By Rigibore Inc.
Advances in modern manufacturing are at the core of industrial production. Technological innovation is occurring at a fast pace with increasing pressure to achieve perfection in the manufacture of components. The goals are improved productivity, efficiency, speed and quality, resulting in higher competitiveness for companies as they embrace Industry 4.0 and digital manufacturing.
In the past decade, a variety of innovative methods have been developed that allow manufacturing processes to be more versatile, less energy-consuming and more environmentally friendly.
One area in which this is very visible is machine tool solutions. Today’s components must be produced with exceptional accuracy while meeting critical lead times. Cutting tool selection can make or break efficiency for many manufacturers.
Boring operations are equally as stringent. Organizations need bores to be machined with micron-level accuracy, meeting and maintaining crucial tolerances in both low- and high-volume manufacturing operations.
New digital solutions for boring and machine tool systems are set to transform industrial production. Through Internet of Things technology, machines can communicate seamlessly with each other, sharing valuable real-time data and analytics with users. The enhancement of high-precision manufacturing by these smart technological systems enables lower error rates and fewer product failures, thus reducing huge costs historically faced by manufacturers. This is particularly critical for applications with high volumes and high accuracy requirements, such as in aerospace, automotive and heavy industry, for which parts that demand total accuracy are very expensive to scrap.
By adopting automated systems, production becomes more smooth, robust and visual, from planning all the way to actual operations, allowing people to work smarter, not harder.
We all know that automation helps businesses reduce production costs and in turn increase profits. The reason is that automation improves accuracy in the process, permitting repeatable production of identical parts. Furthermore, when a production process is automated, the need for downtime when operators take a break is almost entirely eliminated.
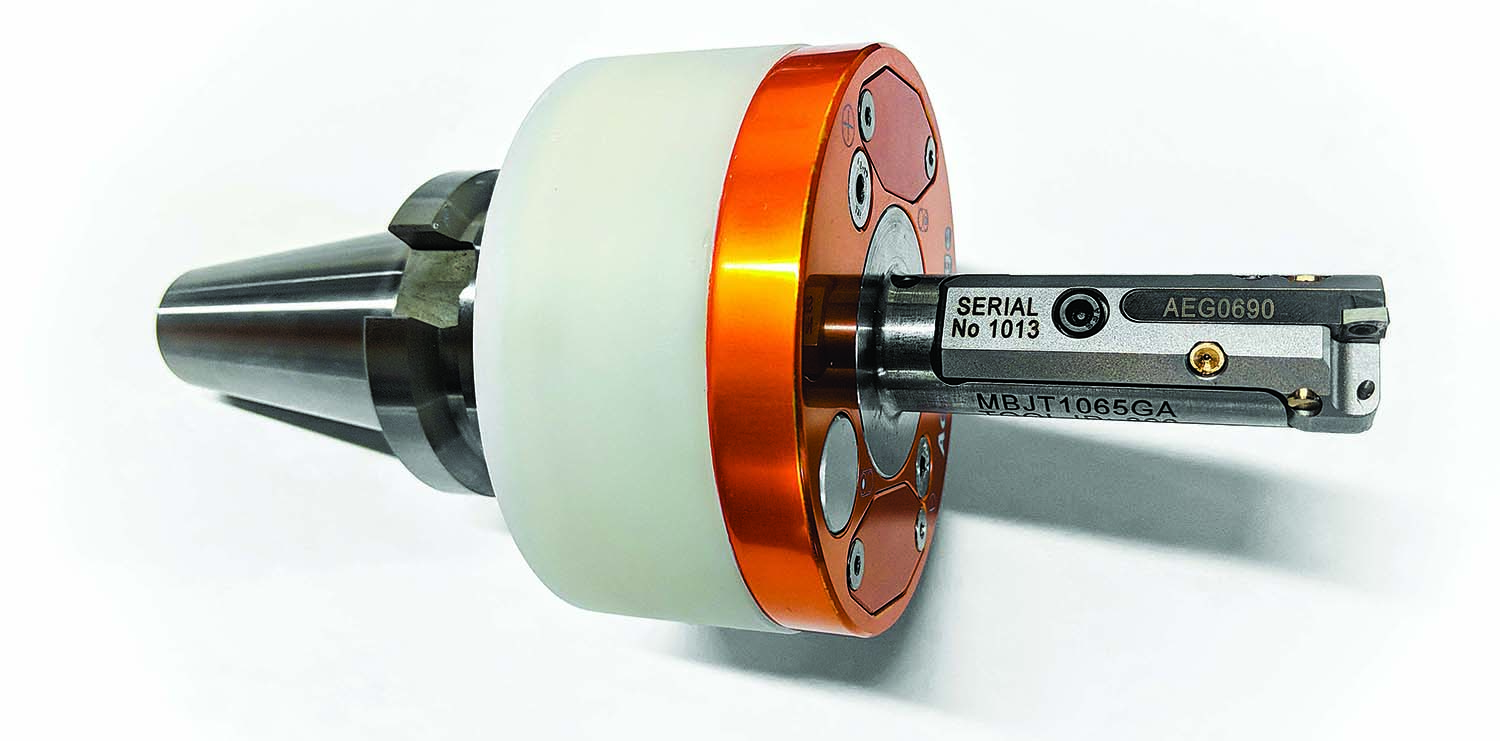
But what are the real-time benefits of automated boring bar systems that cutting tool suppliers and manufacturers must embrace to remain competitive? Before answering that, we should ask, “Why bore?”
Boring is the process of producing accurate, concentric holes in a manufacturing operation. This can be done using a single-point tool or through multiple cutting edges. Boring operations can create a perfect circle, rotating around the centerline of the machine spindle. The method applies greater flexibility and
precision when machining small-diameter holes than alternative operations, such as reaming. Boring is a technique used in many sectors, including construction, aerospace, automotive and heavy industry.
Many traditional boring operations use a wrench to dial-adjust boring units. This process is conducted manually, requires a skilled operator, is time-consuming and risks accuracy.
The blue line in the figure below represents the tolerance in a traditional boring operation. Because of the time, skill and risk involved in making an adjustment, operators often set the tool as high as possible, allowing machining to continue until the insert reaches the lower tolerance level.
While this maximizes the time spent between adjustments, the process sacrifices precision by using all the tolerance. This method of adjustment shows a high deviation of bore sizes, which are frequently outside the upper and lower tolerance limits, with minimal time operating at nominal tolerance.
With an automated boring system, adjustments are carried out based on information provided by accurate probing measurement. They are micron-level accurate and triggered when bore sizes reach the warning level. Other advantages include: automatic adjustments that remove the risk of human error; predetermined upper and lower warning limits; a lack of backlash adjustments; and adjustments that may be made in the machine carousel, reducing the need for and risks to an operator.
Ultimately, more frequent, smaller adjustments can be made (see the orange line in the figure below) compared with traditional operations (again, the blue line). Bore sizes have a low standard deviation from nominal diameter and a considerably higher Cpk.
Using an automated boring system, automatic compensating capabilities allow organizations to meet and maintain the precise tolerances required when producing component parts. Diameter changes are made without removing the tool from the machine carousel, dramatically reducing cycle time. And the ability to set predetermined warning limits provides complete control to companies, enabling them to customize processes to best suit productivity and accuracy objectives.
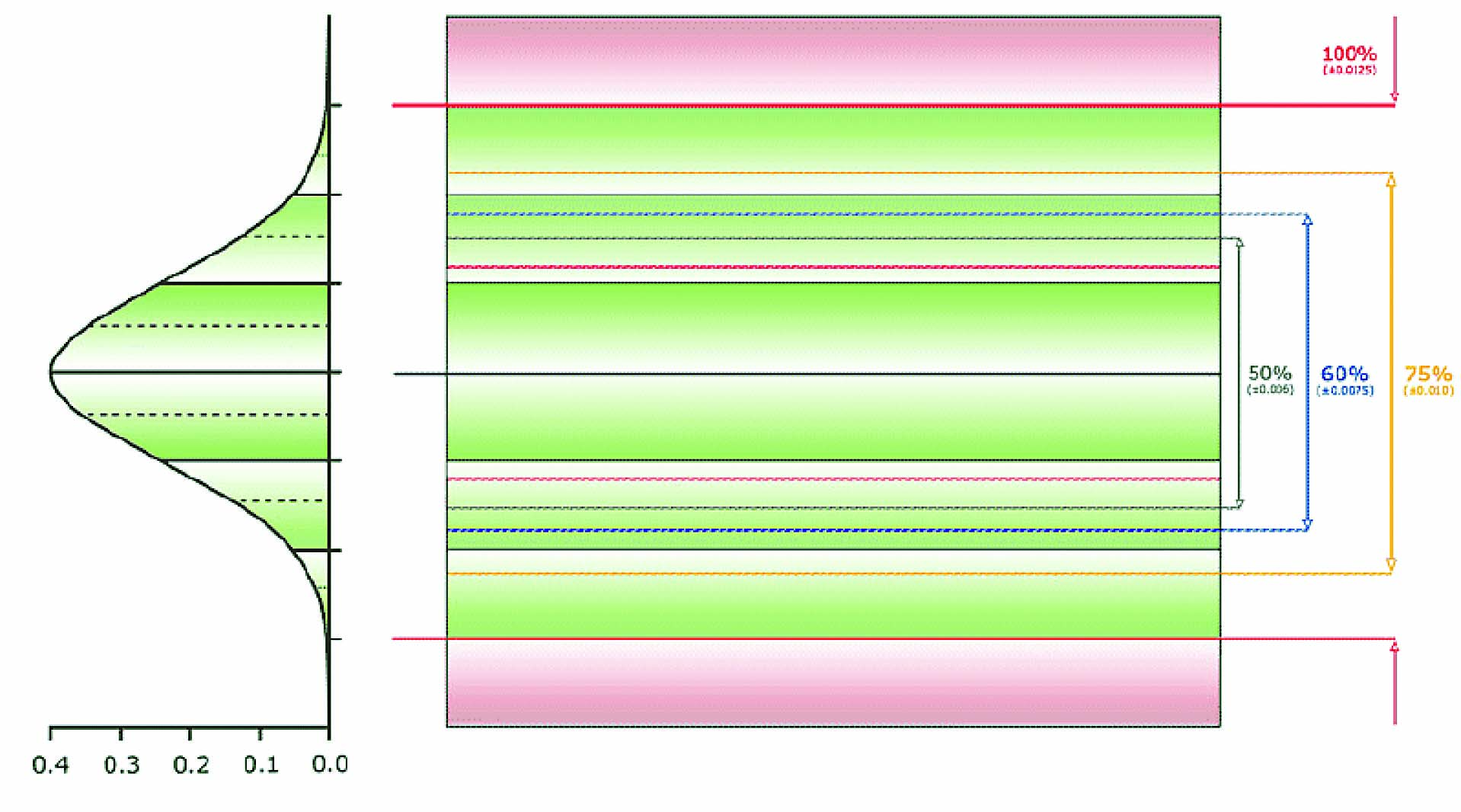
Other benefits of automated boring systems include:
Increased productivity. Businesses must strive to create a streamlined manufacturing process to increase output, reduce cycle times and meet critical lead times. Planning for availability at a shop requires transparency in all manufacturing operations. Access to real-time information permits immediate action to be taken, which optimizes performance. The ability to collect data and gain insights to improve production and embrace digital machining and Industry 4.0 is crucial.
Retrained and retained staff. It is no secret that manufacturing and associated industries face a severe skills shortage caused by an aging workforce and fewer young people entering the profession. The cost of skilled labor also has dramatically increased in recent years. An automated boring system removes the need for skilled operators to be present and perform manual adjustments. This lets employers retrain workforces and achieve staff retention.
Health and safety. Organizations must adhere to legislation, taking steps to ensure worker safety throughout the manufacturing process. With an automated system, the tool can be adjusted in the carousel, not the spindle, thus reducing the need for operator involvement. This automatic adjustment also reduces cycle time.
A controlled production process. To continually improve machining, organizations must secure an accurate, consistent and repeatable boring process. The ability to set predetermined upper and lower warning limits on bore sizes guarantees a narrow tolerance band, with low deviation of bore sizes and a higher Cpk. The implementation of an automated boring system coupled with machine-tending robots can result in a production line being overseen by a single employee, and efficiency of production may be realized by more than 50% in some cases.
Error removal. Component manufacturers strive for exceptional accuracy by meeting precise tolerances. Industries like aerospace and automotive machine components of extreme value and subsequently cannot risk scrap. Some automated boring systems can perform a trial cut, using this data to correct any inaccuracies and achieve the required diameter on the finish bore with absolute accuracy. This method ensures complete confidence to produce the “perfect” bore, which is not possible by manual adjustment measures.
Industry 4.0
New digital solutions for tooling and machine tools are changing manufacturing. One of the main tenets of Industry 4.0 is data collection. Machine tools should have sensors that collect many kinds of data, including how much a machine has operated, the conditions it has operated in and the condition of its equipment. A machine tool is only as good as the data received.
Connectivity is the hallmark of Industry 4.0 as we see the physical and digital worlds meeting on the factory floor. Automated solutions will pave the way for lights-out manufacturing. Exciting times certainly are ahead for boring bar systems.
Rigibore’s Solution
Zenith is Rigibore’s completely automated solution to produce micron-accurate bores. This fine-boring system offers unparalleled savings and a tangible return on investment by reducing labor costs, eliminating scrap and supporting 24-hour production through lights-out manufacturing.
Regardless of their sophistication, modern CNC machines cannot automatically compensate the cutting edges of a boring tool. Rigibore’s ActiveEdge tooling, combined with in-process bore measurement, has overcome this problem. The Zenith system integrates ActiveEdge tools with in-process gauging to enable a machine controller to automatically compensate for insert wear, temperature changes and material inconsistency without manual intervention and without stopping manufacturing.
Rigibore refers to this process as closed-loop tool compensation, eliminating scrap and enabling organizations to meet precise tolerances and production targets in a consistent, repeatable manner.
For more information about ActiveEdge from Rigibore, view a video presentation at cteplus.delivr.com/2b6d9
Contact Details
Related Glossary Terms
- backlash
backlash
Reaction in dynamic motion systems where potential energy that was created while the object was in motion is released when the object stops. Release of this potential energy or inertia causes the device to quickly snap backward relative to the last direction of motion. Backlash can cause a system’s final resting position to be different from what was intended and from where the control system intended to stop the device.
- bandsaw blade ( band)
bandsaw blade ( band)
Endless band, normally with serrated teeth, that serves as the cutting tool for cutoff or contour band machines.
- boring
boring
Enlarging a hole that already has been drilled or cored. Generally, it is an operation of truing the previously drilled hole with a single-point, lathe-type tool. Boring is essentially internal turning, in that usually a single-point cutting tool forms the internal shape. Some tools are available with two cutting edges to balance cutting forces.
- boring bar
boring bar
Essentially a cantilever beam that holds one or more cutting tools in position during a boring operation. Can be held stationary and moved axially while the workpiece revolves around it, or revolved and moved axially while the workpiece is held stationary, or a combination of these actions. Installed on milling, drilling and boring machines, as well as lathes and machining centers.
- computer numerical control ( CNC)
computer numerical control ( CNC)
Microprocessor-based controller dedicated to a machine tool that permits the creation or modification of parts. Programmed numerical control activates the machine’s servos and spindle drives and controls the various machining operations. See DNC, direct numerical control; NC, numerical control.
- tolerance
tolerance
Minimum and maximum amount a workpiece dimension is allowed to vary from a set standard and still be acceptable.
About the author
Rigibore Inc. is based in Mukwonago, Wisconsin. For more information, call 262-363-3922 or visit www.rigibore.com.