END USER: Danfoss Power Solutions, (515) 239-6000, www.danfoss.com.
CHALLENGE: Efficiently deburr machined hydraulic manifolds.
SOLUTION: A machine that deburrs via thermal energy.
SOLUTION PROVIDER: Kennametal Inc., (800) 835-3668, www.kennametal.com.
Removing burrs from intersecting and cross-sectional holes while ensuring no microcontamination is an ongoing challenge for part manufacturers. A deburring method that consumes too much time leads to production bottlenecks, increased costs and a longer time to market.
Danfoss Power Solutions, Ames, Iowa, experienced those problems when manually deburring hydraulic manifolds for hydrostatic pumps, according to Operation Manager Lubos Hanulik. Made of ductile iron, the company produces about 50,000 hydraulic manifolds a year. Manually removing the 0.2mm- to 0.3mm-high (0.008 " to 0.012 ") burrs using brushes and pencils consumed 6 to 7 minutes per manifold. In addition, manual methods can result in the formation of secondary burrs and pose the risk of scratching critical part areas.
Hanulik noted the company has a cutting tool life management program in place to avoid generating larger burrs by ensuring it doesn’t apply tools with too much wear, but Danfoss needed to find a more efficient deburring method. The company tested waterjet deburring, but the technique wasn’t effective for its application. “The parts were washed but they weren’t deburred,” he said. In addition, a waterjet can fold a burr onto the part by pushing it.
After further investigation, including an examination of the best practices at other Danfoss plants in North America and Europe, the company chose an Extrude Hone TEM (thermal energy method) machine from Kennametal Inc., Latrobe, Pa.
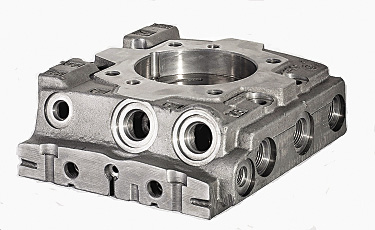
Danfoss Power Solutions removes burrs from hydraulic manifolds, such as this one, using an Extrude Hone TEM machine (below) from Kennametal. Top image courtesy Danfoss Power Solutions. Image below courtesy Kennametal.
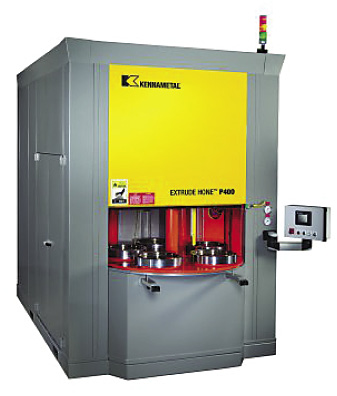
This deburring and deflashing method works on the principle of combustion and oxidation, according to Kennametal. A pressurized mixture of a combustible gas and oxygen is injected at 5 to 10 atmospheres of pressure into a containment chamber sized by the amount of material to be removed and the volume of parts in the chamber. A system ignites the gas mixture, releasing heat energy from the oxidation of fuel in a 20-millisecond energy wave that reaches a temperature of 6,000° F (3,316° C), instantly burning away burrs. Because the gas mixture engulfs the entire workpiece, all internal and external surfaces are exposed to the rapid oxidation and are deburred.
The manifolds, which have holes from about 5mm to 38.1mm (0.2 " to 1.5 ") in diameter, are deburred in about a minute, Hanulik said. Because the burrs are much smaller than the workpiece, Kennametal states that they reach their auto-ignition point instantly and are oxidized in the oxygen-rich atmosphere long before the workpiece can be harmed, with the workpiece mass acting as a heat sink.
“We did some prestudy before we purchased the machine to see if there were some dimensional changes after this thermal effect,” Hanulik said. “Originally, we didn’t see any thermal changes, but when we started to run it (on a production basis), we did.” That required adjusting the thermal deburring process to offset those changes, he added.
The removed burrs form an oxide powder, which is redistributed across the workpiece as a loosely attached dry film that is not chemically bonded to the workpiece. Hanulik explained that the oxide powder looks like rust, so it must be removed. He added that a typical removal method is with phosphoric acid, which Danfoss employed, but that method can be dangerous for workers and was not compatible with the company’s centralized wastewater treatment operation. To counter these negative effects, Danfoss switched to a Kennametal washing unit and applied a neutral product to remove the oxide powder.
The parts washer and TEM machine are part of a work cell, which also includes a parts loading/unloading robot and machining centers.
“If the machining process is under control, TEM with post-washing will give you the best process reliability and repeatability,” Hanulik said. “All of this has been achieved with fully automated robotic integration.”
Related Glossary Terms
- burning
burning
Rotary tool that removes hard or soft materials similar to a rotary file. A bur’s teeth, or flutes, have a negative rake.
- burr
burr
Stringy portions of material formed on workpiece edges during machining. Often sharp. Can be removed with hand files, abrasive wheels or belts, wire wheels, abrasive-fiber brushes, waterjet equipment or other methods.
- centers
centers
Cone-shaped pins that support a workpiece by one or two ends during machining. The centers fit into holes drilled in the workpiece ends. Centers that turn with the workpiece are called “live” centers; those that do not are called “dead” centers.
- lapping compound( powder)
lapping compound( powder)
Light, abrasive material used for finishing a surface.