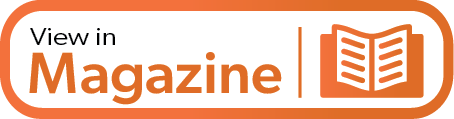
In last month’s column I showed how I put a 1" diameter axle in the rear wheel of a Harley motorcycle that originally came with a ¾" diameter axle. That was done because the bike had a big increase in horsepower and the ¾" diameter part got bent. That in turn required a custom rear brake caliper bracket and custom fixturing to make the new bracket. Figure 1 shows the new caliper bracket. Note that there are two holes through the part. The smaller hole is 1" diameter and mounts on the axle. The original equipment part didn’t have enough material to accommodate this hole safely. The larger hole is the same size and location of the original equipment bracket. There are also two 3/8-16 threaded holes for mounting the caliper. I put two studs into these holes and use that assembly to index a piece of wrought aluminum for machining. Figure 2 shows the fixture I used. Figures 3 and 4 show the work in process. The fixture plate is made from 1¼" x 5" 6061-T6 aluminum bar stock. I like this material for making fixtures because it machines quickly and doesn’t rust. I am in Massachusetts where it gets very humid in the summer and rust can be a nuisance.
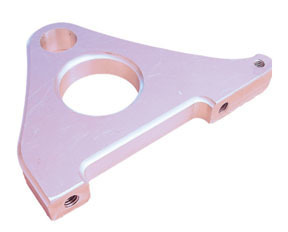
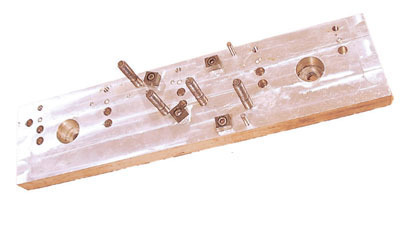
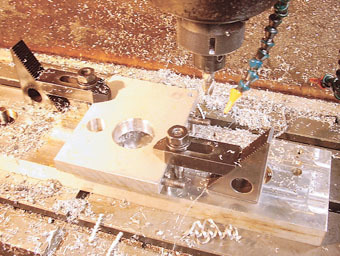
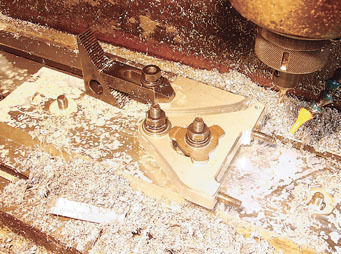
When I make a milling fixture, I start by facing one side, putting in slots and threaded holes to accept two T-slot keys; and two through holes to accept two threaded studs for clamping the fixture to the milling machine table. Then I turn the bar over, face the unfaced side, and counterbore the two through holes to accept washers and nuts from a T-slot clamping set. Now the fixture can be machined for the part being made.
This fixture has been used for other jobs and I have the geometry in a CAD/CAM program. I lay out the geometry of the part being made in the computer and see how the fixture can accommodate the new part. This fixture has nine ½" diameter holes in it. I used one of these holes as my zero, zero geometry position for machining the fixture and the part to be made. For this job, the fixture had two ¼" diameter holes drilled and reamed for two dowel pins, four 1/2-13 diameter holes for threaded studs and four 5/16-18 holes to locate fixture keys that are used as standoffs to hold the unfinished part off the face of the fixture for machining.
Making the part takes four steps. I start with a ¾" x 5" x 6¾" piece of aluminum bar stock. I clamp it to a 6" angle plate, face one edge and put in the 3/8-16 threaded holes. Two partially threaded studs are put into the holes.
Then I clamp the piece of bar to the fixture with parts from a clamping set by two of the 1/2-13 holes with the 3/8" studs against the dowel pins. Now the two through holes are machined (Figure 3).
Then I remove the unfinished part from the fixture. Remove one of the ½" studs and put in two. Now the part is clamped to the fixture with studs using the through holes. The outside profile of the part is machined (Figure 4). And there you have it. The guy I did this job for liked it. When you have a bike with a huge amount of horsepower it is a good to be able to stop the thing safely.
Related Glossary Terms
- angle plate
angle plate
Solid adjustable or nonadjustable plate that holds work at a precise angle to the spindle during machining. Also used for inspection.
- counterbore
counterbore
Tool, guided by a pilot, that expands a hole to a certain depth.
- fixture
fixture
Device, often made in-house, that holds a specific workpiece. See jig; modular fixturing.
- gang cutting ( milling)
gang cutting ( milling)
Machining with several cutters mounted on a single arbor, generally for simultaneous cutting.
- milling
milling
Machining operation in which metal or other material is removed by applying power to a rotating cutter. In vertical milling, the cutting tool is mounted vertically on the spindle. In horizontal milling, the cutting tool is mounted horizontally, either directly on the spindle or on an arbor. Horizontal milling is further broken down into conventional milling, where the cutter rotates opposite the direction of feed, or “up” into the workpiece; and climb milling, where the cutter rotates in the direction of feed, or “down” into the workpiece. Milling operations include plane or surface milling, endmilling, facemilling, angle milling, form milling and profiling.
- milling machine ( mill)
milling machine ( mill)
Runs endmills and arbor-mounted milling cutters. Features include a head with a spindle that drives the cutters; a column, knee and table that provide motion in the three Cartesian axes; and a base that supports the components and houses the cutting-fluid pump and reservoir. The work is mounted on the table and fed into the rotating cutter or endmill to accomplish the milling steps; vertical milling machines also feed endmills into the work by means of a spindle-mounted quill. Models range from small manual machines to big bed-type and duplex mills. All take one of three basic forms: vertical, horizontal or convertible horizontal/vertical. Vertical machines may be knee-type (the table is mounted on a knee that can be elevated) or bed-type (the table is securely supported and only moves horizontally). In general, horizontal machines are bigger and more powerful, while vertical machines are lighter but more versatile and easier to set up and operate.