Though certainly good for patients, modern medical implant designs are causing complications for manufacturers in the medical industry. As the designs have become more complex to facilitate attachment to the body and make implants less invasive, they have also become more difficult and expensive to manufacture. So a need has arisen for processes capable of producing the required shapes in an efficient and economical manner.
Development of such processes was the goal of the ZykloMed project launched by four Germany-based organizations. The results, demonstrated at EMO Hannover earlier this year, are innovations that hold great promise not only for machining implant components but also for manufacturing complex parts in other industries.
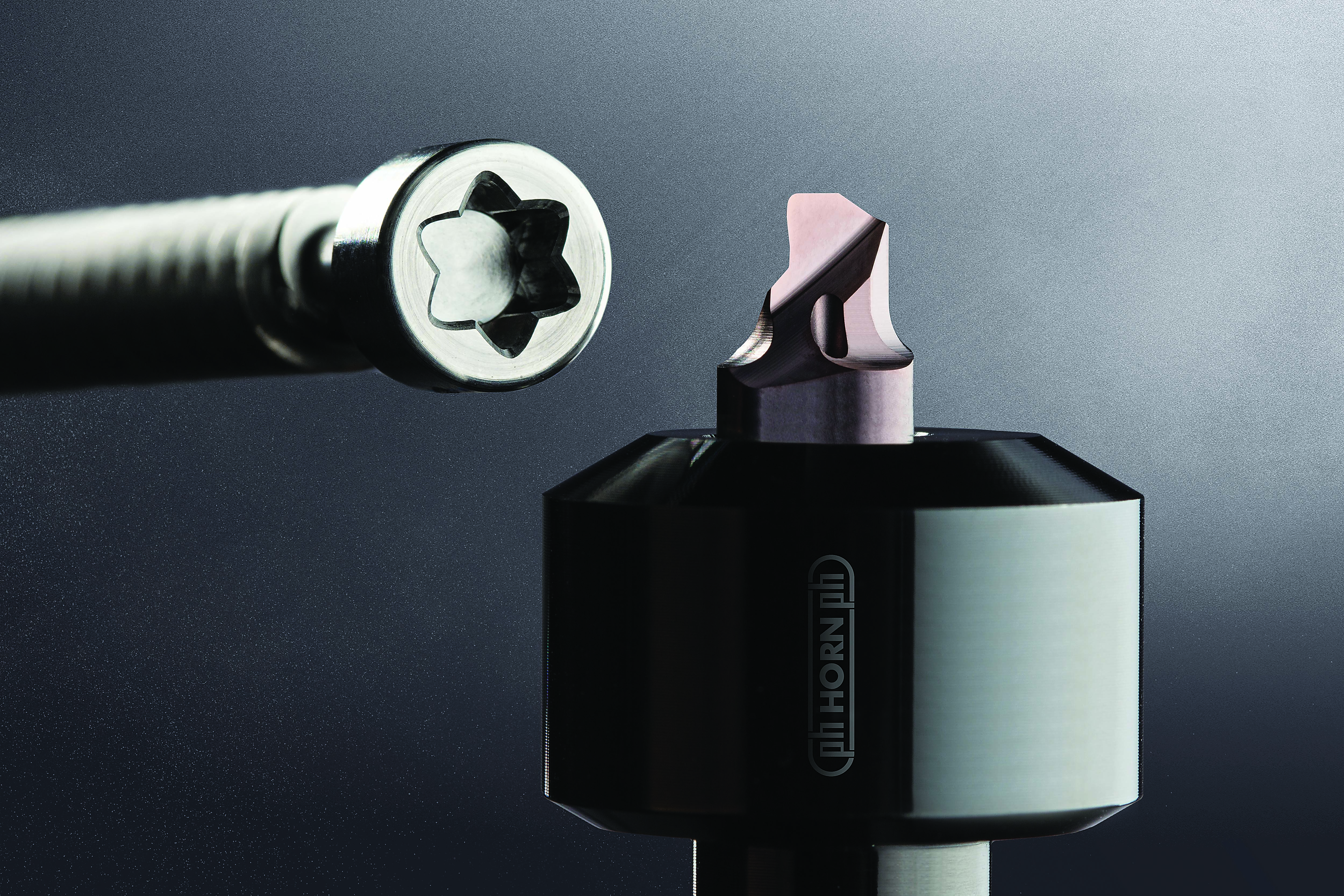
Challenges for makers of modern implant parts include machining shapes that are not circular or square and/or have more curved surfaces than older components of their kind. Machining the new parts can require several steps, driving up manufacturing time and costs.
Project Partners
To effectively deal with these issues, the ZykloMed partners — Index-Werke GmbH & Co. KG Hahn and Tessky, Paul Horn GmbH, the wbk Institute for Production Science at the Karlsruhe Institute of Technology, and Beutter Präzisions-Komponenten GmbH — focused on three different machining processes: non-circular rotary turning (NCRT), polygon turning and high-speed whirl milling. ZykloMed engineers had to come up with the right machine and tool technologies for each of the three processes, which were tested in both laboratory and near-application environments.
All three processes are based on the kinematics of rotating spindle axes during machining. Specifically, the processes require “synchronized motion of your workpiece and tool,” noted Tassilo Arndt, a wbk research associate. “Without this kinematic coupling, these processes won’t be possible.”
Depending on the application requirements, the rotational speeds of the tool and workpiece spindles could be the same or different, according to Matthias Luik, head of research and development at Horn. For ZykloMed, Horn worked on tasks such as tool design, materials and coatings.
Index and wbk also played an important role in tool design, developing a simulation program that determines the shape of the non-round tools needed for the processes, as well as the right clearance angles and number of inserts. Additionally, Index and wbk developed simulation software that comes up with the proper speed ratio for the tool and workpiece spindles. Index also supplied the machine technology for the project, as well as the special tool holders required for each of the processes, noted Volker Sellmeier, the company’s head of technology development.
As for the role of Beutter, a maker of implant components, ZykloMed engineers used the company’s facilities for testing under real manufacturing conditions. According to Luik, this testing provided critical information about the project’s simulation software, as well as tool life and materials.
Turning Technologies
As the names suggest, two of the ZykloMed processes are innovative turning techniques. In NCRT, a rotating non-circular tool is moved along the Z-axis of a rotating workpiece until the non-round tool shape is produced on the component. The speeds of the perpendicular spindles are coupled at a ratio of 1:1. According to Sellmeier, this process machines the desired non-round shapes approximately 13 times faster than conventional turning. In addition, he noted that the tools last more than 10 times longer than those normally used in turning titanium. The reason, he explained, is that the new process uses the entire circumference of the tool, while only a small part of the circumference of a normal cutting insert would be used in conventional turning. This reduces the thermal load at the cutting edge.
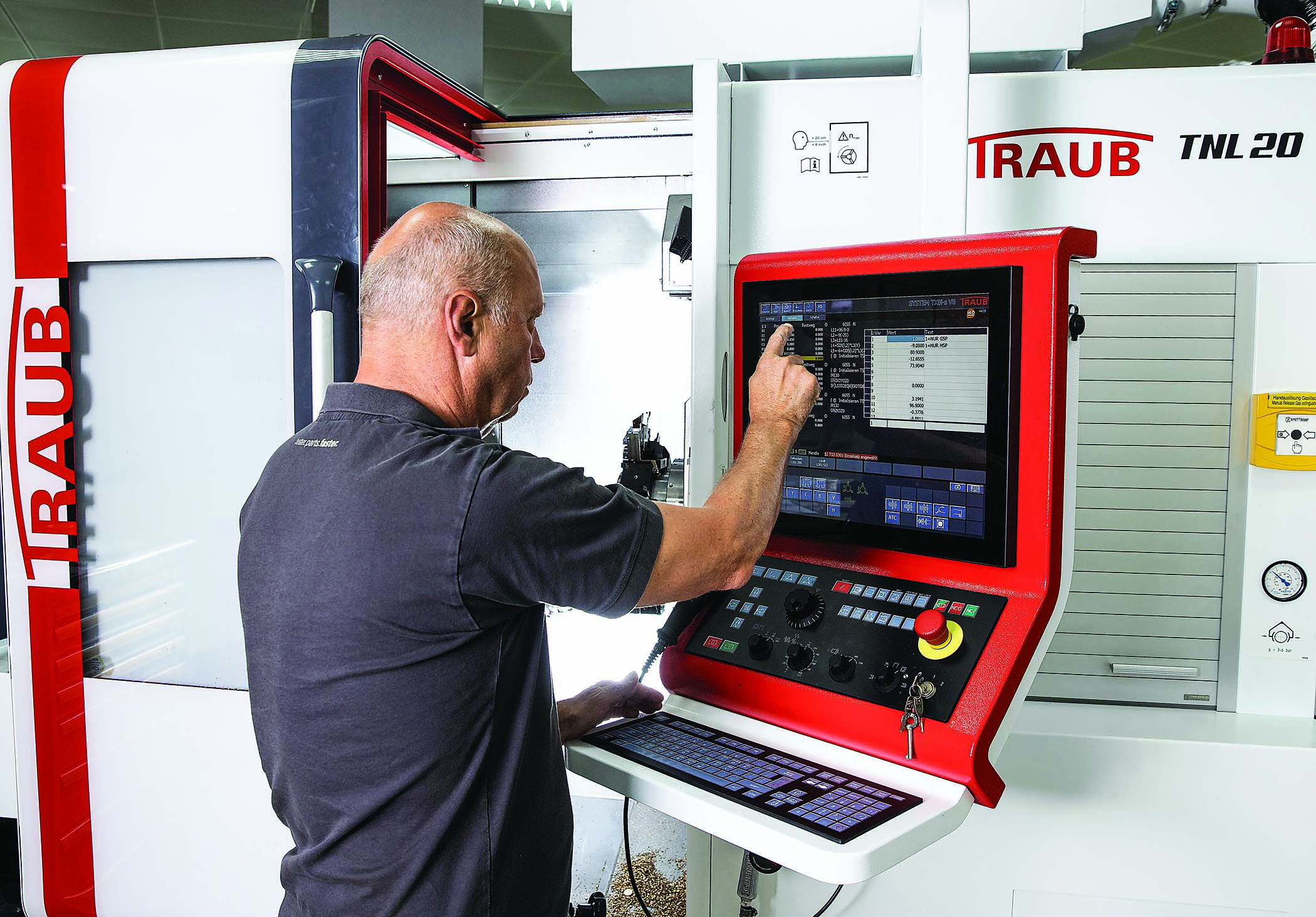
“As the tool is rotating, the point of contact on the tool (constantly) changes,” he said. “So as a point moves out (of the cut), you can cool it down with your cooling liquid. This is what gives you such an increase in tool life.”
One application for NCRT is the production of bone nails with non-round external contours that improve the fit of the nails in bone marrow. In conventional manufacturing processes, bone nails are “basically round” after turning, Arndt said, “and you'd have to mill afterwards to get a non-round contour, which is time-consuming and therefore also expensive. NCRT enables you to produce this non-round external contour in a really short amount of time.”
The other turning-based ZykloMed process, polygon turning, produces non-circular external and internal contours with the shape of a hypotrochoid. In this process, parallel tool and workpiece axes are offset from each other by a certain distance and rotated in accordance with a specific speed ratio. The offset distance and speed ratio, as well as the cutting diameter of the inserts, determine the dimension of the machined contour.
“Our idea was to use this technology to cut an internal profile which looks very similar to a Torx profile,” Sellmeier said. Such a profile, he noted, is often machined into the heads of bone screws to produce a very rigid connection with the screwdriver.
From a manufacturing standpoint, he said, the problem with Torx profiles is that machining them the conventional way is a time-consuming process in which very small end mills are needed to cut the small corners of the shapes. On the other hand, he said, a simple polygon turning tool can cut a shape very similar to a Torx profile in 9 seconds, making the process about 13 times faster than conventional Torx cutting.
Fast Milling
The third ZykloMed process, high-speed whirl milling, is a new option for producing bone screw threads. In the conventional whirling process used to machine these threads, the workpiece rotates slowly while inward-pointing inserts on the rapidly rotating whirling head do the cutting. In high-speed whirl milling, however, the conventional whirling head is replaced by one or two circular milling cutters with outward-pointing cutting edges. Another important difference in the new process is that the workpiece rotates at a high speed that is coupled with the cutter speed. The cutter-to-workpiece speed ratio depends on the number of threads and the number of cutter inserts. The direction of cutter rotation can be the same as or opposite to that of the workpiece.
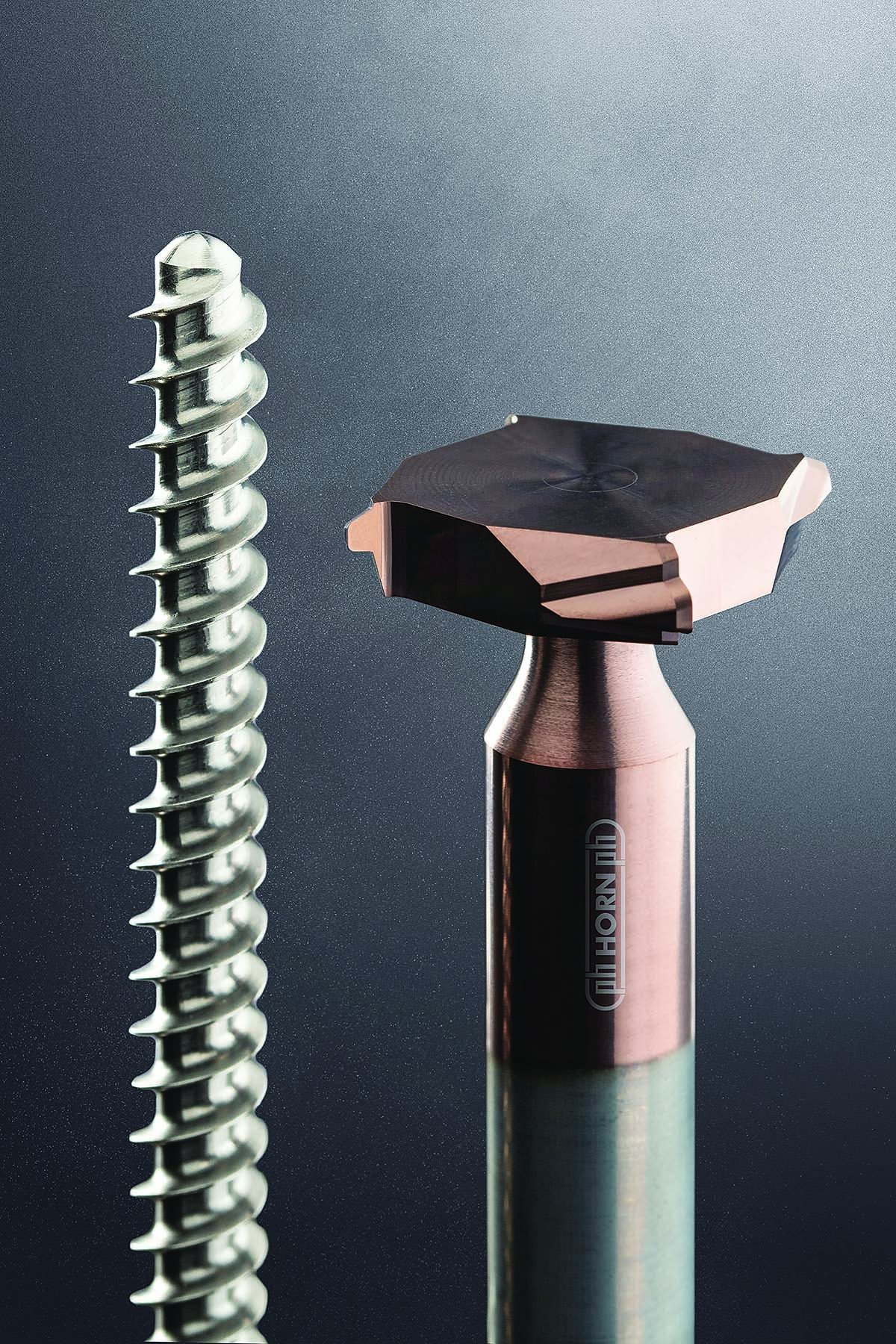
According to Sellmeier, high-speed whirl milling produces better surfaces than conventional whirling and is also much faster. In addition, the process makes it possible to economically produce bone screw threads with a variable pitch.
Sellmeier also noted that users of high-speed whirl milling have the option of cutting the fast-rotating workpiece parallel to the whirling process with a turning tool. He explained that this can be helpful in situations where the head of the bone screw being cut has a diameter that is much larger than the outer thread diameter. In these cases, the parallel turning process can be used to remove the excess material between the two diameters.
“Therefore, you need to cut a lot less material with the whirling process,” he said, adding that this extends the life of the whirling inserts.
At first, all the ZykloMed processes were tested on brass workpieces. Then the team switched to a more challenging metal, titanium. “I think we had really good performance there with all three technologies,” said Sellmeier, who believes the results should be the same with Inconel and other hard-to-machine materials.
Present and Future
In addition to implant applications, the ZykloMed team sees their processes being used for economical production of components outside the medical industry. Sellmeier reports that the team has already been approached by a manufacturer interested in trying NCRT to machine non-round cams for camshafts.
Having run successful tests in a near-series production environment, ZykloMed engineers believe they have taken a big step toward the commercialization of their processes. But some additional work remains to be done. For example, Arndt pointed out that further research is needed so that the team can definitively tell potential customers what contours can be produced by NCRT.
Soon, however, ZykloMed technology will be ready for the market, Luik predicts. “Maybe by the middle of next year,” he said, “we will sell this to the whole world.”
Contact Details
Related Glossary Terms
- clearance
clearance
Space provided behind a tool’s land or relief to prevent rubbing and subsequent premature deterioration of the tool. See land; relief.
- gang cutting ( milling)
gang cutting ( milling)
Machining with several cutters mounted on a single arbor, generally for simultaneous cutting.
- milling
milling
Machining operation in which metal or other material is removed by applying power to a rotating cutter. In vertical milling, the cutting tool is mounted vertically on the spindle. In horizontal milling, the cutting tool is mounted horizontally, either directly on the spindle or on an arbor. Horizontal milling is further broken down into conventional milling, where the cutter rotates opposite the direction of feed, or “up” into the workpiece; and climb milling, where the cutter rotates in the direction of feed, or “down” into the workpiece. Milling operations include plane or surface milling, endmilling, facemilling, angle milling, form milling and profiling.
- milling machine ( mill)
milling machine ( mill)
Runs endmills and arbor-mounted milling cutters. Features include a head with a spindle that drives the cutters; a column, knee and table that provide motion in the three Cartesian axes; and a base that supports the components and houses the cutting-fluid pump and reservoir. The work is mounted on the table and fed into the rotating cutter or endmill to accomplish the milling steps; vertical milling machines also feed endmills into the work by means of a spindle-mounted quill. Models range from small manual machines to big bed-type and duplex mills. All take one of three basic forms: vertical, horizontal or convertible horizontal/vertical. Vertical machines may be knee-type (the table is mounted on a knee that can be elevated) or bed-type (the table is securely supported and only moves horizontally). In general, horizontal machines are bigger and more powerful, while vertical machines are lighter but more versatile and easier to set up and operate.
- parallel
parallel
Strip or block of precision-ground stock used to elevate a workpiece, while keeping it parallel to the worktable, to prevent cutter/table contact.
- pitch
pitch
1. On a saw blade, the number of teeth per inch. 2. In threading, the number of threads per inch.
- turning
turning
Workpiece is held in a chuck, mounted on a face plate or secured between centers and rotated while a cutting tool, normally a single-point tool, is fed into it along its periphery or across its end or face. Takes the form of straight turning (cutting along the periphery of the workpiece); taper turning (creating a taper); step turning (turning different-size diameters on the same work); chamfering (beveling an edge or shoulder); facing (cutting on an end); turning threads (usually external but can be internal); roughing (high-volume metal removal); and finishing (final light cuts). Performed on lathes, turning centers, chucking machines, automatic screw machines and similar machines.