After successfully navigating their way through all the difficulties of part making, machine shops must do the same with part marking, which presents its own set of challenges. These can be met by a number of different marking technologies, some of which have increased appeal these days thanks to developments that have made them more effective, productive and budget-friendly.
Although parts are marked for a variety of reasons, probably the main one is so they can be identified and tracked in the field, said Preben Hansen, president of Platinum Tooling Technologies Inc. in Prospect Heights, Illinois, which sells imported marking systems.
“For accountability, serial numbers and part numbers need to be on parts for long-term reference,” he said. “You want to know where they’re going and if they have to be replaced.”
Other common part markings include logos and QR codes. The latter are becoming more popular because they can hold a lot of information, said Shawn Lawlor, CEO of Dapra Corp. in Bloomfield, Connecticut, a manufacturer and distributor of dot peen and laser marking systems.
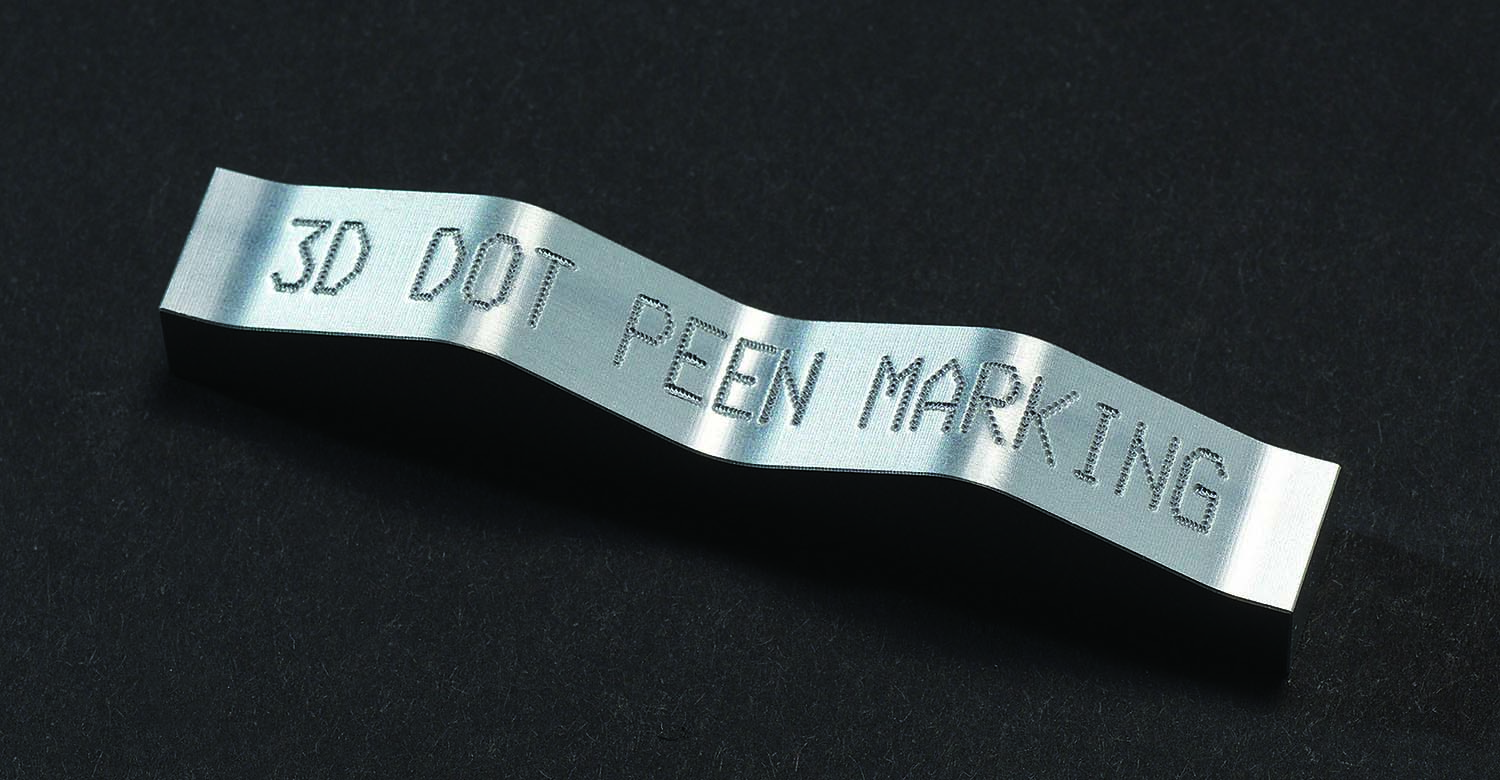
Dot peen systems create marks using a stylus that displaces material on a part surface. As for laser marking, he sees wider adoption of the technology, with fiber lasers being the preferred option of their kind for marking metal parts. He said both dot peen and laser systems excel at putting QR codes on parts.
Laser marking, however, is “very fast” compared with the mechanical dot peen process, said Mustapha Boulkouane, export sales manager at Technomark, a France-based manufacturer of laser and dot peen marking systems. (Technomark North America is in Conroe, Texas.) He pointed out that dot peen systems, with all their moving parts, require more service than laser systems as well.
Marks also can be created by chemical etching and small endmills operated by CNC machines. Lawlor describes chemical etching as a little more complex than other common marking options but useful in medical applications and others requiring marks that are free of debris.
As for marking with endmills, Hansen pointed out that this can be done while parts are still in the machine tool, eliminating the extra handling needed for laser and dot peen marking, which tend to be offline secondary operations. On the downside, he said marking with endmills is slow and creates burrs, plus endmills don’t last long in the process.
Therefore, he said, shops looking for a marking system “might want to consider better options.”
Marking Challenges
Not surprisingly, all marking systems produce the best results when marking conditions are ideal.
“Marking on a flat, consistent surface definitely provides the best mark and leads to a more cost-effective solution for marking,” Lawlor said.
On the other hand, costs rise and the task becomes more difficult when application conditions are less than optimal. He said the most challenging applications are those that require marking across uneven surfaces. While chemical etching can effectively mark these surfaces, he said both laser and dot peen systems can struggle with wavy marking surfaces due to height differences across the wave profile. So he noted that some sellers of laser systems offer 3D marking heads that can adapt to variations in surface height relative to the laser lens.
As for dot peen systems, Lawlor cautioned that they may leave only a faint mark in some places if they lack the ability to adjust to surface height differences. For applications like this, Hansen pointed out that some marking systems have a spring-loaded feature that allows them to apply sufficient force across an uneven surface to produce marks with consistent depth.
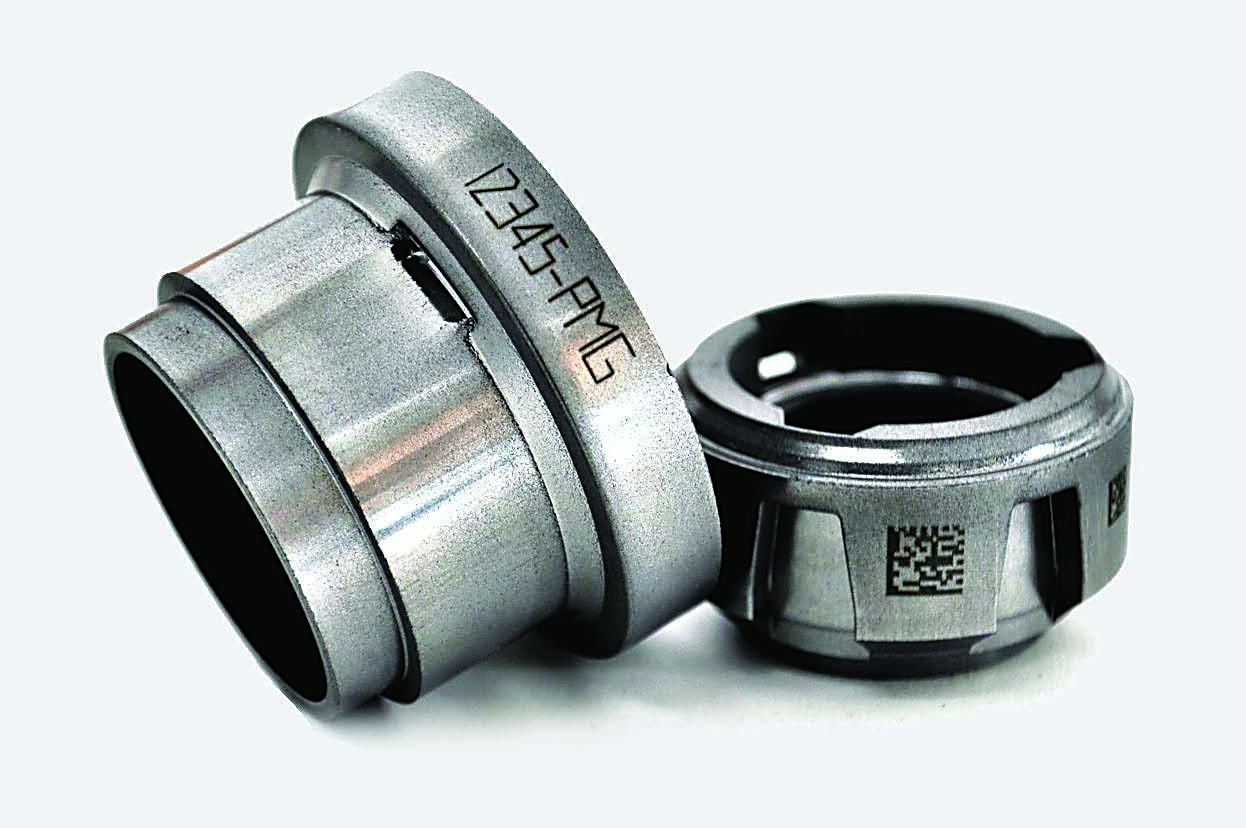
To effectively mark uneven surfaces, Technomark has equipped all its dot peen machines with Intelligent Driving Impact, a patented technology that automatically adjusts the marking force and stroke length of the stylus as necessary during the process. If a marking surface is wavy or otherwise complex, IDI makes sure the stylus will be able to follow its contour and produce a mark of even depth, according to the company.
If the parts to be marked are round, shops can employ a rotary marking tool. As a round part turns, Hansen explained, it’s in contact with the rotary tool, which is turning as well and essentially rolls the desired mark onto the part as it does so.
In addition, Lawlor pointed out that both laser and dot peen systems can be programmed to mark around the circumference of any round component.
When the challenge is marking parts with thin walls, both laser and dot peen systems are up to the job thanks to their adjustability, Boulkouane said. For these applications, he said users of dot peen systems can select a lower marking force while laser users can opt for lower frequency and power settings.
Lawlor said shops marking thin-wall parts also will appreciate the ability of fiber lasers to minimize heat-affected zones.
“Since they’re very precise,” he said, “they can mark very quickly, so the (part) is not deformed or impacted in any way by heat transfer to the base material.”
Lawlor added that chemical etching is a good option for marking thin-wall parts because it normally creates marks with minimal depth. He said this process is also effective for marking very hard materials.
Hard Problems
Laser and dot peen systems can handle hard materials as well. Thanks to their hard carbide styluses and adjustable force settings, Boulkouane said dot peen systems can mark part materials up to 63 HRC.
When the material is harder, however, “even if you select the highest force on the machine,” he said, “the marking will be light.”
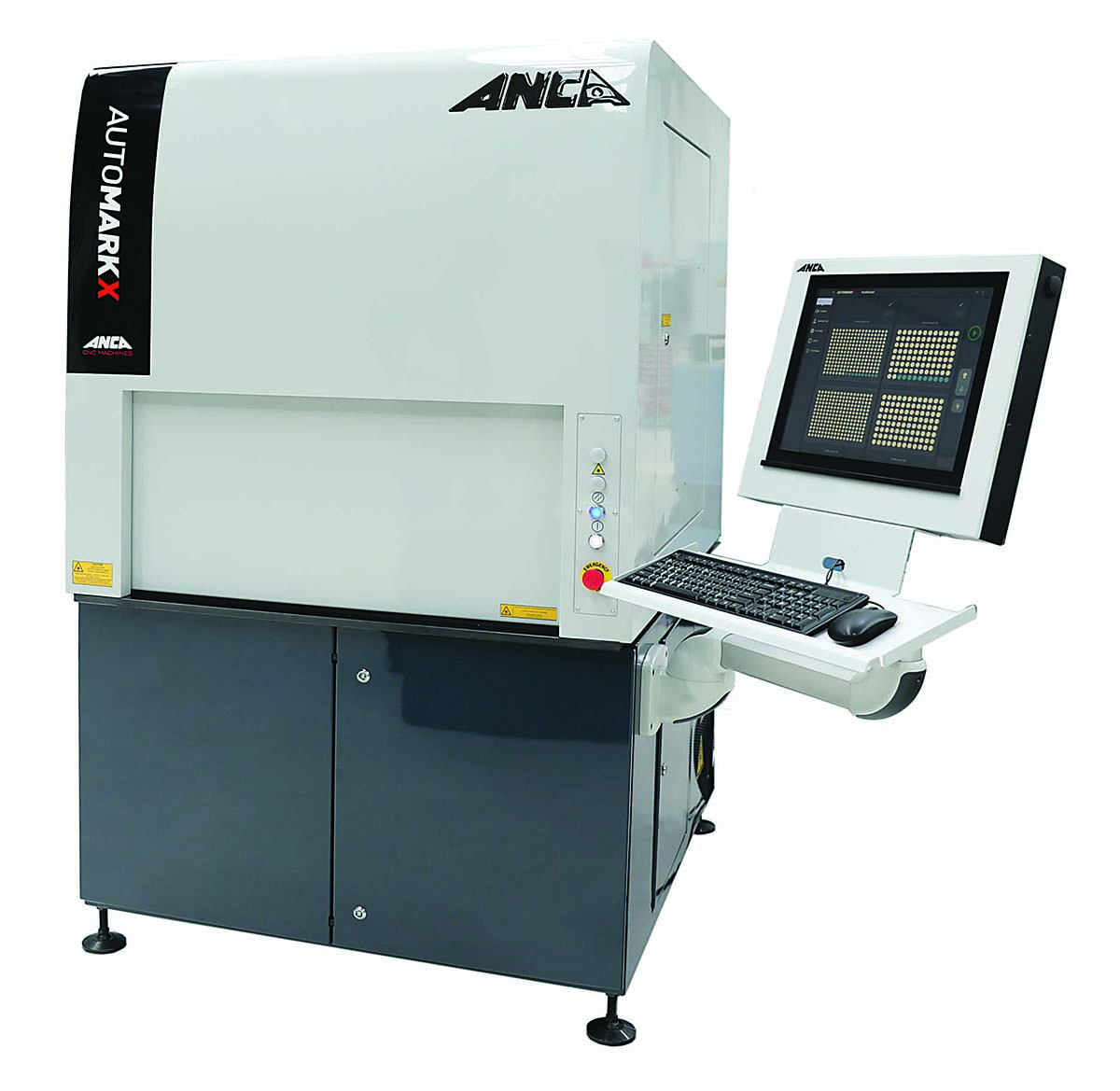
Laser users can turn up the power of their systems to mark harder materials. In addition, Boulkouane said they can make several passes to produce the desired marks.
“The precision of these machines allows you to mark text in the same position several times,” he said. “If you mark the same position several times, you will be able to (achieve) more depth.”
Generally speaking, however, dot peen systems can produce deeper marks than lasers, Boulkouane noted, which means that dot peen marks last longer.
“Depending on the area, 20 years, 30 years, even a century after the marking, you will have more chance to be able to read a mark done by dot peen than (a mark done by) a laser,” he said.
On the other hand, Hansen believes that laser marks have an edge when it comes to appearance.
“Aesthetics are important, and it’s not always easy to make a good-looking marking,” he said, adding that laser marking is very consistent and the results “are always beautiful.”
On the downside, Hansen said laser marking systems aren’t cheap and marking volumes often may be insufficient to justify the expenditure.
“Shops that are not doing marking every day or not doing high volumes are probably not going to invest in a laser marker,” he said.
Making Progress
Today, Lawlor sees more manufacturers with high marking volumes integrating automation into operations. In such processes, for example, a robot can take a part from a cart, place the part in a machine for automatic marking and then move the marked part back to the cart.
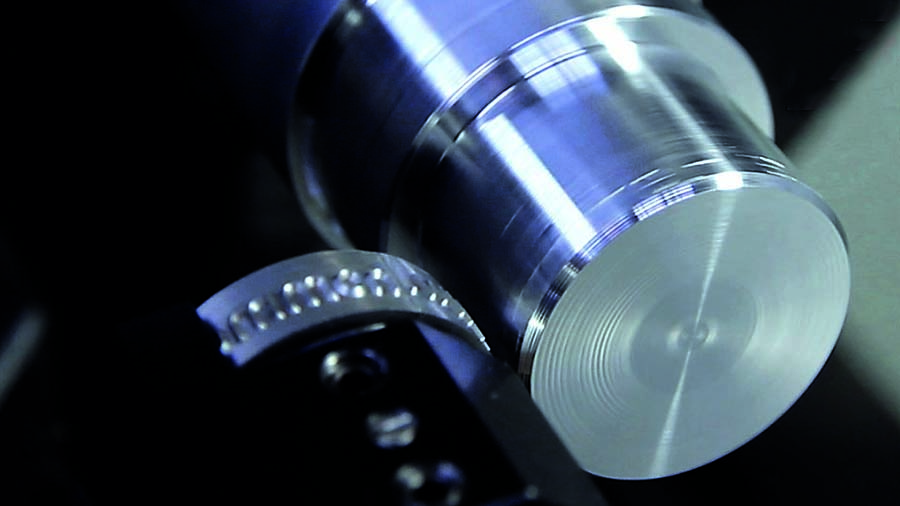
Australia-headquartered Anca, a manufacturer of CNC tool-grinding machines, recently jumped into the automated marking business with the introduction of the AutoMarkX stand-alone laser marking station.
“Laser marking is the last part of the process of manufacturing a cutting tool,” said Russell Riddiford, president of Anca Inc. in Wixom, Michigan. “So it made sense for us to introduce this model.”
An operator takes pallets of finished tools out of a grinding machine and places those same pallets into the AutoMarkX, which can handle two fully loaded pallets at a time. Inside the AutoMarkX is a Fanuc robot that picks up each tool to be marked and presents it at the right orientation to the laser beam. Once loaded, the system automatically can mark all the tools in a lights-out environment.
“That’s what most of our customers are doing with it,” Riddiford said. “After they’ve made several hundred cutting tools, they fill up the laser etcher, push the ‘go’ button and go home. Then they come in the next day, and all the tools are marked.”
In addition to pallets from Anca grinders, AutoMarkX can take pallets from competitors’ machines, thanks to special adapters.
Unveiled last year at IMTS, the $100,000 system is now “a key item for us and a very good seller in the cutting tool market,” Riddiford said.
Although laser marking systems are typically at least four times as expensive as their dot peen counterparts, Boulkouane said their price “is becoming more and more competitive.”
Lawlor attributes the price drop to the fact that overseas suppliers have begun providing lower-cost lasers. This, along with more user-friendly software, has made laser marking a more attractive option in recent years, he said.
Hansen also touts the speed and accuracy of the newest laser systems. He believes that these developments, combined with the quality of laser marks, should make the choice of marking technologies an easy one.
For high-volume marking done offline, he said, opting for a laser marker “is a no-brainer.”
Contact Details
Contact Details
Contact Details
Contact Details
Related Glossary Terms
- computer numerical control ( CNC)
computer numerical control ( CNC)
Microprocessor-based controller dedicated to a machine tool that permits the creation or modification of parts. Programmed numerical control activates the machine’s servos and spindle drives and controls the various machining operations. See DNC, direct numerical control; NC, numerical control.
- flat ( screw flat)
flat ( screw flat)
Flat surface machined into the shank of a cutting tool for enhanced holding of the tool.
- grinding
grinding
Machining operation in which material is removed from the workpiece by a powered abrasive wheel, stone, belt, paste, sheet, compound, slurry, etc. Takes various forms: surface grinding (creates flat and/or squared surfaces); cylindrical grinding (for external cylindrical and tapered shapes, fillets, undercuts, etc.); centerless grinding; chamfering; thread and form grinding; tool and cutter grinding; offhand grinding; lapping and polishing (grinding with extremely fine grits to create ultrasmooth surfaces); honing; and disc grinding.
- grinding machine
grinding machine
Powers a grinding wheel or other abrasive tool for the purpose of removing metal and finishing workpieces to close tolerances. Provides smooth, square, parallel and accurate workpiece surfaces. When ultrasmooth surfaces and finishes on the order of microns are required, lapping and honing machines (precision grinders that run abrasives with extremely fine, uniform grits) are used. In its “finishing” role, the grinder is perhaps the most widely used machine tool. Various styles are available: bench and pedestal grinders for sharpening lathe bits and drills; surface grinders for producing square, parallel, smooth and accurate parts; cylindrical and centerless grinders; center-hole grinders; form grinders; facemill and endmill grinders; gear-cutting grinders; jig grinders; abrasive belt (backstand, swing-frame, belt-roll) grinders; tool and cutter grinders for sharpening and resharpening cutting tools; carbide grinders; hand-held die grinders; and abrasive cutoff saws.
- turning
turning
Workpiece is held in a chuck, mounted on a face plate or secured between centers and rotated while a cutting tool, normally a single-point tool, is fed into it along its periphery or across its end or face. Takes the form of straight turning (cutting along the periphery of the workpiece); taper turning (creating a taper); step turning (turning different-size diameters on the same work); chamfering (beveling an edge or shoulder); facing (cutting on an end); turning threads (usually external but can be internal); roughing (high-volume metal removal); and finishing (final light cuts). Performed on lathes, turning centers, chucking machines, automatic screw machines and similar machines.
Contributors
Anca Inc.
248-926-4466
https://machines.anca.com
Dapra Corp.
800-243-3344
www.dapra.com
Platinum Tooling Technologies Inc.
847-749-0633
www.platinumtooling.com
Technomark North America
888-610-0151
www.technomark-inc.com