, base material, thermal conditions, type of tooling and operation and other variables.
Contributors
Allied Machine & Engineering Corp.
330-343-4283
www.alliedmachine.com
Scientific Cutting Tools Inc.
805-584-9495
www.sct-usa.com