Rotary broaching can be an attractive alternative to conventional broaching—provided the desired form is 2" (50.8mm) in diameter or less and the machine tool being used is up to the task. The process allows machine shops to complete orders in-house with conventional machine tools rather than send them out to be finished at specialized broaching houses.
Rotary broaching produces internal and external polygon forms in one pass on the end of a part. This is quite different from conventional broaching, in which a series of increasingly larger polygon-shaped tools are pushed onto or through a part until the desired form is achieved.
This capability is making rotary broaching increasingly common. “Rotary broaching can be used just about anywhere there is a need for a polygon-shaped drive feature on a part,” said Scott Laprade, marketing manager for Genevieve Swiss Industries Inc., Westfield, Mass., which offers GenSwiss rotary broach tooling.
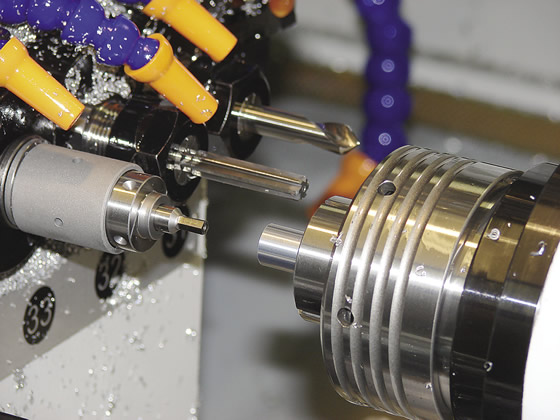
Courtesy of Genevieve Swiss Industries
Rotary broaching being performed on the subspindle of a CNC Swiss-style machine.
He added that internal rotary broaching is much more common than external. Hexagons and squares are the most common internal forms, and serrations and splines are the most common external ones, but many other polygonal forms are possible.
Rotary broaching is most effective on relatively soft materials, such as brass and aluminum, but also works well on free-machining materials, such as mild steel. It is more difficult to perform on harder materials, such as stainless steel and titanium, but it is still possible. “Brass and aluminum are the easiest to rotary broach and users can achieve upwards of 20,000 parts per broach, depending on the application,” said Kris Renner, sales and marketing director for rotary broach maker Slater Tools Inc., Clinton Township, Mich. “Stainless and titanium do reduce tool life but because it is so efficient to rotary broach on a lathe or mill, users are still satisfied with their count per broach.”
However, according to Renner, rotary broaching materials hardened above 29 HRC is not cost-effective because the broach can only produce a few parts. “The material is just too hard and it ends up prematurely chipping the broach.” She added that plastics are a developing area for rotary broaching.
The Good and the Bad
One of the reasons rotary broaching is popular is it can be performed on a variety of machine tools, including Swiss-style machines, manual and automatic lathes, milling machines and vertical machining centers. This makes the process practical for machine shops.
“Rotary broaching eliminates secondary operations,” Laprade said. “Rather than blanking out a bunch of parts and then putting them on another machine tool to put the form in, a finished product comes out of the first machine.”
In addition, rotary broaching creates a full form within seconds and achieves 0.0005" (12.7µm) accuracy or better. Feed rates when rotary broaching tend to be in the range of 0.002 to 0.004 ipr (0.051 to 0.102 mm/rev.) while running at roughly 800 to 1,500 rpm, depending on the form diameter.
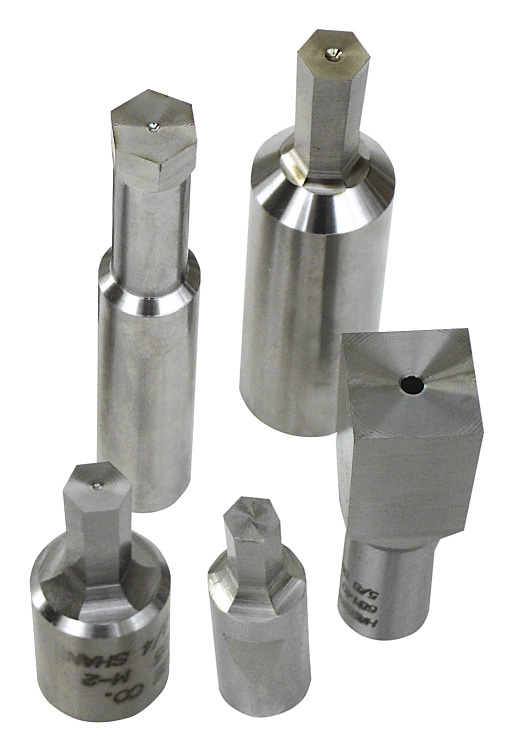
Courtesy of Hassay Savage
A sample of hexagon and square rotary broach tools.
Another advantage is long tool life. “Rotary broaching is a cutting action,” said Jeff Tryles, director of sales for Slater Tools. “You are using the cutting edge on the broach to produce the actual form, not pushing the tool. If you were pushing it, there would be a tendency for the corners to round out on the broach.”
A disadvantage of rotary broaching is that it can only create forms up to 2" in diameter. The form depth is up to 1.5 times the smallest diameter of the form.
“When you get to the upper size limit and are broaching something like steel, it requires quite a bit of thrust on the feed axis,” said David Jackson, applications engineer for machine tool builder Mazak Corp., Florence, Ky. “Too much material removal creates tool pressure that can cause the tool to fail or the machine to stall.”
“If you are attempting any large-part rotary broaching, you have to make sure the machine tool can handle the pressure,” added Bill Fletcher, vice president of sales and marketing for Hassay Savage Co., Turners Falls, Mass., a tooling manufacturer. “Some of the older machines were not built with high power drive on the servomotors, such as on the Z-axis.”
External rotary broaching requires even more pressure than internal. “You aren’t going to be doing any heavy material removal when external rotary broaching,” Laprade said. “That is why it works well on something like a spline, where the difference between the major and minor diameter is only about 0.040". Minimal material removal makes the operation run better.”
When targeting microparts, the smallest form possible is approximately 0.040"(1.02mm). The only difference in the process is the smaller the broach, the lighter the feed rate that should be used.
How it Works
Rotary broaching requires two components: a toolholder specifically for rotary broaching and a broach tool. The rotary broach holder incorporates an internal live spindle, or free-spinning bearing, that holds the broach at a 1° angle relative to the centerline of the workpiece. While either the machine spindle or the toolholder body is rotating, pressure on each corner of the broach is constantly changing. This creates a chisel-type shearing action, cutting one corner at a time as the broach is fed through the workpiece to the desired depth.
In a turning machine, the toolholder body is stationary while its internal live spindle and the broach rotate, driven by the workpiece (see graphic on next page). Because the workpiece drives the broach, the process does not require live tooling. In a milling machine, the toolholder is mounted in and rotates with the machine spindle while the internal live spindle and broach remain stationary.
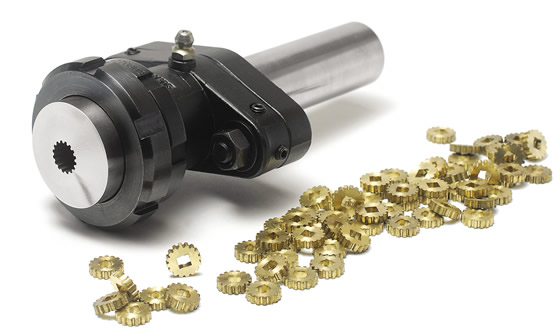
Courtesy of Slater Tools
This rotary broach toolholder and broach tool created these small brass parts with a square internal form and spline-shaped external form.
During setup, it is critical that the rotary broach is centered as close as possible to the centerline of the workpiece. Improper centering causes uneven form configurations, oversize forms, spiraling and excessive tool wear.
“If you do not use an adjustment- free toolholder, you need to take the time to align the holder,” said Brian Such, customer support group manager for machine tool builder Marubeni Citizen-Cincom Inc., Allendale, N.J. “If it is not aligned, it causes more pressure and bad cutting. Most users are not aware of this.”
Laprade added: “Being on center with rotary broaching is one of the most important objectives when setting up. Adjustment-free toolholders put the broach on centerline automatically as long as you use the correct length broach. They find the center for you.”
Starting Off
For internal rotary broaching, a pilot hole with a lead chamfer is required. “The pilot hole minimizes the amount of material the broach is actually cutting,” Slater Tools’ Renner said. “This reduces pressure on the machine. Also, the less material the broach is trying to remove, the better the tool life.”
The hole diameter should be equal to or larger than the distance across the flats on the rotary broach. “The hole should be countersunk with a lead chamfer slightly larger than the largest dimension of the broach,” Hassay Savage’s Fletcher said. “The countersink acts like a funnel and directs the broach into the proper position for cutting.” Without a chamfer on the workpiece, the broach will chip prematurely because of the pressure.
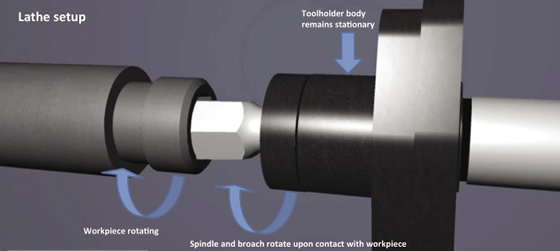
Courtesy of Slater Tools
In a lathe (above), the rotary broach toolholder body is stationary, while its internal live spindle and broach rotate upon contact with the rotating workpiece. In a mill (below), the toolholder body rotates and the workpiece is stationary, while the spindle and broach become stationary upon contact with the workpiece.
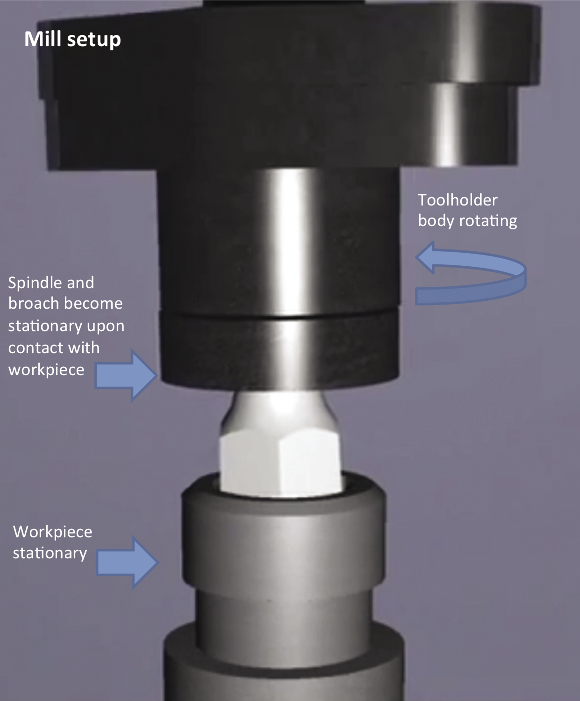
Courtesy of Slater Tools
Squares and hexagons sometimes are not required to be full form. In these cases, a larger pilot hole should be created to reduce the pressure and extend tool life because there is less material to be removed by the broach.
The depth of the pilot hole must exceed the depth of the form to be broached. This leaves enough room at the bottom of the hole to allow chips to accumulate without excessive packing.
In general, chips must be removed after rotary broaching because they cling to the part, curling down like a banana peel. “You can add an undercut or recess to the part prior to broaching to allow the chips to break cleanly,” Renner said. “Otherwise, you have to go in and turn them off the OD after external broaching, or drill or bore them out of the ID after internal broaching.”
There are some applications, however, where chips can remain in the bottom of the hole. An example is when rotary broaching a hexagon form in a fastener where the only purpose of the form is to accept a hex wrench, Fletcher noted.
Also, as the rotary broach enters into a tight-fitting hole—during a full-form cut when the pilot hole is smaller than the form’s minor diameter—there is no room for air or coolant to escape. “More shops are attempting this,” Renner said. “Pressure can build from trapped air or cutting fluid and this can cause the part to back up into the machine or the machine to alarm. A vent hole can be added to the broach to relieve this pressure. However, if you are able to open the pilot hole larger than the minor diameter, there is no need to have a vented broach.”
Rotary broaching has been around for decades, especially in the screw machine industry. However, there are still shops that have the machine tools required to perform rotary broaching that need to be made aware of that capability, according to Renner. “A lot of shops still send their jobs out to broaching houses because they don’t want to invest in a new machine,” she said. “So this is a way to bring broaching in-house. Most everyone has a lathe or a mill.” CTE
Index broaching punches its way to finished parts
Index broaching is an alternative to full-form internal rotary broaching and involves a stationary spindle and a partial form of the shape to be generated. Once hole preparation is completed, the polygon-shaped form is generated on the machine tool by making imprints of the form to the proper depth while the part is indexed to create the full form. Index broaching is performed on Swiss-style machines and is most effective at hole diameters of 3/8" (9.525mm) and under.
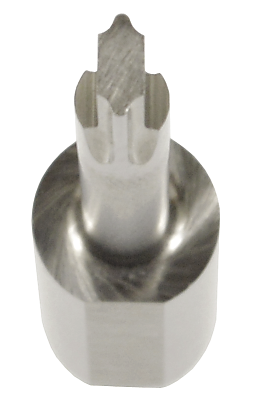
Courtesy of Hassay Savage
An index broach cuts a portion of the form as the part is indexed to produce the full form.
“Rather than cutting the entire form at once, the tool is only cutting a portion of the form,” said Bill Fletcher, vice president of sales and marketing, Hassay Savage Co. “You are basically punching. You drive the index broach into the workpiece, make an impression, remove it, index the part, reenter the hole and make the second impression, come back out, rotate the part and cut a third impression. The cut is broken into three separate sections to get the full geometry.”
The drill or boring bar used to make the pilot hole can reenter the cut and remove the chips.
Index broaching has several advantages, according to Fletcher. It is an effective alternative when rotary broaching is not practical, such as for difficult-to-machine materials and when there is limited amount of space at the bottom of the hole or when witness marks (remnants of the original pilot hole) are unacceptable.
Index broaching is also suitable for lights-out machining. “With rotary broaching, you are probably going to need at least one tool change overnight, but with index broaching, tool life skyrockets,” Fletcher said.
Another advantage is that index broaching, unlike rotary broaching, does not require a specific toolholder.
Index broaching, however, is a “new frontier,” Fletcher said. “As such, at this point only custom tools are available.”
—S. Woods
Just one point: The case for single-point broaching
An option for producing polygon-shaped forms is using an insertable, single-point broaching tool. The single-point tool does not produce the whole form at once. Rather, it removes 0.001" to 0.003" (0.0254mm to 0.0762mm) of material during each pass.
“We consider it broaching because it is essentially shaving the part to the form we want to produce,” said Jason Farthing, marketing and sales coordinator for toolmaker Horn USA Inc., Franklin, Tenn. “With each pass, the tool gets farther and farther away from centerline on the X-axis and closer to the chuck until it reaches the required depth. This decreases tool pressure and the required machine horsepower because it is not cutting all that material at one time.”
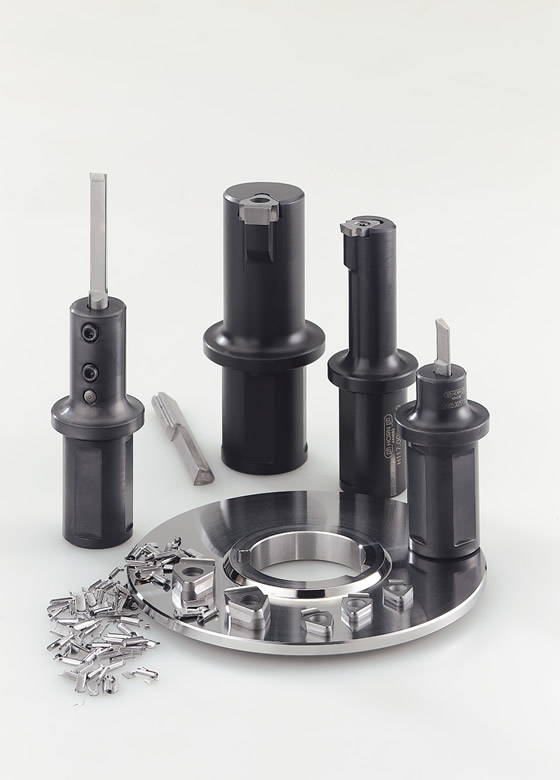
Courtesy of Horn USA
Horn USA’s insertable, single-point broaching tools remove a minimal amount of material during each pass.
Standard single-point tools are used to broach keyways, hex shapes and lobular sockets, and specials can be ordered for internal and external applications. Standard tools are available with up to a 4.5:1 ratio for the tool length to bore ID.
Like a rotary broach, a single-point broaching tool can be applied on lathes and milling machines. “The tool allows users to eliminate secondary operations or the need to subcontract work,” Farthing said.
A relief groove, or undercut, must be machined into the part to create a ramp-down exit from the cut at the end of the broached area in order to evacuate chips.
Single-point broaching tools up to 0.551" (14mm) wide are available as standards. “If the user is producing a wider keyway, he needs a Y-axis to step back and forth,” Farthing said. “That is easy to do on a mill, but a lathe might have only two axes—Z and X. Without the Y-axis, the user would have to go to a wider, custom tool.”
Whether using a lathe or a mill for this process, it is important that it have a mechanical spindle lock. “Generally, if the machine has a C-axis, it has a mechanical lock on the spindle,” Farthing said.
Most single-point tools have a round shank with four flats for direct mounting in lathes and milling machines. The tool can be oriented in all four directions.
Standard tools for mounting in some live tooling (reciprocating) attachments, which allow a tool to rapidly move back and forth, are available as well. “However, reciprocating attachments have a limit on their stroke. They are made to drive only a small amount of material,” Farthing said.
—S. Woods
Contributors
Genevieve Swiss Industries Inc.
(413) 562-4800
www.genswiss.com
Hassay Savage Co.
(800) 247-2024
www.hassay-savage.com
Horn USA Inc.
(888) 818-4676
www.hornusa.com
Marubeni Citizen-Cincom Inc.
(201) 818-0100
www.marucit.com
Mazak Corp.
(859) 342-1700
www.mazakusa.com
Slater Tools Inc.
(586) 465-5000
www.slatertools.com
Related Glossary Terms
- boring
boring
Enlarging a hole that already has been drilled or cored. Generally, it is an operation of truing the previously drilled hole with a single-point, lathe-type tool. Boring is essentially internal turning, in that usually a single-point cutting tool forms the internal shape. Some tools are available with two cutting edges to balance cutting forces.
- boring bar
boring bar
Essentially a cantilever beam that holds one or more cutting tools in position during a boring operation. Can be held stationary and moved axially while the workpiece revolves around it, or revolved and moved axially while the workpiece is held stationary, or a combination of these actions. Installed on milling, drilling and boring machines, as well as lathes and machining centers.
- broach
broach
Tapered tool, with a series of teeth of increasing length, that is pushed or pulled into a workpiece, successively removing small amounts of metal to enlarge a hole, slot or other opening to final size.
- broaching
broaching
Operation in which a cutter progressively enlarges a slot or hole or shapes a workpiece exterior. Low teeth start the cut, intermediate teeth remove the majority of the material and high teeth finish the task. Broaching can be a one-step operation, as opposed to milling and slotting, which require repeated passes. Typically, however, broaching also involves multiple passes.
- centering
centering
1. Process of locating the center of a workpiece to be mounted on centers. 2. Process of mounting the workpiece concentric to the machine spindle. See centers.
- centers
centers
Cone-shaped pins that support a workpiece by one or two ends during machining. The centers fit into holes drilled in the workpiece ends. Centers that turn with the workpiece are called “live” centers; those that do not are called “dead” centers.
- chuck
chuck
Workholding device that affixes to a mill, lathe or drill-press spindle. It holds a tool or workpiece by one end, allowing it to be rotated. May also be fitted to the machine table to hold a workpiece. Two or more adjustable jaws actually hold the tool or part. May be actuated manually, pneumatically, hydraulically or electrically. See collet.
- computer numerical control ( CNC)
computer numerical control ( CNC)
Microprocessor-based controller dedicated to a machine tool that permits the creation or modification of parts. Programmed numerical control activates the machine’s servos and spindle drives and controls the various machining operations. See DNC, direct numerical control; NC, numerical control.
- coolant
coolant
Fluid that reduces temperature buildup at the tool/workpiece interface during machining. Normally takes the form of a liquid such as soluble or chemical mixtures (semisynthetic, synthetic) but can be pressurized air or other gas. Because of water’s ability to absorb great quantities of heat, it is widely used as a coolant and vehicle for various cutting compounds, with the water-to-compound ratio varying with the machining task. See cutting fluid; semisynthetic cutting fluid; soluble-oil cutting fluid; synthetic cutting fluid.
- countersink
countersink
Tool that cuts a sloped depression at the top of a hole to permit a screw head or other object to rest flush with the surface of the workpiece.
- cutting fluid
cutting fluid
Liquid used to improve workpiece machinability, enhance tool life, flush out chips and machining debris, and cool the workpiece and tool. Three basic types are: straight oils; soluble oils, which emulsify in water; and synthetic fluids, which are water-based chemical solutions having no oil. See coolant; semisynthetic cutting fluid; soluble-oil cutting fluid; synthetic cutting fluid.
- feed
feed
Rate of change of position of the tool as a whole, relative to the workpiece while cutting.
- gang cutting ( milling)
gang cutting ( milling)
Machining with several cutters mounted on a single arbor, generally for simultaneous cutting.
- inner diameter ( ID)
inner diameter ( ID)
Dimension that defines the inside diameter of a cavity or hole. See OD, outer diameter.
- lathe
lathe
Turning machine capable of sawing, milling, grinding, gear-cutting, drilling, reaming, boring, threading, facing, chamfering, grooving, knurling, spinning, parting, necking, taper-cutting, and cam- and eccentric-cutting, as well as step- and straight-turning. Comes in a variety of forms, ranging from manual to semiautomatic to fully automatic, with major types being engine lathes, turning and contouring lathes, turret lathes and numerical-control lathes. The engine lathe consists of a headstock and spindle, tailstock, bed, carriage (complete with apron) and cross slides. Features include gear- (speed) and feed-selector levers, toolpost, compound rest, lead screw and reversing lead screw, threading dial and rapid-traverse lever. Special lathe types include through-the-spindle, camshaft and crankshaft, brake drum and rotor, spinning and gun-barrel machines. Toolroom and bench lathes are used for precision work; the former for tool-and-die work and similar tasks, the latter for small workpieces (instruments, watches), normally without a power feed. Models are typically designated according to their “swing,” or the largest-diameter workpiece that can be rotated; bed length, or the distance between centers; and horsepower generated. See turning machine.
- milling
milling
Machining operation in which metal or other material is removed by applying power to a rotating cutter. In vertical milling, the cutting tool is mounted vertically on the spindle. In horizontal milling, the cutting tool is mounted horizontally, either directly on the spindle or on an arbor. Horizontal milling is further broken down into conventional milling, where the cutter rotates opposite the direction of feed, or “up” into the workpiece; and climb milling, where the cutter rotates in the direction of feed, or “down” into the workpiece. Milling operations include plane or surface milling, endmilling, facemilling, angle milling, form milling and profiling.
- milling machine ( mill)
milling machine ( mill)
Runs endmills and arbor-mounted milling cutters. Features include a head with a spindle that drives the cutters; a column, knee and table that provide motion in the three Cartesian axes; and a base that supports the components and houses the cutting-fluid pump and reservoir. The work is mounted on the table and fed into the rotating cutter or endmill to accomplish the milling steps; vertical milling machines also feed endmills into the work by means of a spindle-mounted quill. Models range from small manual machines to big bed-type and duplex mills. All take one of three basic forms: vertical, horizontal or convertible horizontal/vertical. Vertical machines may be knee-type (the table is mounted on a knee that can be elevated) or bed-type (the table is securely supported and only moves horizontally). In general, horizontal machines are bigger and more powerful, while vertical machines are lighter but more versatile and easier to set up and operate.
- milling machine ( mill)2
milling machine ( mill)
Runs endmills and arbor-mounted milling cutters. Features include a head with a spindle that drives the cutters; a column, knee and table that provide motion in the three Cartesian axes; and a base that supports the components and houses the cutting-fluid pump and reservoir. The work is mounted on the table and fed into the rotating cutter or endmill to accomplish the milling steps; vertical milling machines also feed endmills into the work by means of a spindle-mounted quill. Models range from small manual machines to big bed-type and duplex mills. All take one of three basic forms: vertical, horizontal or convertible horizontal/vertical. Vertical machines may be knee-type (the table is mounted on a knee that can be elevated) or bed-type (the table is securely supported and only moves horizontally). In general, horizontal machines are bigger and more powerful, while vertical machines are lighter but more versatile and easier to set up and operate.
- outer diameter ( OD)
outer diameter ( OD)
Dimension that defines the exterior diameter of a cylindrical or round part. See ID, inner diameter.
- relief
relief
Space provided behind the cutting edges to prevent rubbing. Sometimes called primary relief. Secondary relief provides additional space behind primary relief. Relief on end teeth is axial relief; relief on side teeth is peripheral relief.
- shank
shank
Main body of a tool; the portion of a drill or similar end-held tool that fits into a collet, chuck or similar mounting device.
- toolholder
toolholder
Secures a cutting tool during a machining operation. Basic types include block, cartridge, chuck, collet, fixed, modular, quick-change and rotating.
- turning
turning
Workpiece is held in a chuck, mounted on a face plate or secured between centers and rotated while a cutting tool, normally a single-point tool, is fed into it along its periphery or across its end or face. Takes the form of straight turning (cutting along the periphery of the workpiece); taper turning (creating a taper); step turning (turning different-size diameters on the same work); chamfering (beveling an edge or shoulder); facing (cutting on an end); turning threads (usually external but can be internal); roughing (high-volume metal removal); and finishing (final light cuts). Performed on lathes, turning centers, chucking machines, automatic screw machines and similar machines.
- turning machine
turning machine
Any machine that rotates a workpiece while feeding a cutting tool into it. See lathe.
- undercut
undercut
In numerical-control applications, a cut shorter than the programmed cut resulting after a command change in direction. Also a condition in generated gear teeth when any part of the fillet curve lies inside of a line drawn tangent to the working profile at its point of juncture with the fillet. Undercut may be deliberately introduced to facilitate finishing operations, as in preshaving.