Aluminum is relatively easy to machine, especially when compared to heat-resistant superalloys and titanium, but as the silicon content increases or if the material is inherently gummy, controlling chips and economically cutting aluminum can be a challenge. To meet that challenge, toolmaker Lach Diamant, Hanau, Germany, combined its »Cool Injection« coolant-delivery system with the »Plus« chipbreaker to introduce »Cool Injection-Plus« PCD monoblock milling cutters.
According to the company, the combination cutter maximizes tool life, imparts mirror surface finishes, reduces cycle times up to 50 percent and provides high machining parameters, with a feed rate up to 40.000 mm/min. (1.575 ipm) and a cutting depth up to 8mm (0.315 ") at the maximum cutting speed.
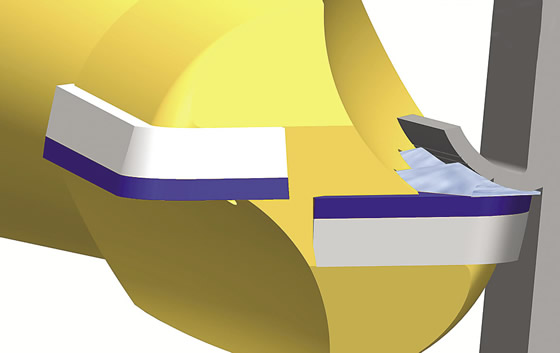
The »Cool Injection« system delivers coolant directly through the PCD cutting face. All images courtesy Lach Diamant.
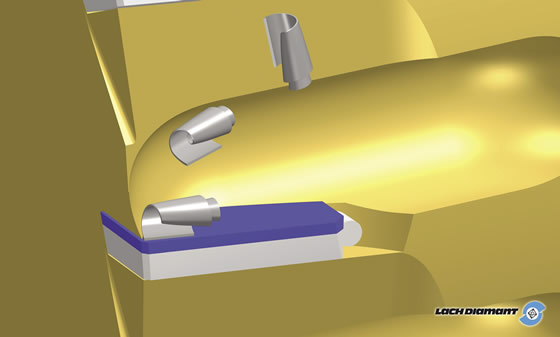
Audi developed the »Plus« chipbreaker.
The through-coolant system delivers coolant directly through the base of the substrate and PCD cutting face, so cooling occurs at the cutting edge, explained Randy Prafke, operations manager for Lach Diamond Inc. “This keeps the heat stable right at the cut.”
In addition to emulsion and oil, the tool is also suitable for cryogenics, such as liquid nitrogen and liquid CO2. However, Prafke noted it has to be a special application, such as machining difficult-to-cut materials like cobalt chrome or hard metal-matrix composites, for that to be necessary.
German automaker Audi AG developed and patented the laser-machined chipbreaker, which Lach Diamant incorporated into the cutter design through a licensing agreement. “The chipbreaker is developing the chip and getting the chip to go in the direction you want it to go so you can deal with it,” Prafke said.
The cutter concept is suitable for all aluminum processors, particularly Tier 1 and 2 automotive suppliers, but he noted potential applications are more widespread. “Cutting aluminum is what it was built to do, but I know that our mother company, Lach Diamant, has taken this tool to a lot of places. Some of the uses include facing and decking of aluminum engine blocks, heads, transmission components—basically, anywhere in which chip control and high production is in demand.”
The toolmaker reports that it assembles a »Cool Injection-Plus« PCD cutter with the adapter of the customer’s choice and balances the assembly to G2.5 grade, allowing users to mount the tool on a machine after adjustment. For more information about Lach Diamond Inc., Grand Rapids, Mich, call (800) LACH-USA or visit www.lach-dia mond.com.
About the Author: Alan Richter is editor of CTE. Contact him at (847) 714-0175 or [email protected].
Related Glossary Terms
- chipbreaker
chipbreaker
Groove or other tool geometry that breaks chips into small fragments as they come off the workpiece. Designed to prevent chips from becoming so long that they are difficult to control, catch in turning parts and cause safety problems.
- composites
composites
Materials composed of different elements, with one element normally embedded in another, held together by a compatible binder.
- coolant
coolant
Fluid that reduces temperature buildup at the tool/workpiece interface during machining. Normally takes the form of a liquid such as soluble or chemical mixtures (semisynthetic, synthetic) but can be pressurized air or other gas. Because of water’s ability to absorb great quantities of heat, it is widely used as a coolant and vehicle for various cutting compounds, with the water-to-compound ratio varying with the machining task. See cutting fluid; semisynthetic cutting fluid; soluble-oil cutting fluid; synthetic cutting fluid.
- cutting speed
cutting speed
Tangential velocity on the surface of the tool or workpiece at the cutting interface. The formula for cutting speed (sfm) is tool diameter 5 0.26 5 spindle speed (rpm). The formula for feed per tooth (fpt) is table feed (ipm)/number of flutes/spindle speed (rpm). The formula for spindle speed (rpm) is cutting speed (sfm) 5 3.82/tool diameter. The formula for table feed (ipm) is feed per tooth (ftp) 5 number of tool flutes 5 spindle speed (rpm).
- emulsion
emulsion
Suspension of one liquid in another, such as oil in water.
- feed
feed
Rate of change of position of the tool as a whole, relative to the workpiece while cutting.
- gang cutting ( milling)
gang cutting ( milling)
Machining with several cutters mounted on a single arbor, generally for simultaneous cutting.
- milling
milling
Machining operation in which metal or other material is removed by applying power to a rotating cutter. In vertical milling, the cutting tool is mounted vertically on the spindle. In horizontal milling, the cutting tool is mounted horizontally, either directly on the spindle or on an arbor. Horizontal milling is further broken down into conventional milling, where the cutter rotates opposite the direction of feed, or “up” into the workpiece; and climb milling, where the cutter rotates in the direction of feed, or “down” into the workpiece. Milling operations include plane or surface milling, endmilling, facemilling, angle milling, form milling and profiling.
- polycrystalline diamond ( PCD)
polycrystalline diamond ( PCD)
Cutting tool material consisting of natural or synthetic diamond crystals bonded together under high pressure at elevated temperatures. PCD is available as a tip brazed to a carbide insert carrier. Used for machining nonferrous alloys and nonmetallic materials at high cutting speeds.
- superalloys
superalloys
Tough, difficult-to-machine alloys; includes Hastelloy, Inconel and Monel. Many are nickel-base metals.